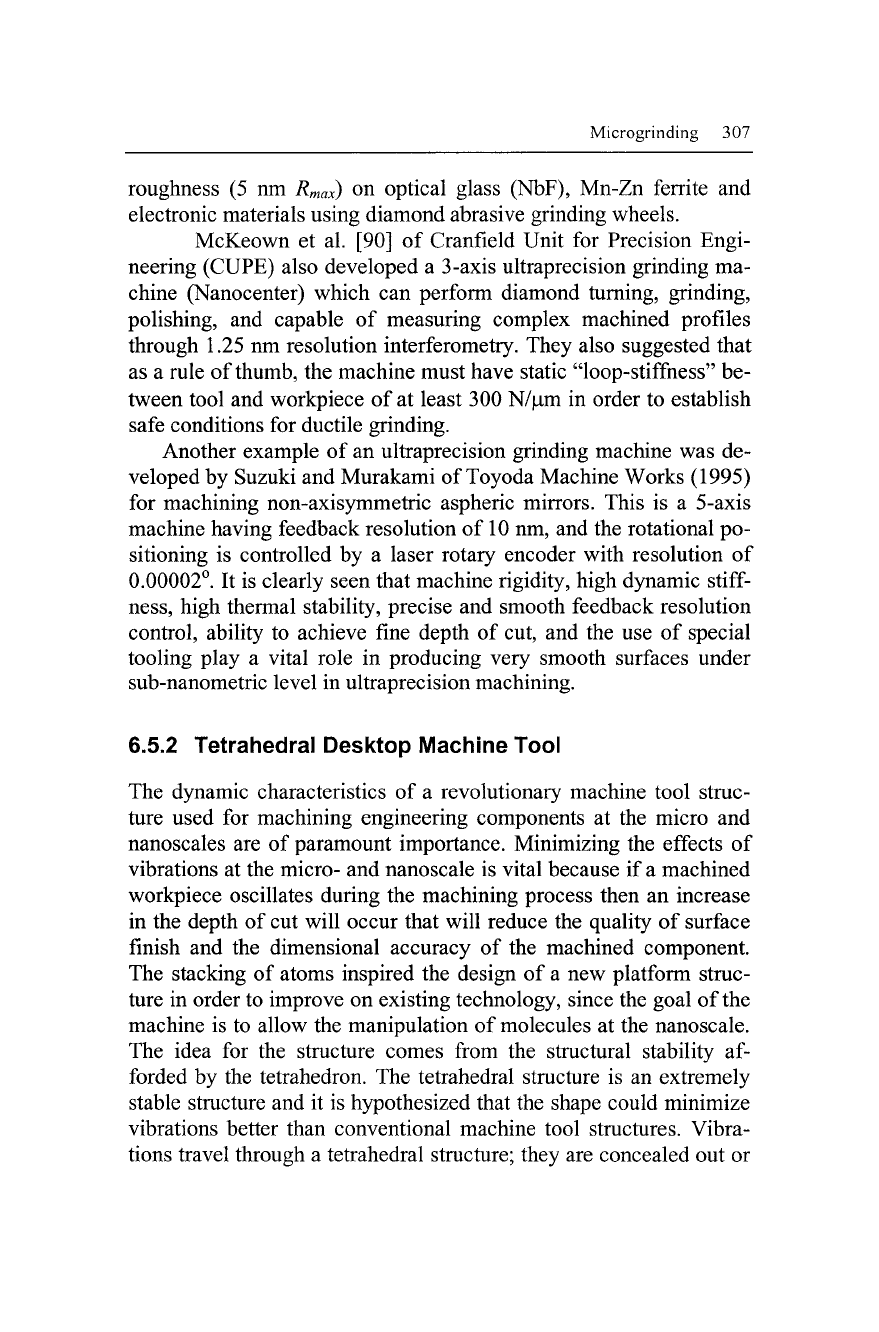
Microgrinding 307
roughness (5 nm
Rmax)
on optical glass (NbF), Mn-Zn ferrite and
electronic materials using diamond abrasive grinding wheels.
McKeown et al. [90] of Cranfield Unit for Precision Engi-
neering (CUPE) also developed a 3-axis ultraprecision grinding ma-
chine (Nanocenter) which can perform diamond turning, grinding,
polishing, and capable of measuring complex machined profiles
through 1.25 nm resolution interferometry. They also suggested that
as a rule of thumb, the machine must have static "loop-stiffness" be-
tween tool and workpiece of at least 300 N/|um in order to establish
safe conditions for ductile grinding.
Another example of an ultraprecision grinding machine was de-
veloped by Suzuki and Murakami of Toyoda Machine Works (1995)
for machining non-axisymmetric aspheric mirrors. This is a 5-axis
machine having feedback resolution of 10 nm, and the rotational po-
sitioning is controlled by a laser rotary encoder with resolution of
0.00002^. It is clearly seen that machine rigidity, high dynamic
stiff-
ness,
high thermal stability, precise and smooth feedback resolution
control, ability to achieve fine depth of cut, and the use of special
tooling play a vital role in producing very smooth surfaces under
sub-nanometric level in ultraprecision machining.
6.5.2 Tetrahedral Desktop Machine Tool
The dynamic characteristics of a revolutionary machine tool struc-
ture used for machining engineering components at the micro and
nanoscales are of paramount importance. Minimizing the effects of
vibrations at the micro- and nanoscale is vital because if a machined
workpiece oscillates during the machining process then an increase
in the depth of cut will occur that will reduce the quality of surface
finish and the dimensional accuracy of the machined component.
The stacking of atoms inspired the design of a new platform struc-
ture in order to improve on existing technology, since the goal of the
machine is to allow the manipulation of molecules at the nanoscale.
The idea for the structure comes from the structural stability af-
forded by the tetrahedron. The tetrahedral structure is an extremely
stable structure and it is hypothesized that the shape could minimize
vibrations better than conventional machine tool structures. Vibra-
tions travel through a tetrahedral structure; they are concealed out or