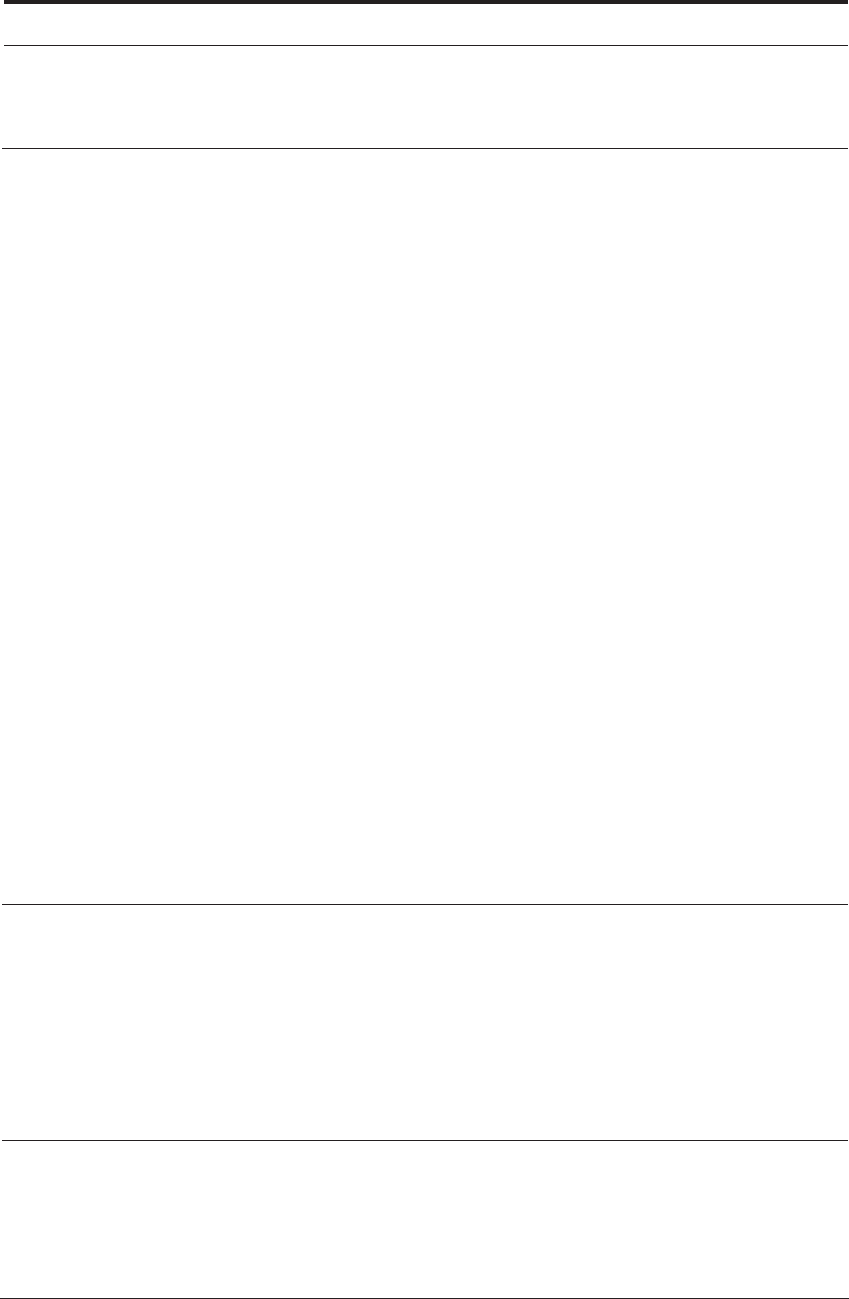
CONCLUSION 19
2.10 CONCLUSION
The operations described are some of the more important ones employed in shaping engineer-
ing components, but there are many others. Some of these, like sawing, filing and tapping of
threads, are familiar to all of us, but others such as skiving, reaming or the hobbing of gears are
the province of the specialist. Each of these operations has its special characteristics and prob-
lems, as well as the features which it has in common with the others.
There is one further variable which should be mentioned at this stage and that is the environ-
ment of the tool edge. Cutting is often carried out in air, but in many operations the use of a fluid
to cool the tool or the workpiece, and/or act as a lubricant, is essential to efficiency. The fluid is
usually a liquid, based on water or a mineral oil, but may be a gas such as CO
2
. The action of
coolants/lubricants will be considered in Chapter 10, but the influence of the cutting lubricant, if
any, should never be neglected.
One objective of this very brief discussion of cutting operations is to make a major point
which the reader should bear in mind in the subsequent chapters: in spite of the complexity and
diversity of machining, analyses are made in the next three chapters of some of the more impor-
tant features which all metal cutting operations have in common. The more theoretical work
begins with an analysis of the basic geometry and features of metal cutting in Chapter 3. Stress
and heat generation are then considered in Chapters 4 and 5. The work on which these analyses
are based has, of necessity, been derived from a study of a limited number of cutting operations -
often the simplest - such as uninterrupted turning, and from investigations in the machining of a
limited range of work materials. At the same time, the results of these analyses should not be
used uncritically, in the complex conditions of machine shops. In considering any problem of
metal cutting, the first questions to ask should be - what is the machining operation, and what are
the specific features which are critical for this operation?
3
Especially in Chapter 9 on “Machin-
ability”, it will be seen that the general pictures of stress and temperature distributions vary quite
considerably from one work material alloy to the next.
2.11 REFERENCES
1. United States Cutting Tool Institute, Metal Cutting Tool Handbook, 7th ed.
2. Stabler, G.V., J.I. Prod. E.,
34, 264 (1955)
3. A.S.M. Metals Handbook, 8th ed., Vol.3. ‘Machining’ (1967)
4. Kline, W.A., and DeVor, R.E. Int. J. Mach. Tool Des. Res., 23, (2/3), 123 (1983)
5. Stori, J.A. Ph.D. Thesis, University of California, Berkeley, (1998)
2.12 BIBLIOGRAPHY (Also see Chapter 15)
These introductory texts are helpful with diagrams of tool geometry and processes:
1. DeGarmo, E. P., Black, J.T., and Kohser, R. A., Materials and Processes in Manufacturing,
8th Edition, Prentice Hall, New York (1997)