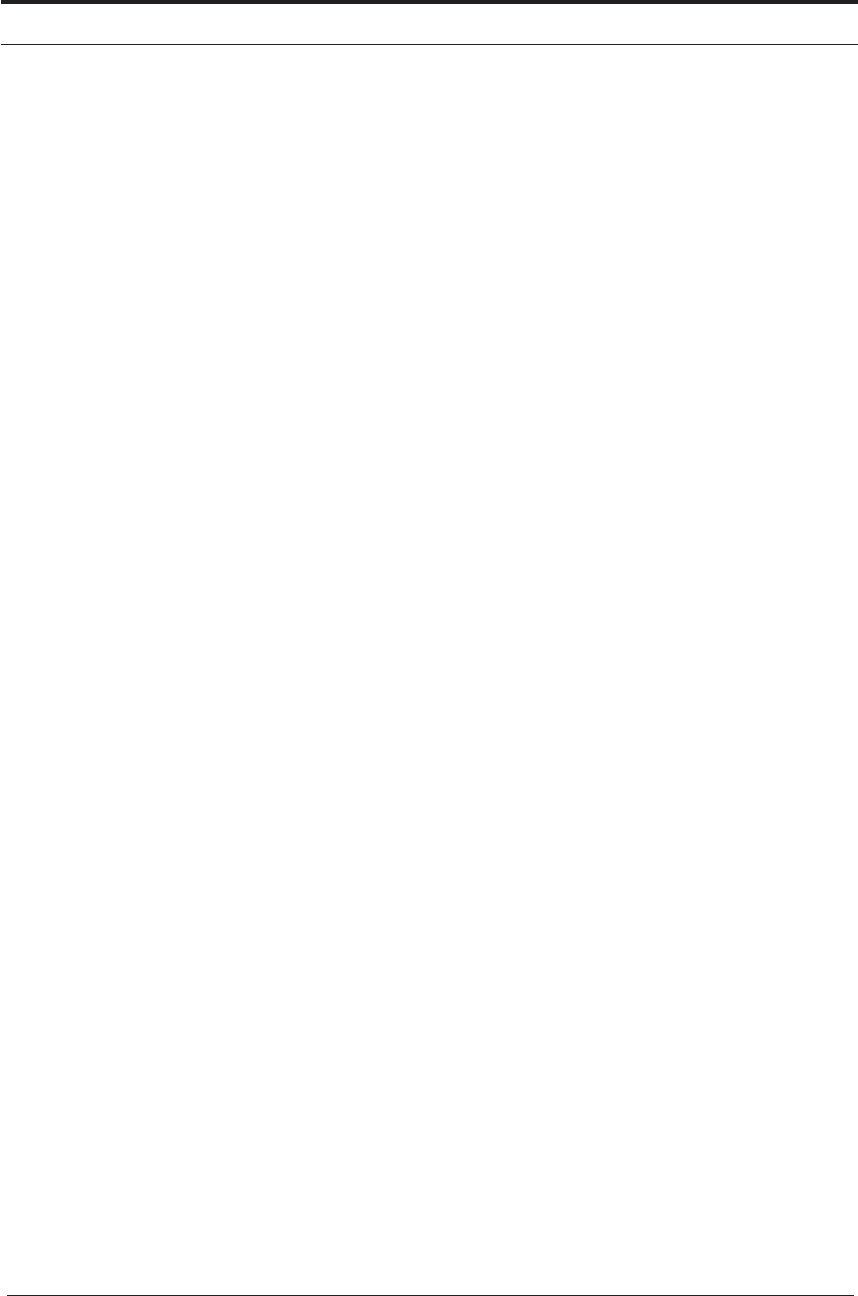
A SHORT HISTORY OF MACHINING 3
By 1860 the basic problem of how to produce the necessary shapes in the existing materials
had been solved. There had been little change in the materials which had to be machined - cast
iron, wrought iron and a few copper based alloys. High carbon tool steel, hardened and tempered
by the blacksmith, still had to answer all the tooling requirements. The quality and the consis-
tency of tool steels had been greatly improved by a century of experience with the crucible steel
process. Yet even the best carbon steel tools, pushed to their functional limits, were increasingly
insufficient for manufacturers’ needs, constraining production speed and hampering efficiency.
From the mid-1880s on, innovative energies in manufacturing shifted from developing basic
machine tools and producing highly-accurate parts to reducing machining costs and cutting new
types of metals and alloys. With the Bessemer and Open Hearth steel making processes, steel rap-
idly replaced wrought iron as the workhorse of construction materials. Industry required ever
greater tonnages of steel (steel production soon vastly exceeded the earlier output of wrought
iron), and required it machined to particular specifications.
Alloy steels proved much more difficult than wrought iron to machine, and cutting speeds had
to be lowered even further to maintain reasonable tool life. Towards the end of the 19th century,
both the labor and capital costs of machining were becoming very great. The incentive to reduce
costs by accelerating and automating the cutting process became more intense, and, up to the
present time, still acts as the major driving force behind technological developments in the metal
cutting field.
The discovery and manipulation of new cutting tool materials has been perhaps the most
important theme in the last century of metal cutting. Productivity could not have significantly
increased without the higher cutting speeds achievable using high-speed steel and cemented car-
bide tools, both important advances over traditional carbon steel technology. The next major step
occurred with the development of ceramic and ultra-hard tool materials. Recently, a group of new
techniques, including electrical discharge and water-jet machining, have joined ceramic and
ultra-hard materials at the forefront of metal cutting technology.
Machine tool manufacturers have created machines capable of maximizing the utility of each
generation of cutting tool materials. Designers and machinists have optimized the shapes of tools
to lengthen tool life at high cutting speeds, while lubricant manufacturers have developed new
coolants and lubricants to improve surface finish and permit increased rates of metal removal.
Tool control has also advanced considerably since the days of manually operated machines.
Automatic machines, computer numerically controlled (CNC) machines and transfer machines
produce better tool efficiency, greatly increasing output per employee.
Increasingly, the process of metal cutting is integrated with computer software and hardware
that control machine tools. The age of “mechatronics” accompanies a trend toward integrated
manufacturing systems composed of cells and modules of machines rather than individual, stand-
alone units. Machining today requires a wider range of skills than it did a century ago: computer
programming and knowledge of electronic equipment, among others. Nevertheless, knowledge
of the physical realities of the tool-work interface is as important as ever.
One last note should be added to our understanding of the evolution of machine tool technol-
ogy concerning the double role of basic metal producers. Many new alloys have been developed
to meet the increasingly severe conditions of stress, temperature and corrosion imposed by the
needs of our industrial civilization. Some of these materials, like aluminum and magnesium, are
easy to machine, but others, such as high-alloy steels and nickel-based alloys, become more diffi-
cult to cut as their useful properties (i.e. strength, durability, etc.) improve. The machine tool and