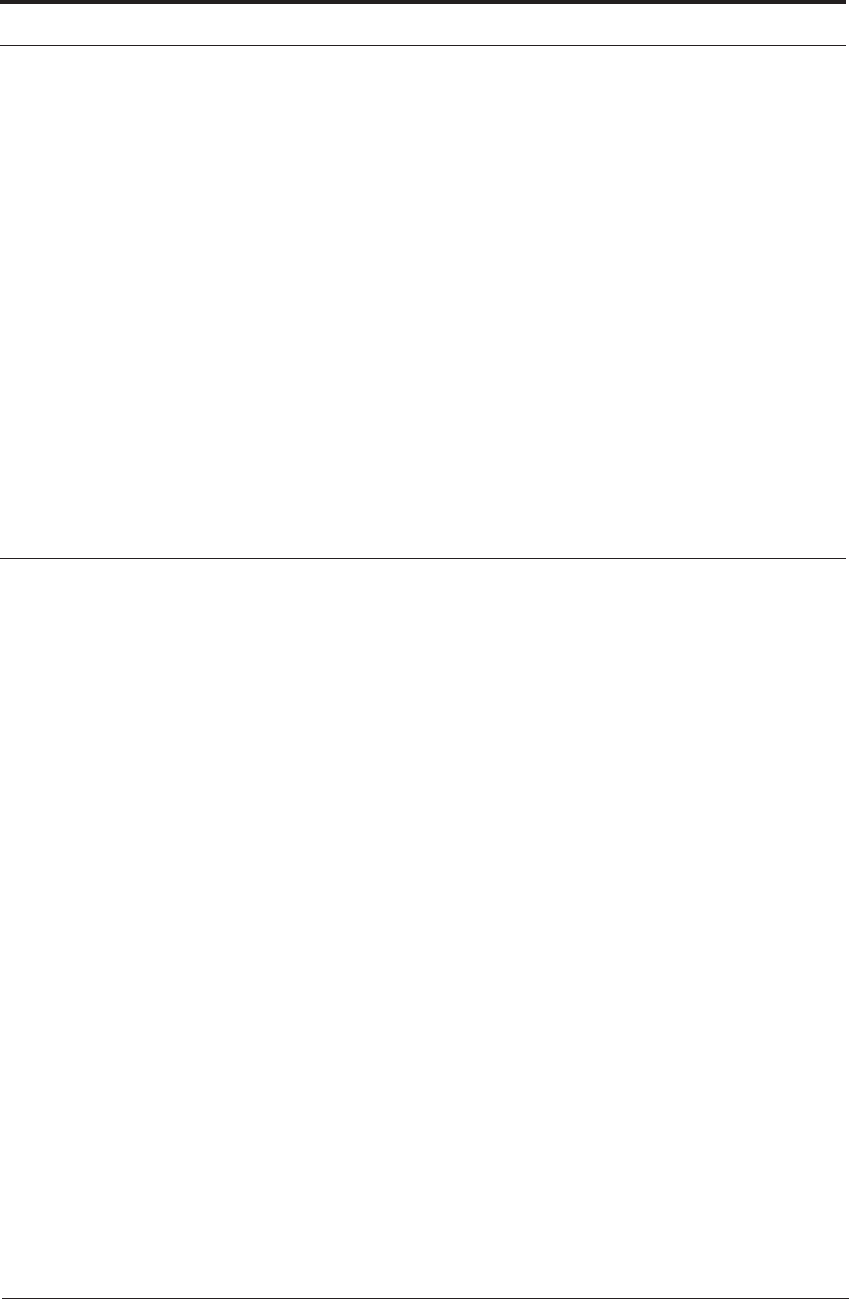
138 CUTTING TOOL MATERIALS I: HIGH SPEED STEELS
Carbon steel tools were used successfully for cutting copper at speeds as high as 110 m min
-1
(350 ft/min), but for cutting iron and steel, speeds were normally kept to about 5 or 7 m min
-1
(16 to 22 ft/min) to ensure a reasonable tool life. At the end of the last century, when the amount
of machining was escalating with industrial development, the very high costs resulting from the
extremely low productivity of machine tools operating at such very low speeds provided a major
incentive to develop improved tool materials. Steel had become the most important of materials
in engineering and the criterion of an improved tool material was its ability to cut steel at high
rate of metal removal. This remains largely true up to the present and the majority of the refer-
ences at the end of this chapter are concerned with improving the structure of high speed steels
or using them in improved ways to cut steels and other “difficult-to-machine” alloys.
6- 20
It should be emphasized that high-speed steels are still, today, the main tool materials used for
drills, end-milling-cutters, and broaches.
11,19,20
At the end of Chapter 8, it will be emphasized
that by no means have carbide or harder tools taken the place of high speed steel for such day-
to-day operations in a typical machine shop.
6.3 HIGH SPEED STEELS
The earliest commercially successful attempt to improve cutting tools by use of alloying ele-
ments was the ‘self-hardening’ tool steel of Robert Mushet, first made public in 1868.
3
This con-
tained about 6 to 10% tungsten and 1.2 to 2% manganese and, later, 0.5% chromium, with
carbon contents of 1.2 to 2.5%. The most outstanding property was that it could be hardened by
cooling in air from the hardening temperature and did not need to be quenched in water. Water
quenching often brought trouble through cracking, particularly with tools of large size and diffi-
cult shape. The ‘self-hardening’ quality was mainly the result of the high manganese content and
the chromium, both of which greatly retard the rate of transformation during cooling.
The tools were also found to give a modest improvement in the speed at which steel could be
cut compared with carbon steel tools - for example, from 7 m min
-1
to 10 m min
-1
(22 to 33 ft/
min). This can be attributed mainly to the tungsten which, after normal heat treatment, results in
a significant increase in the yield stress at elevated temperature. R. Mushet’s Special Steel, being
more expensive, was usually reserved by craftspeople for cutting hard materials or for difficult
operations.
The hardening procedures had been developed by centuries of experience of heat treatment of
carbon tool steels. Generations of blacksmiths, some very competent and highly skilled, had
established that tools were made brittle by hardening from temperatures above “cherry-red
heat”, and this constraint was, usually, applied to the heat treatment of self-hardening alloy steels
for more than 20 years after their introduction.
The story of how revolutionary changes in the properties and performance of alloy tool steels
were accomplished by modifying the conventional heat treatment is told by F. W. Taylor in his
presidential address in 1906 to the A.S.M.E., ‘On the Art of Cutting Metals’.
4
This outstanding
paper deserves to be read as an historical record of the steps by which an engineer, Taylor, and a
metallurgist, Maunsel White, developed high speed steels as part of what was probably the most
thorough and systematic program of tests in the history of machining technology.