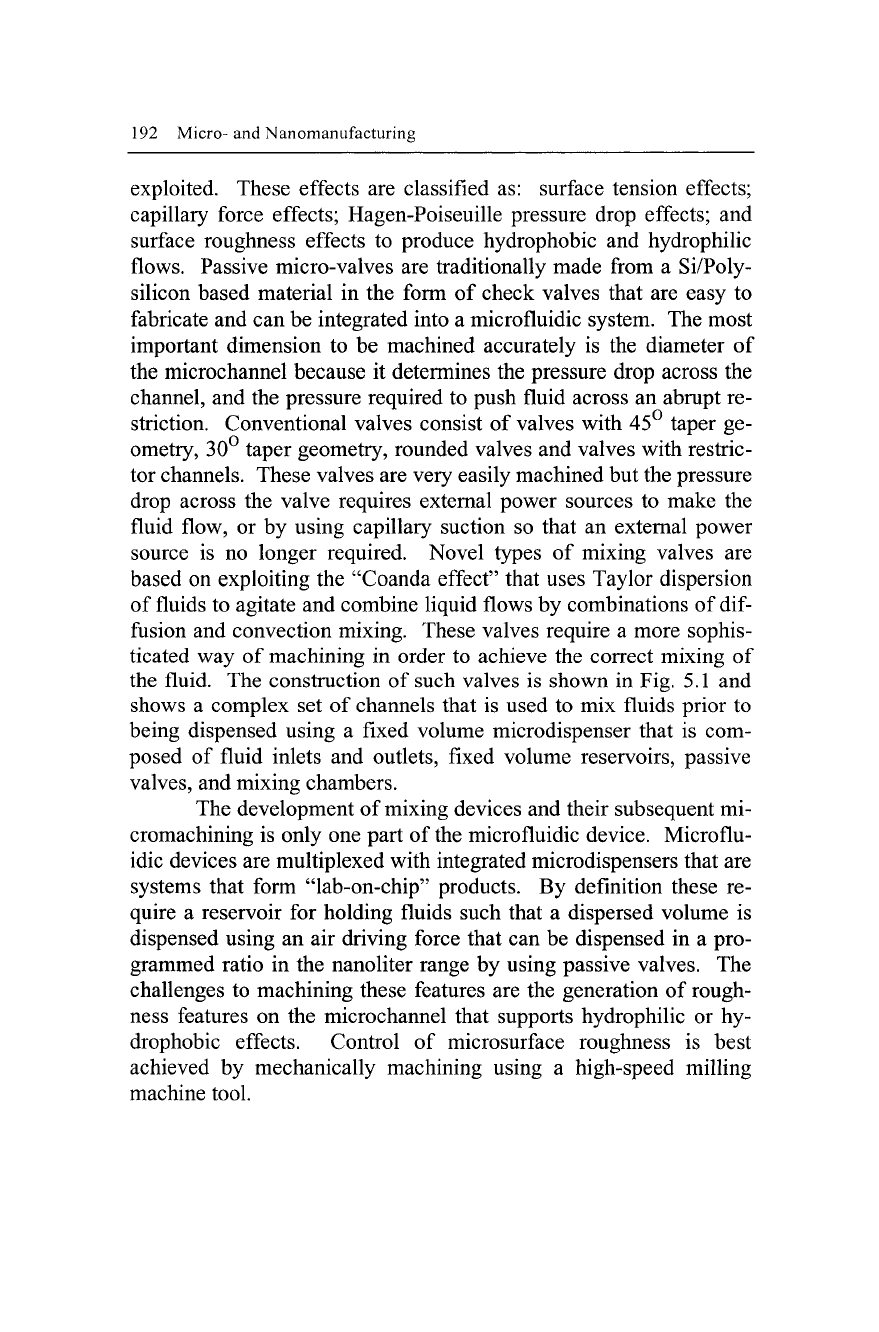
192 Micro-and Nanomanufacturing
exploited. These effects are classified as: surface tension effects;
capillary force effects; Hagen-Poiseuille pressure drop effects; and
surface roughness effects to produce hydrophobic and hydrophilic
flows.
Passive micro-valves are traditionally made from a Si/Poly-
silicon based material in the form of check valves that are easy to
fabricate and can be integrated into a microfluidic system. The most
important dimension to be machined accurately is the diameter of
the microchannel because it determines the pressure drop across the
channel, and the pressure required to push fluid across an abrupt re-
striction. Conventional valves consist of valves with 45° taper ge-
ometry, 30° taper geometry, rounded valves and valves with restric-
tor channels. These valves are very easily machined but the pressure
drop across the valve requires external power sources to make the
fluid flow, or by using capillary suction so that an external power
source is no longer required. Novel types of mixing valves are
based on exploiting the "Coanda effect" that uses Taylor dispersion
of fluids to agitate and combine liquid flows by combinations of
dif-
fusion and convection mixing. These valves require a more sophis-
ticated way of machining in order to achieve the correct mixing of
the fluid. The construction of such valves is shown in Fig. 5.1 and
shows a complex set of channels that is used to mix fluids prior to
being dispensed using a fixed volume microdispenser that is com-
posed of fluid inlets and outlets, fixed volume reservoirs, passive
valves, and mixing chambers.
The development of mixing devices and their subsequent mi-
cromachining is only one part of the microfluidic device. Microflu-
idic devices are multiplexed with integrated microdispensers that are
systems that form "lab-on-chip" products. By definition these re-
quire a reservoir for holding fluids such that a dispersed volume is
dispensed using an air driving force that can be dispensed in a pro-
grammed ratio in the nanoliter range by using passive valves. The
challenges to machining these features are the generation of rough-
ness features on the microchannel that supports hydrophilic or hy-
drophobic effects. Control of microsurface roughness is best
achieved by mechanically machining using a high-speed milling
machine tool.