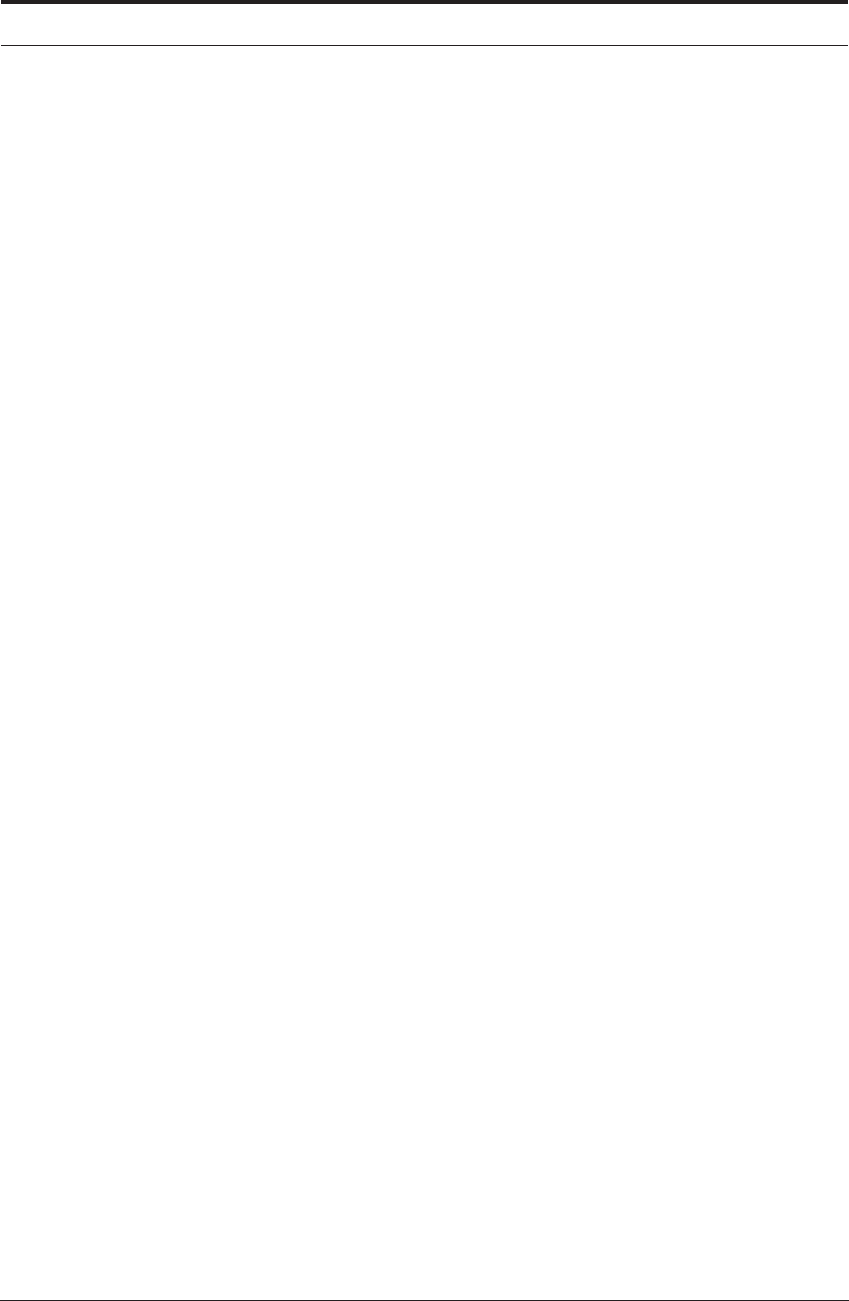
THE SHEAR PLANE AND MINIMUM ENERGY THEORY 65
(4.16)
where is the shear-plane area .
The coefficient of friction is defined in usual engineering practice as the ratio of the force in
the direction of sliding to the force normal to the sliding interface. Thus, from the geometry
shown, Figure 4.3, it follows that on the rake face of the tool, the coefficient of friction,
(4.17)
(4.18)
where F is the friction force on the rake face, N is the normal force on the rake face, and is the
friction angle.
The usual concept of friction implies that F and N are forces which are uniformly distributed
over the sliding interface. However, this is not the case in metal cutting and thus this approach to
coefficient of friction is too simple to adequately describe a seizure situation.
Although there have been many attempts to update the model, change its boundary conditions
and consider new material properties, it still remains a useful, direct way of thinking about the
energy used in cutting and how deformation will take place.
4.4.2 Oxley’s shear ‘zone’ analysis
More recently other research workers, notably Oxley and colleagues,
6
have refined the analy-
sis of cutting using more realistic models. Chip formation is considered to take place in a fan-
shaped zone at low speed, and a parallel-sided zone at higher speeds, rather than on a single
plane. The work-hardening characteristics of the material are taken into account. The frictional
conditions are described as shear within a layer of the chip adjacent to the rake face of the tool.
Within this layer “near-seizure” conditions are said to exist, with velocity in the work material
approaching zero at the interface. To make quantitative predictions from this model, attempts are
made to use realistic data for the stress/strain behavior of the work material allowing for strain
hardening and the influence of high strain rates and temperature. This model is a considerable
advance. For example, the conditions in which a built-up edge will occur during the cutting of
steel can be predicted.
In Figure 4.4 , the directions of maximum shear stress and maximum shear strain-rate are: i)
the line OD, near the center of the shear zone, and ii) the tool/chip interface.
σ normal stress
F
c
φ F
t
φcos+sin[]φsin
wt
1
----------------------------------------------------------==
A
s
wt
1
φsin⁄
μ
F
N
----
F
c
α F
c
αcos+sin
F
c
α F
t
αsin–cos
--------------------------------------------==
F
c
F
t
αtan+
F
c
F
t
αtan–
------------------------------= λtan=
λ