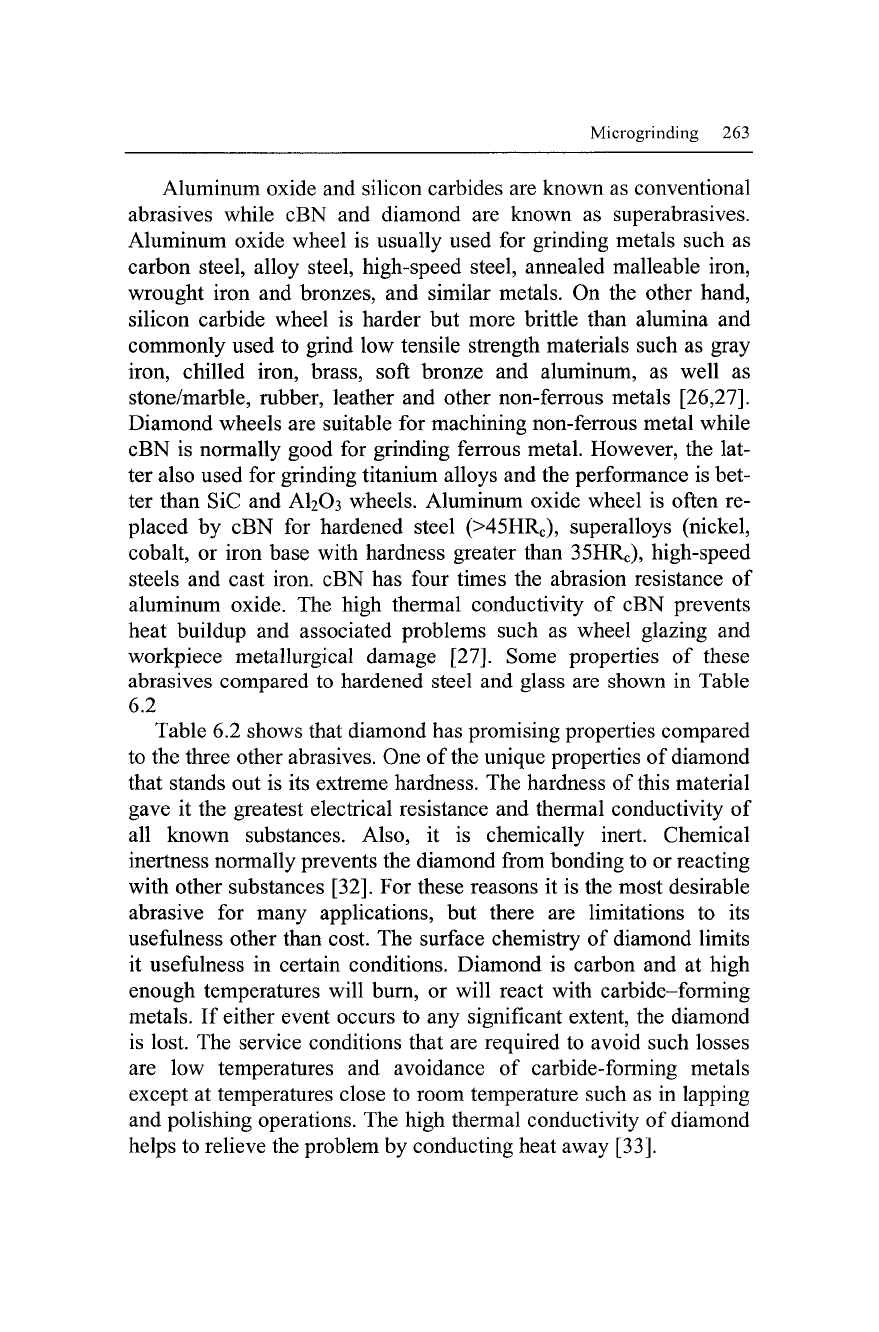
Microgrinding 263
Aluminum oxide and silicon carbides are known as conventional
abrasives while cBN and diamond are known as superabrasives.
Aluminum oxide wheel is usually used for grinding metals such as
carbon steel, alloy steel, high-speed steel, annealed malleable iron,
wrought iron and bronzes, and similar metals. On the other hand,
silicon carbide wheel is harder but more brittle than alumina and
commonly used to grind low tensile strength materials such as gray
iron, chilled iron, brass, soft bronze and aluminum, as well as
stone/marble, rubber, leather and other non-ferrous metals [26,27].
Diamond wheels are suitable for machining non-ferrous metal while
cBN is normally good for grinding ferrous metal. However, the lat-
ter also used for grinding titanium alloys and the performance is bet-
ter than SiC and AI2O3 wheels. Aluminum oxide wheel is often re-
placed by cBN for hardened steel (>45HRc), superalloys (nickel,
cobalt, or iron base with hardness greater than 35HRc), high-speed
steels and cast iron. cBN has four times the abrasion resistance of
aluminum oxide. The high thermal conductivity of cBN prevents
heat buildup and associated problems such as wheel glazing and
workpiece metallurgical damage [27]. Some properties of these
abrasives compared to hardened steel and glass are shown in Table
6.2
Table 6.2 shows that diamond has promising properties compared
to the three other abrasives. One of the unique properties of diamond
that stands out is its extreme hardness. The hardness of this material
gave it the greatest electrical resistance and thermal conductivity of
all known substances. Also, it is chemically inert. Chemical
inertness normally prevents the diamond from bonding to or reacting
with other substances [32]. For these reasons it is the most desirable
abrasive for many applications, but there are limitations to its
usefulness other than cost. The surface chemistry of diamond limits
it usefulness in certain conditions. Diamond is carbon and at high
enough temperatures will burn, or will react with carbide-forming
metals. If either event occurs to any significant extent, the diamond
is lost. The service conditions that are required to avoid such losses
are low temperatures and avoidance of carbide-forming metals
except at temperatures close to room temperature such as in lapping
and polishing operations. The high thermal conductivity of diamond
helps to relieve the problem by conducting heat away [33].