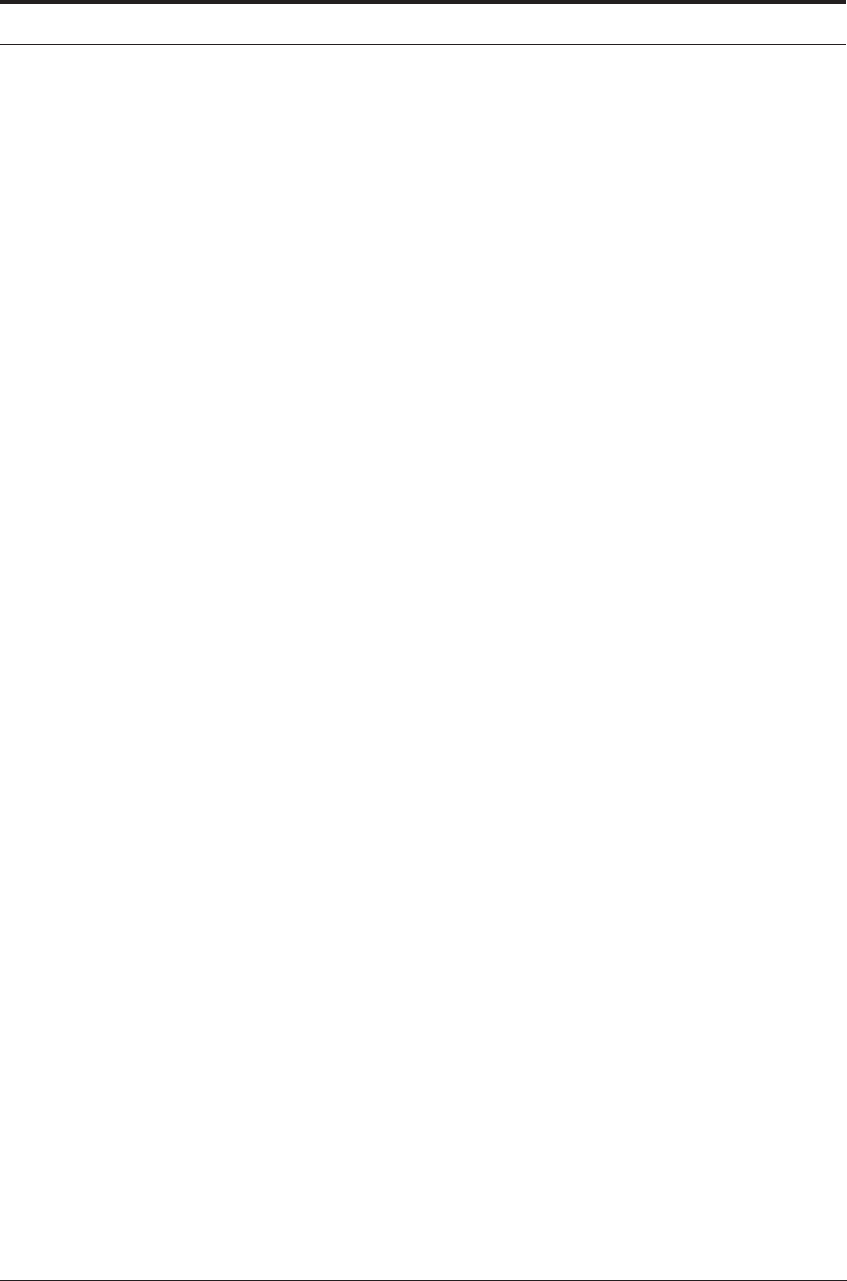
THE CHIP/TOOL INTERFACE 31
coefficient of friction, F/N, is therefore a useful concept - i.e. under conditions where the normal
stress on the apparent contact area is very small compared with the yield stress of the materials.
When the normal force is increased to such an extent that the real area of contact is a large pro-
portion of the apparent contact area, it is no longer possible for the real contact area to increase
proportionately to the load. In the extreme case, where the two surfaces are completely in con-
tact, the real area of contact becomes independent of the normal force, and the frictional force
becomes that required to shear the material across the whole interface. When two materials of
different strengths are in contact, as in metal cutting, the force required to move one body over
the other becomes that required to shear the weaker of the two materials across the whole area.
This force is almost independent of the normal force, but is directly proportional to apparent area
of contact - a relationship directly opposed to that of classical friction concepts!
It is, therefore, important to know what conditions exist at the interface between tool and work
material during cutting. This is a very difficult region to investigate. Few significant observa-
tions can be made while cutting is in progress, thus the conditions existing must be inferred from
studies of the interface after cutting has stopped, and from measurements of stress and tempera-
ture. The conclusions presented here are deduced from studies, mainly by optical and electron
microscopy, of the interface between work-material and tool after use in a wide variety of cutting
conditions. Evidence comes from worn tools, from quick-stop sections and from chips.
The most important conclusion from the observations is that contact between tool and work
surfaces is so nearly complete over a large part of the total area of the interface that sliding at
the interface is impossible under most cutting conditions.
7
The evidence for this statement is
now reviewed.
When cutting is stopped by disengaging the feed and withdrawing the tool, layers of the work
material are commonly, but not always, observed on the worn tool surfaces, and micro-sections
through these surfaces can preserve details of the interface. Special metallographic techniques
are essential to prevent rounding of the edge where the tool is in contact with a much softer, thin
layer of work-material.
Figure 3.7 is a photomicrograph (x 1,500) of a section through the cutting edge of a cemented
carbide tool used to cut steel. The white area is the residual steel layer, which is attached to the
cutting edge (slightly rounded), the tool rake face (horizontal) and down the worn flank. The two
surfaces remained firmly attached during the grinding and polishing of the metallographic sec-
tion. Any gap larger than 0.1 μm (4 micro-inches) would be visible at the magnification in this
photomicrograph, but no such gap can be seen. It is unlikely that a gap exists since none of the
lubricant used in polishing oozed out afterwards.
Figure 3.8 is an electron micrograph of a replica of a section through a high speed steel tool at
the rake surface, where the work material (top) was adherent to the tool. The tool had been used
for cutting a very low carbon steel at high cutting speed (200 m min
-1
; 1,600 ft/min). The steel
adhering to the tool had recrystallized and contact between the two surfaces is continuous, in
spite of the uneven surface of the tool, which would make sliding impossible. Many investiga-
tions have shown the two surfaces to be interlocked, the adhering metal penetrating both major
and minor irregularities in the tool surface.