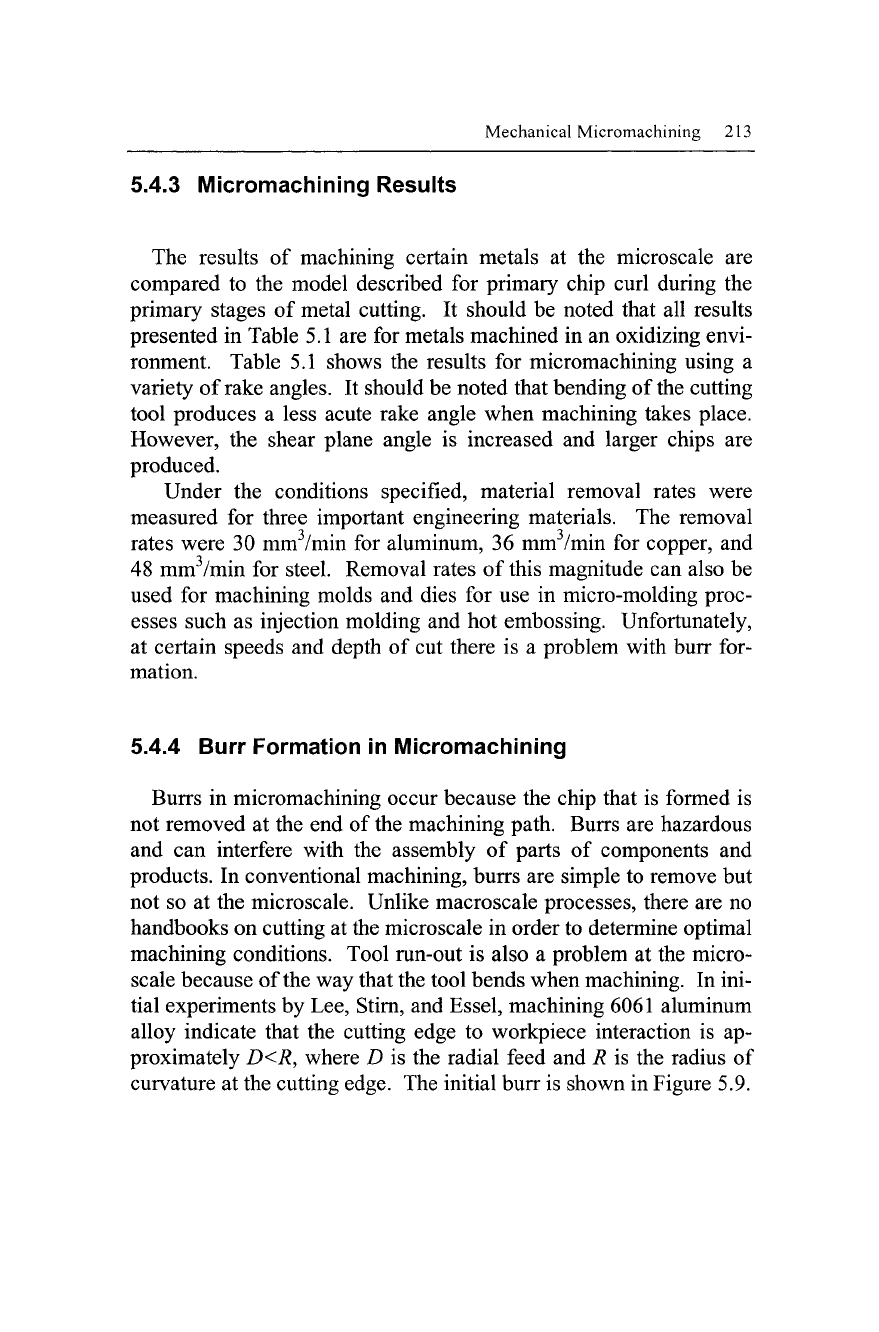
Mechanical Micromachining 213
5.4.3 Micromachining Results
The results of machining certain metals at the microscale are
compared to the model described for primary chip curl during the
primary stages of metal cutting. It should be noted that all results
presented in Table 5.1 are for metals machined in an oxidizing envi-
ronment. Table 5.1 shows the results for micromachining using a
variety of rake angles. It should be noted that bending of the cutting
tool produces a less acute rake angle when machining takes place.
However, the shear plane angle is increased and larger chips are
produced.
Under the conditions specified, material removal rates were
measured for three important engineering materials. The removal
rates were 30 mm
3
/min for aluminum, 36 mm
3
/min for copper, and
48 mmVmin for steel. Removal rates of this magnitude can also be
used for machining molds and dies for use in micro-molding proc-
esses such as injection molding and hot embossing. Unfortunately,
at certain speeds and depth of cut there is a problem with burr for-
mation.
5.4.4 Burr Formation in Micromachining
Burrs in micromachining occur because the chip that is formed is
not removed at the end of the machining path. Burrs are hazardous
and can interfere with the assembly of parts of components and
products. In conventional machining, burrs are simple to remove but
not so at the microscale. Unlike macroscale processes, there are no
handbooks on cutting at the microscale in order to determine optimal
machining conditions. Tool run-out is also a problem at the micro-
scale because of the way that the tool bends when machining. In ini-
tial experiments by Lee, Stirn, and Essel, machining 6061 aluminum
alloy indicate that the cutting edge to workpiece interaction is ap-
proximately D<R, where D is the radial feed and R is the radius of
curvature at the cutting edge. The initial burr is shown in Figure 5.9.