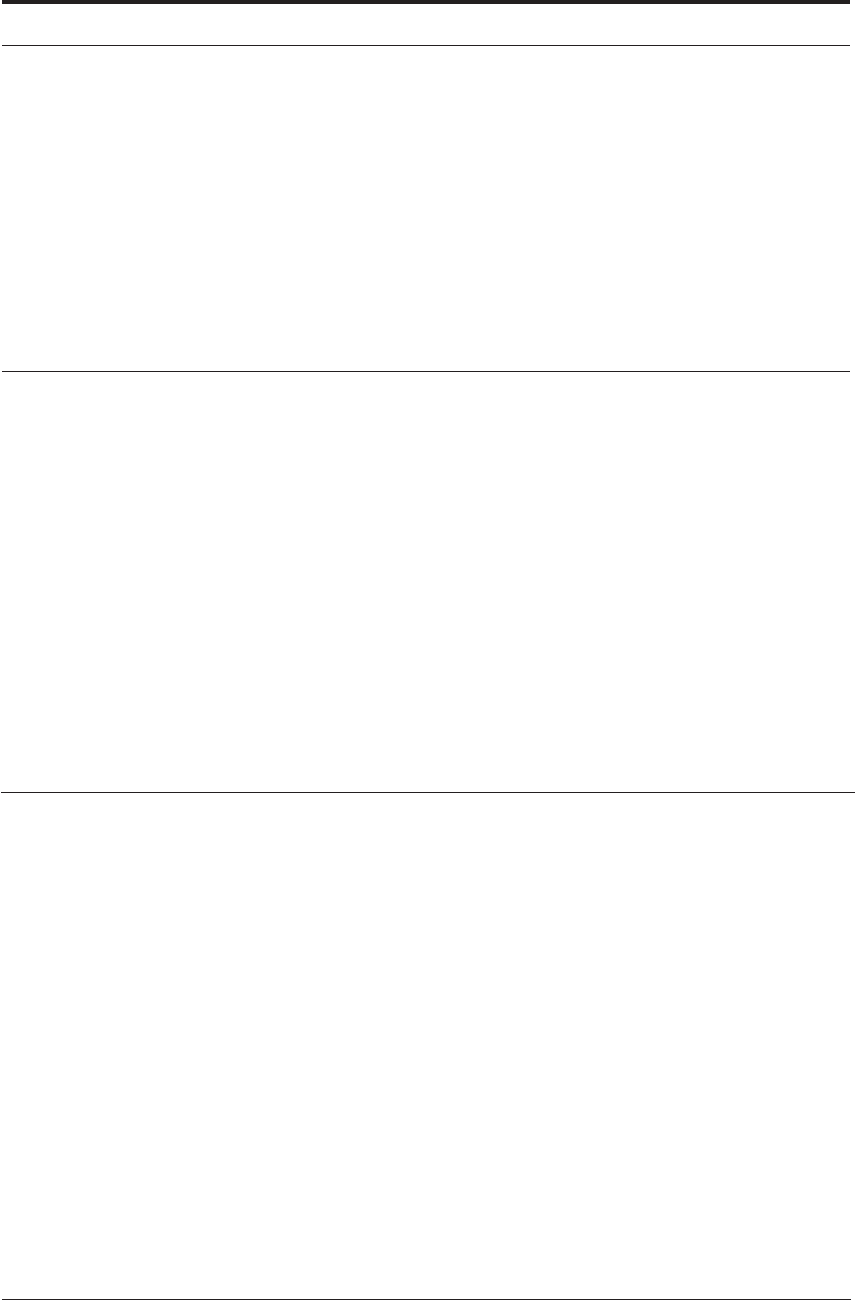
90 FORCES AND STRESSES IN METAL CUTTING
These rake-face normal and shear-stress distributions for the cutting conditions shown, quali-
tatively resemble those obtained by Chandrasekaran and Kapoor
17
who machined commercially
pure lead with a -10 degree rake angle epoxy resin tool. In the recent set of experiments with sap-
phire tools it was found that the boundary stress distributions varied with the speed and feed rate
as expected, although the variation was more pronounced with respect to feed rate.
4.7.6 Normal stress distribution: typical results
4.7.6.1 Influence of speed
TABLE 4.7 Comparisons of the Rake-face Stress Distributions from Photoelastic Analysis for
Different Machining Conditions
It can be seen in Table 4.7 that the maximum normal stress at the edge decreased by only 10%
for 650% increase in speed (from 10 to 75 m min
-1
) at 0.132 mm per revolution feed rate. At a
feed rate of 0.381 mm per revolution, although the speed was increased by 200% (from 25 to 75
m min
-1
) the decrease in peak stress was not noticeable. The variation in the stresses calculated
from experimental data closest to the cutting edge also showed the same trend. Such small
changes were not considered to be indicative of any variation of the stresses with speed.
4.7.7 Influence of feed rate
The variation of the normal stresses with feed rate was more noticeable. The rake-face normal
stresses increased by a factor of 1.5 when the feed rate was increased near three times from 0.132
to 0.381 mm per revolution. It is thus clear that the interfacial stresses increase with the uncut
chip thickness. However experimentation over a broader range of feed rates will be necessary
before any functional relationship between stresses and feed rate can be established.
The experimental data was also approximately validated by comparing the total normal force
measured by the 3 axis dynamometer with that obtained by integrating the normal stress distribu-
tion from photoelastic stress analysis (Figures 4.23 to 4.25) over the entire contact length. Table
4.8 shows the comparison between the rake face normal forces calculated from photoelastic
work
material
speed
m min
-1
thickness
(uncut chip)
mm
width
(uncut
chip)
mm
Cutting Forces
for F
f
and F
c
newtons
average
normal
stress
MPa
peak
normal
stress
MPa
360 brass 60 0.132 5.00 947 1373 --- 600
1020 steel 10 0.132 4.50 1225 1778 --- 565
12L14 steel 10 0.132 5.00 558 1307 286 580
12L14 steel 25 0.132 4.84 294 904 326 490
12L14 steel 75 0.132 4.93 201 821 339 530
12L14 steel 25 0.381 5.00 847 2633 498 800
12L14 steel 75 0.381 4.99 450 2140 495 840