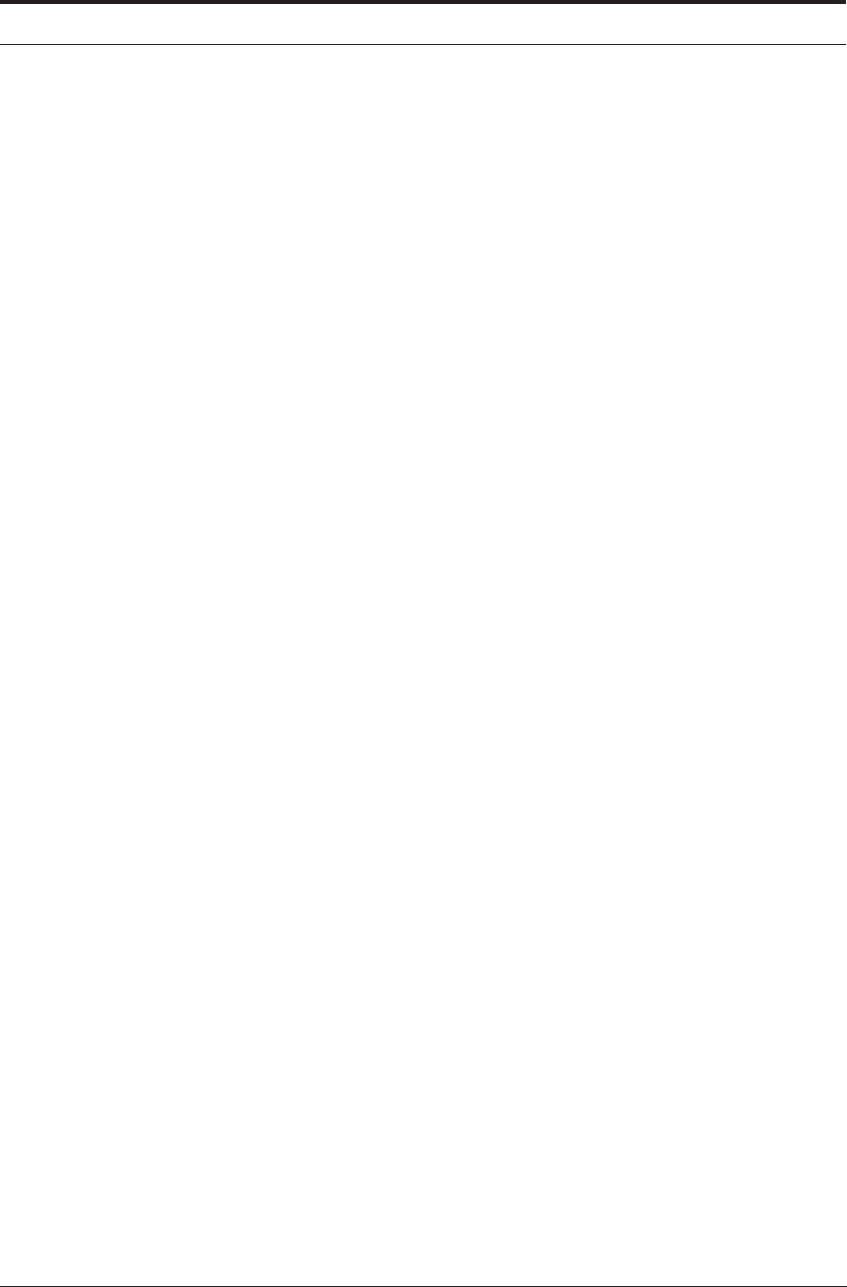
48 THE ESSENTIAL FEATURES OF METAL CUTTING
finishing cuts. It is important to consider that the finishing cuts might “inherit” damage (Figure
3.25) from the previous roughing cuts.
17-18
To arrive at an acceptable accuracy/tolerance with minimal damage, it may, in certain circum-
stances, be advisable to use a modest roughing cut followed by two lighter finishing cuts, rather
than one more aggressive roughing cut which causes such sub-surface damage to the extent that
only one finishing cut cannot correct the surface. A small sacrifice in overall machining time
may, in such a case, be a better strategy for minimizing sub-surface damage. Further research is
desirable to investigate such strategies for different commercial alloys.
The issues related to sub-surface damage become even more critical in the “precision” and
“ultra-precision” ranges in Figure 1.1. In such operations, the value of the undeformed chip
thickness (t
1
) during finishing cuts is very small. It is useful to refer to Figures 2.1 and 3.1 and
relate the value of t
1
, the feed rate, to any possible tool wear, blemishes, nicks, or general round-
ing of the tool’s edge during use (at position O in Figure 3.1). During roughing cuts, with a large
value of t
1
, such blemishes or rounding will not be a major influence on the general smoothness
of the chip flow process. By contrast, thinking about relative proportions, when t
1
is very small,
as in precision finishing, any blemishes or tool-edge rounding by wear will have a more dra-
matic interference on the general smoothness of chip flow and consequently on the quality of the
surface finish of the part being machined.
Thus, when considering the condition of the machined surface, especially for precision
machining, the sharpness and integrity of the cutting edge is probably the most important issue
to focus on.
During a particular cut as the edge wears and becomes slightly blunt or rounded, the strain
imposed on the machined surface increases. Intuitively, it can be imagined that a rounded tool
edge is, at high magnification, like a blunt wedge being dragged across the surface. The more
blunt and rounded the edge becomes, the more the action resembles a blunt hardness-tester being
dragged on the surface causing the familiar strain fields seen in standard plasticity textbooks.
19
As the tool wears even more, the effect can cause shear lamellae to spall-off, visibly creating
rough “ears” on the machined surface and on the underside of the chip.
Figures 3.26 to 3.30 have been drawn to summarize the development of such effects over time.
Experience has shown that by the time the tool exhibits 0.75mm (0.03 inches) of flank wear, the
tool is essentially worn-out because its blunted state causes considerable damage on the
machined surface.
Also, at the end of the tool’s life the “indenting rather than cutting” effect of its worn edges
and clearance face can push-up a “collar formation”. This occurs at the outer shoulder of the bar
in Figure 2.1 and is shown schematically for face-milling in Figure 3.29.
Clearly this effect is unacceptable for high accuracy machining and the tool should be changed
well before the usual 0.75mm (0.03 inches) flank wear limit. However, even at lesser amounts of
flank wear, some damage occurs, building up on a gradual basis. Figures 3.26 to 3.28 have been
drawn to show the gradual transition that occurs. A highly skilled machinist can track these
events, and also correlate them with aural and visual cues as summarized in Figure 3.30.
In conclusion, the characteristics of machined surfaces, especially those of high-quality form-
ing dies and components that demand high-precision, are greatly dependent on the flow patterns,
stresses and temperatures at this all-important tool edge, O, and these are the subjects of the next
chapters.