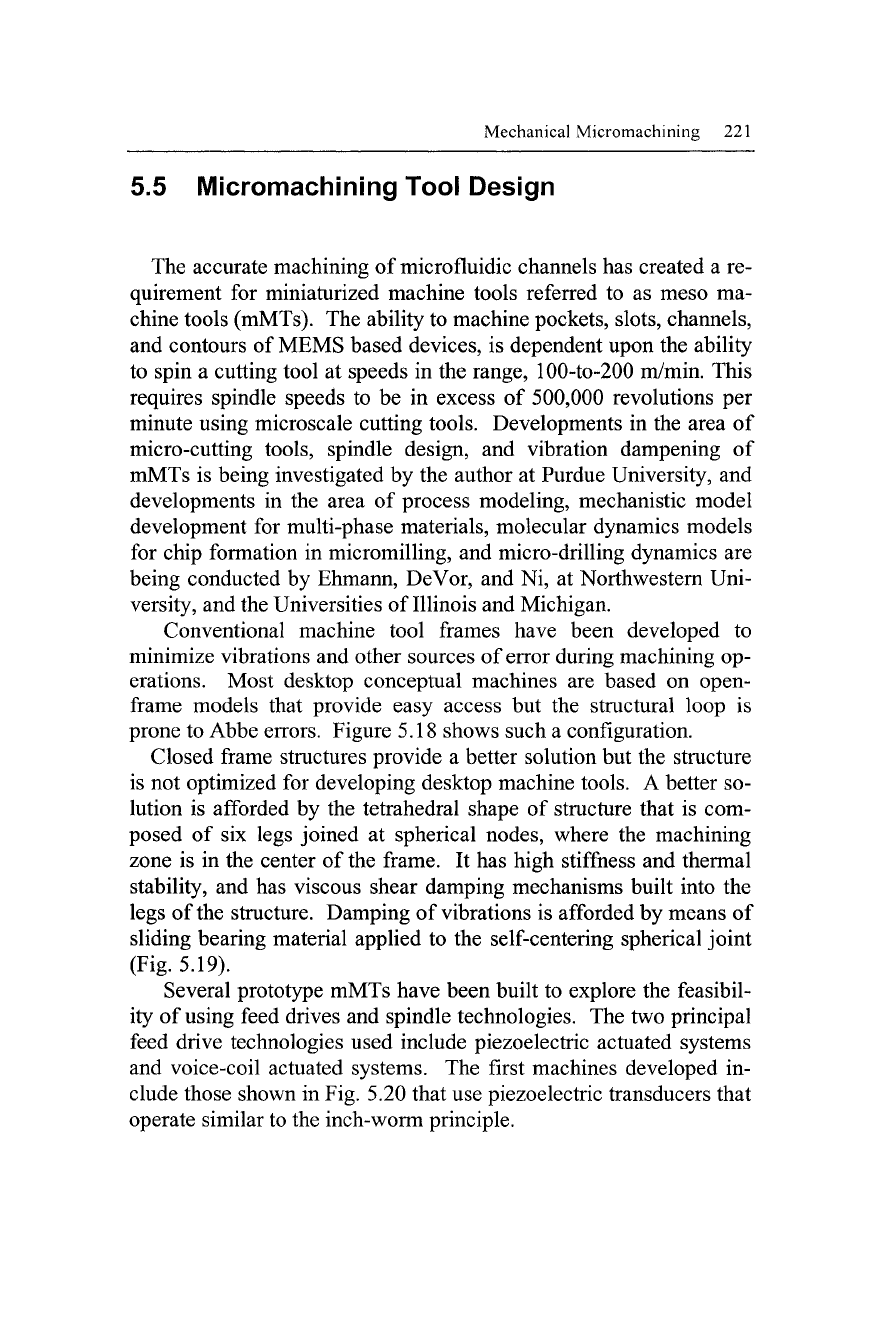
Mechanical Micromachining 221
5.5 Micromachining Tool Design
The accurate machining of microfluidic channels has created a re-
quirement for miniaturized machine tools referred to as meso ma-
chine tools (mMTs). The ability to machine pockets, slots, channels,
and contours of MEMS based devices, is dependent upon the ability
to spin a cutting tool at speeds in the range, 100-to-200 m/min. This
requires spindle speeds to be in excess of 500,000 revolutions per
minute using microscale cutting tools. Developments in the area of
micro-cutting tools, spindle design, and vibration dampening of
mMTs is being investigated by the author at Purdue University, and
developments in the area of process modeling, mechanistic model
development for multi-phase materials, molecular dynamics models
for chip formation in micromilling, and micro-drilling dynamics are
being conducted by Ehmann, DeVor, and Ni, at Northwestern Uni-
versity, and the Universities of Illinois and Michigan.
Conventional machine tool frames have been developed to
minimize vibrations and other sources of error during machining op-
erations. Most desktop conceptual machines are based on open-
frame models that provide easy access but the structural loop is
prone to Abbe errors. Figure 5.18 shows such a configuration.
Closed frame structures provide a better solution but the structure
is not optimized for developing desktop machine tools. A better so-
lution is afforded by the tetrahedral shape of structure that is com-
posed of six legs joined at spherical nodes, where the machining
zone is in the center of the frame. It has high stiffness and thermal
stability, and has viscous shear damping mechanisms built into the
legs of
the
structure. Damping of vibrations is afforded by means of
sliding bearing material applied to the self-centering spherical joint
(Fig. 5.19).
Several prototype mMTs have been built to explore the feasibil-
ity of using feed drives and spindle technologies. The two principal
feed drive technologies used include piezoelectric actuated systems
and voice-coil actuated systems. The first machines developed in-
clude those shown in Fig. 5.20 that use piezoelectric transducers that
operate similar to the inch-worm principle.