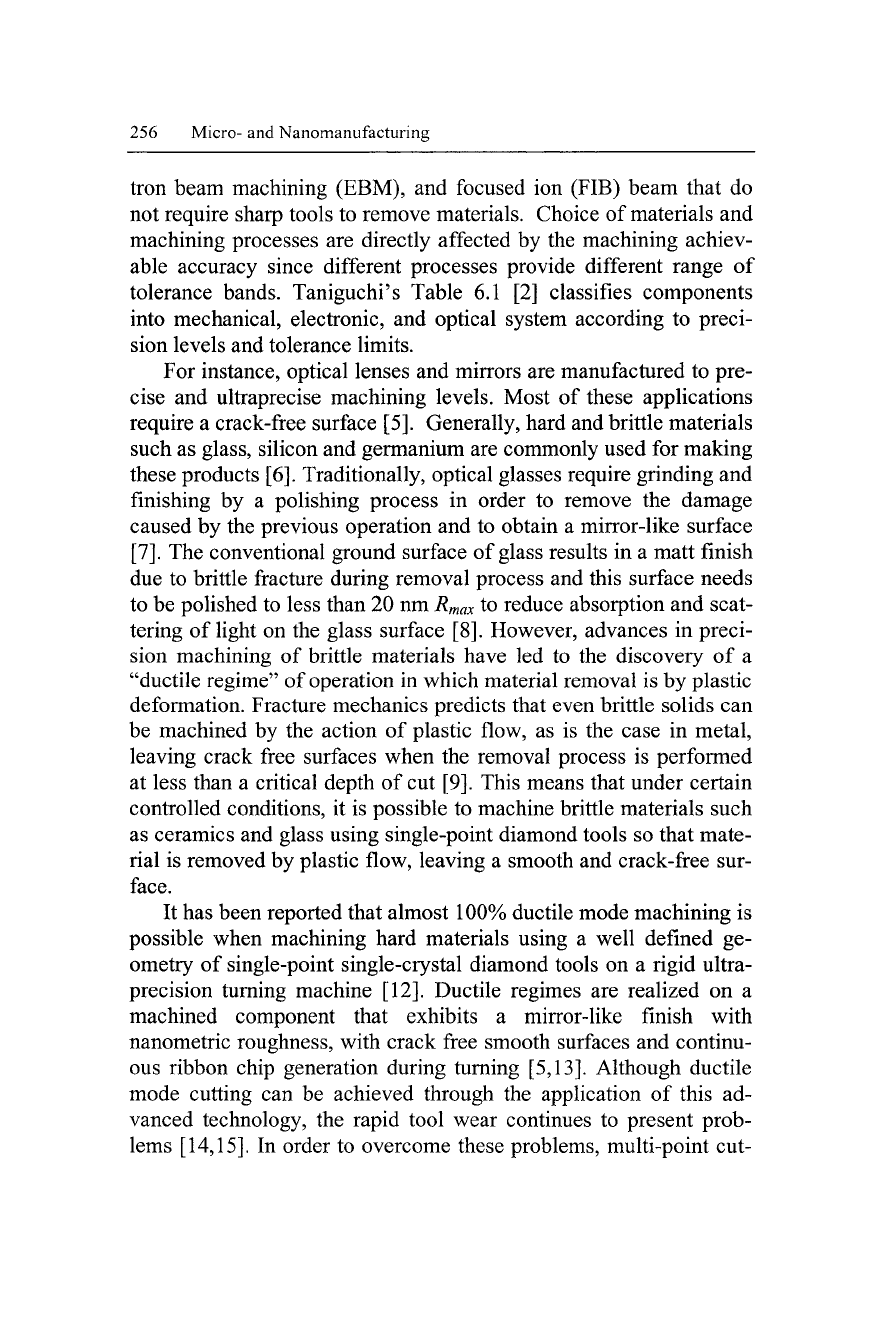
256 Micro- and Nanomanufacturing
tron beam machining (EBM), and focused ion (FIB) beam that do
not require sharp tools to remove materials. Choice of materials and
machining processes are directly affected by the machining achiev-
able accuracy since different processes provide different range of
tolerance bands. Taniguchi's Table 6.1 [2] classifies components
into mechanical, electronic, and optical system according to preci-
sion levels and tolerance limits.
For instance, optical lenses and mirrors are manufactured to pre-
cise and ultraprecise machining levels. Most of these applications
require a crack-free surface [5]. Generally, hard and brittle materials
such as glass, silicon and germanium are commonly used for making
these products [6]. Traditionally, optical glasses require grinding and
finishing by a polishing process in order to remove the damage
caused by the previous operation and to obtain a mirror-like surface
[7].
The conventional ground surface of glass results in a matt finish
due to brittle fracture during removal process and this surface needs
to be polished to less than 20 nm
R
max
to reduce absorption and scat-
tering of light on the glass surface [8]. However, advances in preci-
sion machining of brittle materials have led to the discovery of a
"ductile regime" of operation in which material removal is by plastic
deformation. Fracture mechanics predicts that even brittle solids can
be machined by the action of plastic flow, as is the case in metal,
leaving crack free surfaces when the removal process is performed
at less than a critical depth of cut [9]. This means that under certain
controlled conditions, it is possible to machine brittle materials such
as ceramics and glass using single-point diamond tools so that mate-
rial is removed by plastic flow, leaving a smooth and crack-free sur-
face.
It has been reported that almost 100% ductile mode machining is
possible when machining hard materials using a well defined ge-
ometry of single-point single-crystal diamond tools on a rigid ultra-
precision turning machine [12]. Ductile regimes are realized on a
machined component that exhibits a mirror-like finish with
nanometric roughness, with crack free smooth surfaces and continu-
ous ribbon chip generation during turning
[5,13].
Although ductile
mode cutting can be achieved through the application of this ad-
vanced technology, the rapid tool wear continues to present prob-
lems [14,15]. In order to overcome these problems, multi-point cut-