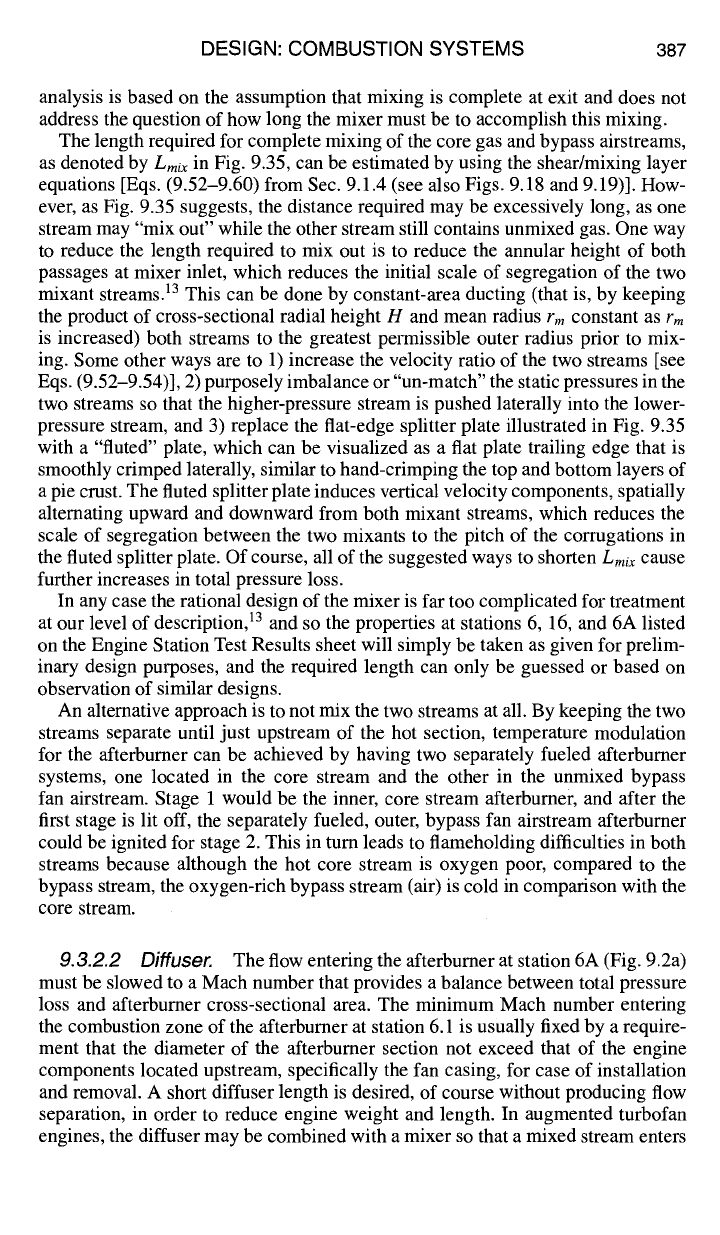
DESIGN: COMBUSTION SYSTEMS 387
analysis is based on the assumption that mixing is complete at exit and does not
address the question of how long the mixer must be to accomplish this mixing.
The length required for complete mixing of the core gas and bypass airstreams,
as denoted by
Lmix
in Fig. 9.35, can be estimated by using the shear/mixing layer
equations [Eqs. (9.52-9.60) from Sec. 9.1.4 (see also Figs. 9.18 and 9.19)]. How-
ever, as Fig. 9.35 suggests, the distance required may be excessively long, as one
stream may "mix out" while the other stream still contains unmixed gas. One way
to reduce the length required to mix out is to reduce the annular height of both
passages at mixer inlet, which reduces the initial scale of segregation of the two
mixant streams. 13 This can be done by constant-area ducting (that is, by keeping
the product of cross-sectional radial height H and mean radius
rm
constant as
r m
is increased) both streams to the greatest permissible outer radius prior to mix-
ing. Some other ways are to l) increase the velocity ratio of the two streams [see
Eqs. (9.52-9.54)], 2) purposely imbalance or "un-match" the static pressures in the
two streams so that the higher-pressure stream is pushed laterally into the lower-
pressure stream, and 3) replace the flat-edge splitter plate illustrated in Fig. 9.35
with a "fluted" plate, which can be visualized as a flat plate trailing edge that is
smoothly crimped laterally, similar to hand-crimping the top and bottom layers of
a pie crust. The fluted splitter plate induces vertical velocity components, spatially
alternating upward and downward from both mixant streams, which reduces the
scale of segregation between the two mixants to the pitch of the corrugations in
the fluted splitter plate. Of course, all of the suggested ways to shorten
Lmix
cause
further increases in total pressure loss.
In any case the rational design of the mixer is far too complicated for treatment
at our level of description, 13 and so the properties at stations 6, 16, and 6A listed
on the Engine Station Test Results sheet will simply be taken as given for prelim-
inary design purposes, and the required length can only be guessed or based on
observation of similar designs.
An alternative approach is to not mix the two streams at all. By keeping the two
streams separate until just upstream of the hot section, temperature modulation
for the afterburner can be achieved by having two separately fueled afterburner
systems, one located in the core stream and the other in the unmixed bypass
fan airstream. Stage 1 would be the inner, core stream afterburner, and after the
first stage is lit off, the separately fueled, outer, bypass fan airstream afterburner
could be ignited for stage 2. This in turn leads to flameholding difficulties in both
streams because although the hot core stream is oxygen poor, compared to the
bypass stream, the oxygen-rich bypass stream (air) is cold in comparison with the
core stream.
9.3.2.2 Diffuser. The flow entering the afterburner at station 6A (Fig. 9.2a)
must be slowed to a Mach number that provides a balance between total pressure
loss and afterburner cross-sectional area. The minimum Mach number entering
the combustion zone of the afterburner at station 6.1 is usually fixed by a require-
ment that the diameter of the afterburner section not exceed that of the engine
components located upstream, specifically the fan casing, for case of installation
and removal. A short diffuser length is desired, of course without producing flow
separation, in order to reduce engine weight and length. In augmented turbofan
engines, the diffuser may be combined with a mixer so that a mixed stream enters