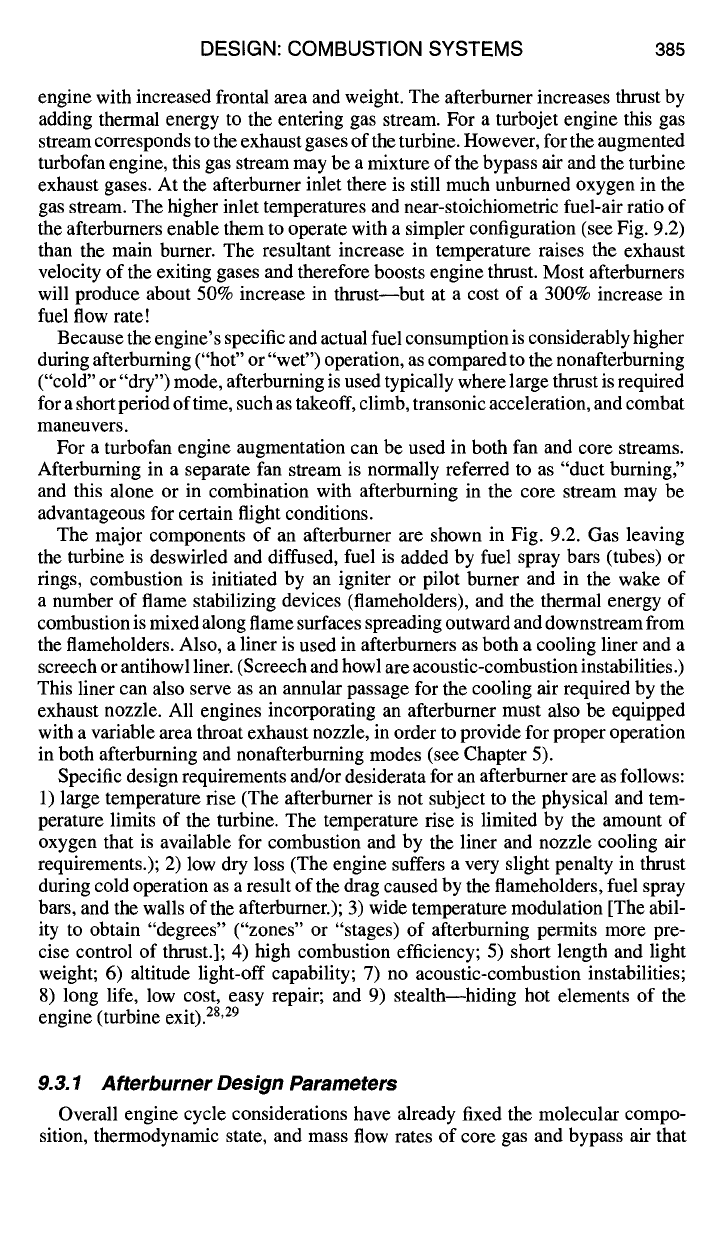
DESIGN: COMBUSTION SYSTEMS 385
engine with increased frontal area and weight. The afterburner increases thrust by
adding thermal energy to the entering gas stream. For a turbojet engine this gas
stream corresponds to the exhaust gases of the turbine. However, for the augmented
turbofan engine, this gas stream may be a mixture of the bypass air and the turbine
exhaust gases. At the afterburner inlet there is still much unburned oxygen in the
gas stream. The higher inlet temperatures and near-stoichiometric fuel-air ratio of
the afterburners enable them to operate with a simpler configuration (see Fig. 9.2)
than the main burner. The resultant increase in temperature raises the exhaust
velocity of the exiting gases and therefore boosts engine thrust. Most afterburners
will produce about 50% increase in thrust--but at a cost of a 300% increase in
fuel flow rate!
Because the engine's specific and actual fuel consumption is considerably higher
during afterburning ("hot" or"wet") operation, as compared to the nonafterburning
("cold" or"dry") mode, afterburning is used typically where large thrust is required
for a short period of time, such as takeoff, climb, transonic acceleration, and combat
maneuvers.
For a turbofan engine augmentation can be used in both fan and core streams.
Afterburning in a separate fan stream is normally referred to as "duct burning,"
and this alone or in combination with afterburning in the core stream may be
advantageous for certain flight conditions.
The major components of an afterburner are shown in Fig. 9.2. Gas leaving
the turbine is deswirled and diffused, fuel is added by fuel spray bars (tubes) or
rings, combustion is initiated by an igniter or pilot burner and in the wake of
a number of flame stabilizing devices (flameholders), and the thermal energy of
combustion is mixed along flame surfaces spreading outward and downstream from
the flameholders. Also, a liner is used in afterburners as both a cooling liner and a
screech or antihowl liner. (Screech and howl are acoustic-combustion instabilities.)
This liner can also serve as an annular passage for the cooling air required by the
exhaust nozzle. All engines incorporating an afterburner must also be equipped
with a variable area throat exhaust nozzle, in order to provide for proper operation
in both afterburning and nonafterburning modes (see Chapter 5).
Specific design requirements and/or desiderata for an afterburner are as follows:
1) large temperature rise (The afterburner is not subject to the physical and tem-
perature limits of the turbine. The temperature rise is limited by the amount of
oxygen that is available for combustion and by the liner and nozzle cooling air
requirements.); 2) low dry loss (The engine suffers a very slight penalty in thrust
during cold operation as a result of the drag caused by the flameholders, fuel spray
bars, and the walls of the afterburner.); 3) wide temperature modulation [The abil-
ity to obtain "degrees" ("zones" or "stages) of afterburning permits more pre-
cise control of thrust.]; 4) high combustion efficiency; 5) short length and light
weight; 6) altitude light-off capability; 7) no acoustic-combustion instabilities;
8) long life, low cost, easy repair; and 9) stealth--hiding hot elements of the
engine (turbine exit). 28,29
9.3.1 Afterburner Design Parameters
Overall engine cycle considerations have already fixed the molecular compo-
sition, thermodynamic state, and mass flow rates of core gas and bypass air that