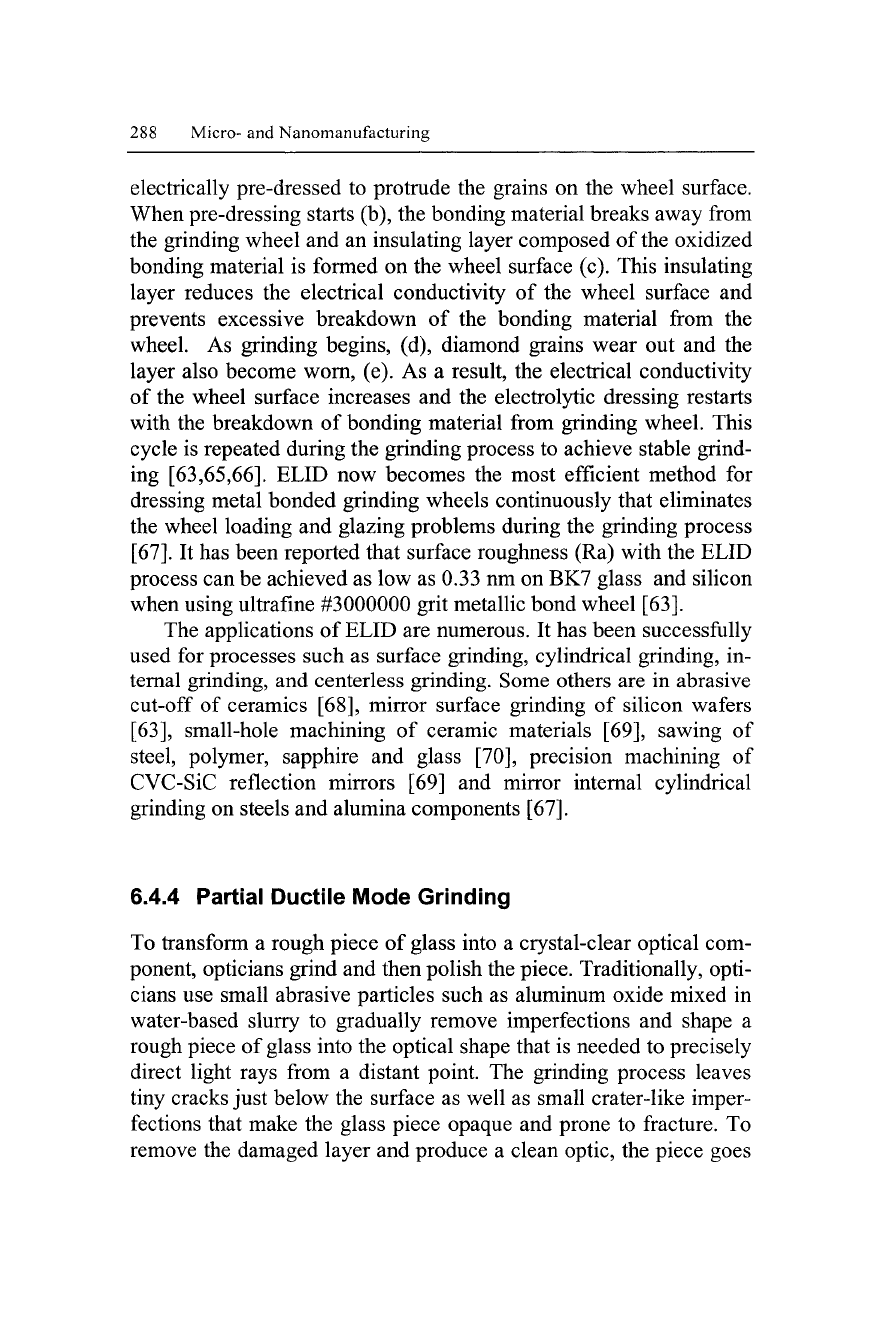
288 Micro- and Nanomanufacturing
electrically pre-dressed to protrude the grains on the wheel surface.
When pre-dressing starts (b), the bonding material breaks away from
the grinding wheel and an insulating layer composed of the oxidized
bonding material is formed on the wheel surface (c). This insulating
layer reduces the electrical conductivity of the wheel surface and
prevents excessive breakdown of the bonding material from the
wheel. As grinding begins, (d), diamond grains wear out and the
layer also become worn, (e). As a result, the electrical conductivity
of the wheel surface increases and the electrolytic dressing restarts
with the breakdown of bonding material from grinding wheel. This
cycle is repeated during the grinding process to achieve stable grind-
ing [63,65,66]. ELID now becomes the most efficient method for
dressing metal bonded grinding wheels continuously that eliminates
the wheel loading and glazing problems during the grinding process
[67].
It has been reported that surface roughness (Ra) with the ELID
process can be achieved as low as 0.33 nm on BK7 glass and silicon
when using ultrafine #3000000 grit metallic bond wheel [63].
The applications of ELID are numerous. It has been successfully
used for processes such as surface grinding, cylindrical grinding, in-
ternal grinding, and centerless grinding. Some others are in abrasive
cut-off of ceramics [68], mirror surface grinding of silicon wafers
[63],
small-hole machining of ceramic materials [69], sawing of
steel, polymer, sapphire and glass [70], precision machining of
CVC-SiC reflection mirrors [69] and mirror internal cylindrical
grinding on steels and alumina components [67].
6.4.4 Partial Ductile Mode Grinding
To transform a rough piece of glass into a crystal-clear optical com-
ponent, opticians grind and then polish the piece. Traditionally, opti-
cians use small abrasive particles such as aluminum oxide mixed in
water-based slurry to gradually remove imperfections and shape a
rough piece of glass into the optical shape that is needed to precisely
direct light rays from a distant point. The grinding process leaves
tiny cracks just below the surface as well as small crater-like imper-
fections that make the glass piece opaque and prone to fracture. To
remove the damaged layer and produce a clean optic, the piece goes