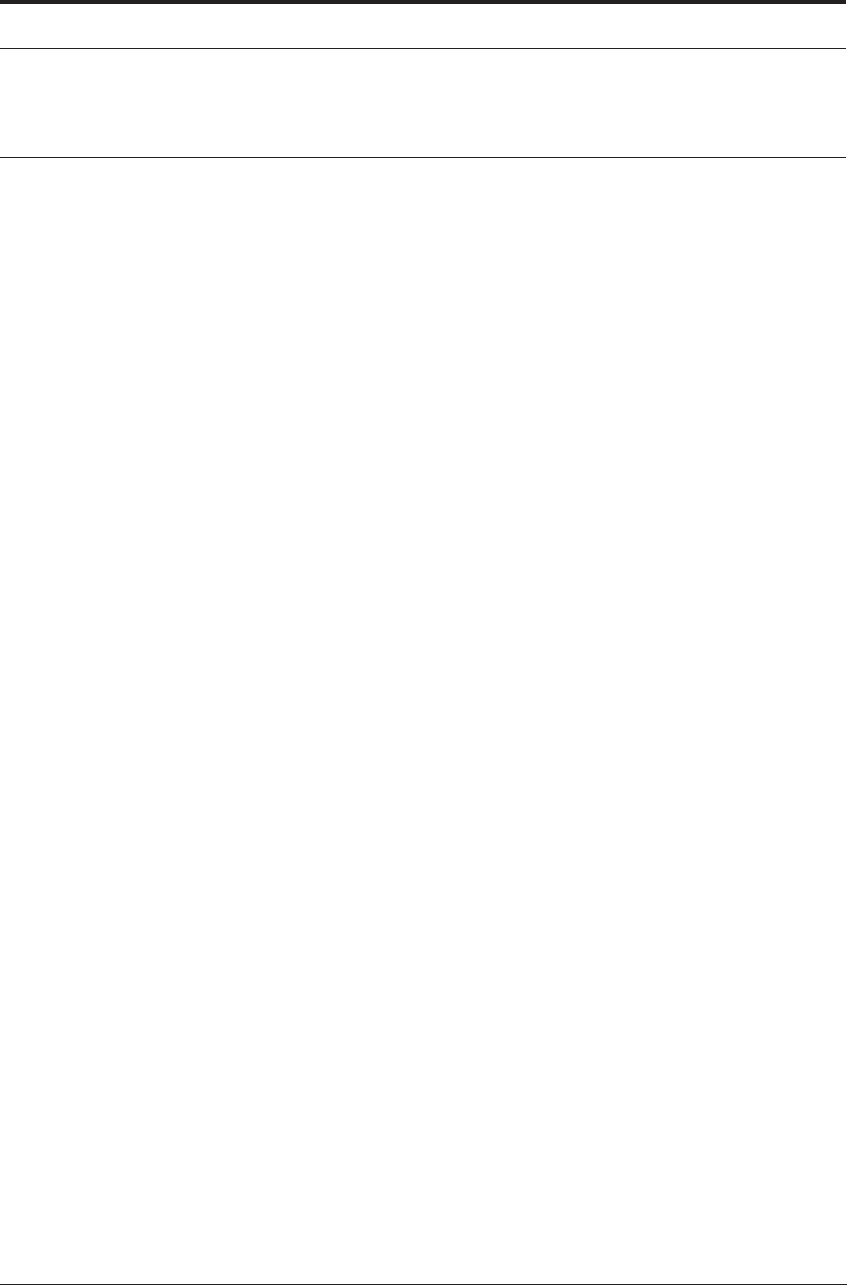
114 HEAT IN METAL CUTTING
5.6 METHODS OF TOOL TEMPERATURE MEASUREMENT
The difficulty of calculating temperatures and temperature gradients near the cutting edge,
even for very simple cutting conditions, gives emphasis to the importance of methods for mea-
suring temperature. This has been an important objective of research and some of the experimen-
tal methods explored are now discussed.
5.6.1 Tool/work thermocouple
The most extensively used method of tool temperature measurement has employed the tool
and the work material as the two elements of a thermocouple.
16
The thermoelectric e.m.f. gener-
ated between the tool and workpiece during cutting is measured using a sensitive millivoltmeter.
The hot junction is the contact area at the cutting edge, while an electrical connection to a cold
part of the tool forms one cold junction. The tool is electrically insulated from the machine tool
(usually a lathe). The electrical connection forming the cold junction with the rotating workpiece
is more difficult to make, and various methods have been adopted, a form of slip-ring often
being used.
Care must be taken to avoid secondary e.m.f. sources such as may arise with tipped tools, or
short circuits which may occur if the chip makes a second contact with the tool, for example on
a chip breaker. The e.m.f. can be measured and recorded during cutting, and, to convert these
readings to temperatures, the tool and work materials, used as a thermocouple, must be cali-
brated against a standard couple such as chromel-alumel. Each different type of tool and work
material used must be calibrated.
There are several sources of error in the use of this method. The tool and work materials are
not ideal elements of a thermocouple: the e.m.f. tends to be low, and the shape of the e.m.f.-tem-
perature curve is far from a straight line. It is doubtful whether the thermo-e.m.f. from a station-
ary couple, used in calibration, corresponds exactly to that of the same couple during cutting
when the work material is being severely strained. The tool/work thermo-couple method has
nevertheless been used successfully by many workers to investigate specific areas of metal cut-
ting - for example, to compare the machinability of different work materials, the effectiveness of
coolants and lubricants or the performance of different tool materials.
As an example, Kurimoto and Barrow cut a low-alloy engineering steel using a steel cutting
grade of cemented carbide tool over a range of speeds and feeds in air and using different cutting
lubricants.
17
Figure 5.9 shows the temperature determined, plotted against cutting speed for
three different values of feed, and a comparison of cutting in air and with water as a cutting fluid.
The results, the mean of 3 to 12 measurements, are consistent. They indicate an increase in tem-
perature with increments in speed and feed, and a small lowering of temperature when water was
used as a coolant. Temperatures over 1000°C are recorded for speeds of 120 m min
-1
(400ft/min)
and above - conditions commonly used in machine shops. This method is useful in demonstrat-
ing the influence of such variable parameters, but the significance to attach to the numerical val-
ues for temperature which it provides is uncertain.
It is demonstrated later that there are very steep temperature gradients across the contact area
when machining steel at high speed, with temperature differences of 300
°
C or greater at different
positions. It is uncertain whether the tool/work thermo-couple measures the lowest temperature