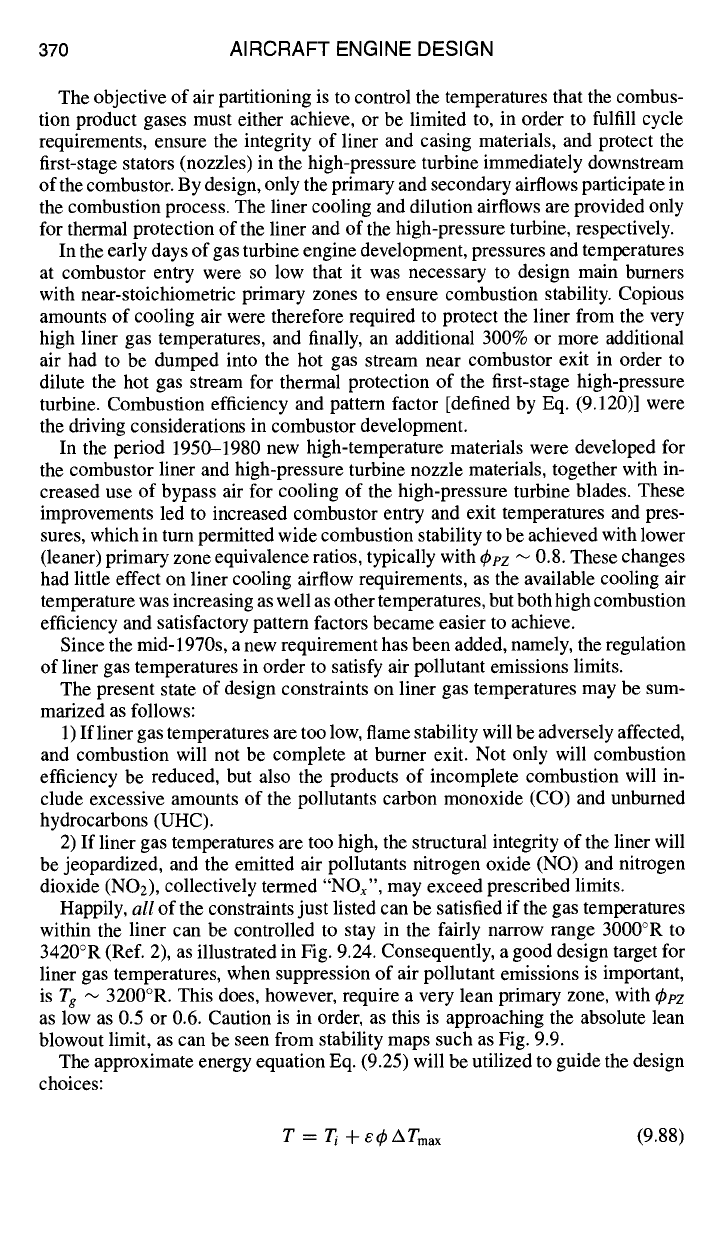
370 AIRCRAFT ENGINE DESIGN
The objective of air partitioning is to control the temperatures that the combus-
tion product gases must either achieve, or be limited to, in order to fulfill cycle
requirements, ensure the integrity of liner and casing materials, and protect the
first-stage stators (nozzles) in the high-pressure turbine immediately downstream
of the combustor. By design, only the primary and secondary airflows participate in
the combustion process. The liner cooling and dilution airflows are provided only
for thermal protection of the liner and of the high-pressure turbine, respectively.
In the early days of gas turbine engine development, pressures and temperatures
at combustor entry were so low that it was necessary to design main burners
with near-stoichiometric primary zones to ensure combustion stability. Copious
amounts of cooling air were therefore required to protect the liner from the very
high liner gas temperatures, and finally, an additional 300% or more additional
air had to be dumped into the hot gas stream near combustor exit in order to
dilute the hot gas stream for thermal protection of the first-stage high-pressure
turbine. Combustion efficiency and pattern factor [defined by Eq. (9.120)] were
the driving considerations in combustor development.
In the period 1950-1980 new high-temperature materials were developed for
the combustor liner and high-pressure turbine nozzle materials, together with in-
creased use of bypass air for cooling of the high-pressure turbine blades. These
improvements led to increased combustor entry and exit temperatures and pres-
sures, which in turn permitted wide combustion stability to be achieved with lower
(leaner) primary zone equivalence ratios, typically with q~pz "~ 0.8. These changes
had little effect on liner cooling airflow requirements, as the available cooling air
temperature was increasing as well as other temperatures, but both high combustion
efficiency and satisfactory pattem factors became easier to achieve.
Since the mid-1970s, a new requirement has been added, namely, the regulation
of liner gas temperatures in order to satisfy air pollutant emissions limits.
The present state of design constraints on liner gas temperatures may be sum-
marized as follows:
1) If liner gas temperatures are too low, flame stability will be adversely affected,
and combustion will not be complete at burner exit. Not only will combustion
efficiency be reduced, but also the products of incomplete combustion will in-
clude excessive amounts of the pollutants carbon monoxide (CO) and unburned
hydrocarbons (UHC).
2) If liner gas temperatures are too high, the structural integrity of the liner will
be jeopardized, and the emitted air pollutants nitrogen oxide (NO) and nitrogen
dioxide (NO2), collectively termed "NOx", may exceed prescribed limits.
Happily,
all
of the constraints just listed can be satisfied if the gas temperatures
within the liner can be controlled to stay in the fairly narrow range 3000°R to
3420°R (Ref. 2), as illustrated in Fig. 9.24. Consequently, a good design target for
liner gas temperatures, when suppression of air pollutant emissions is important,
is
Tg ,~
3200°R. This does, however, require a very lean primary zone, with ~bpz
as low as 0.5 or 0.6. Caution is in order, as this is approaching the absolute lean
blowout limit, as can be seen from stability maps such as Fig. 9.9.
The approximate energy equation Eq. (9.25) will be utilized to guide the design
choices:
T = T~ + egoATmax
(9.88)