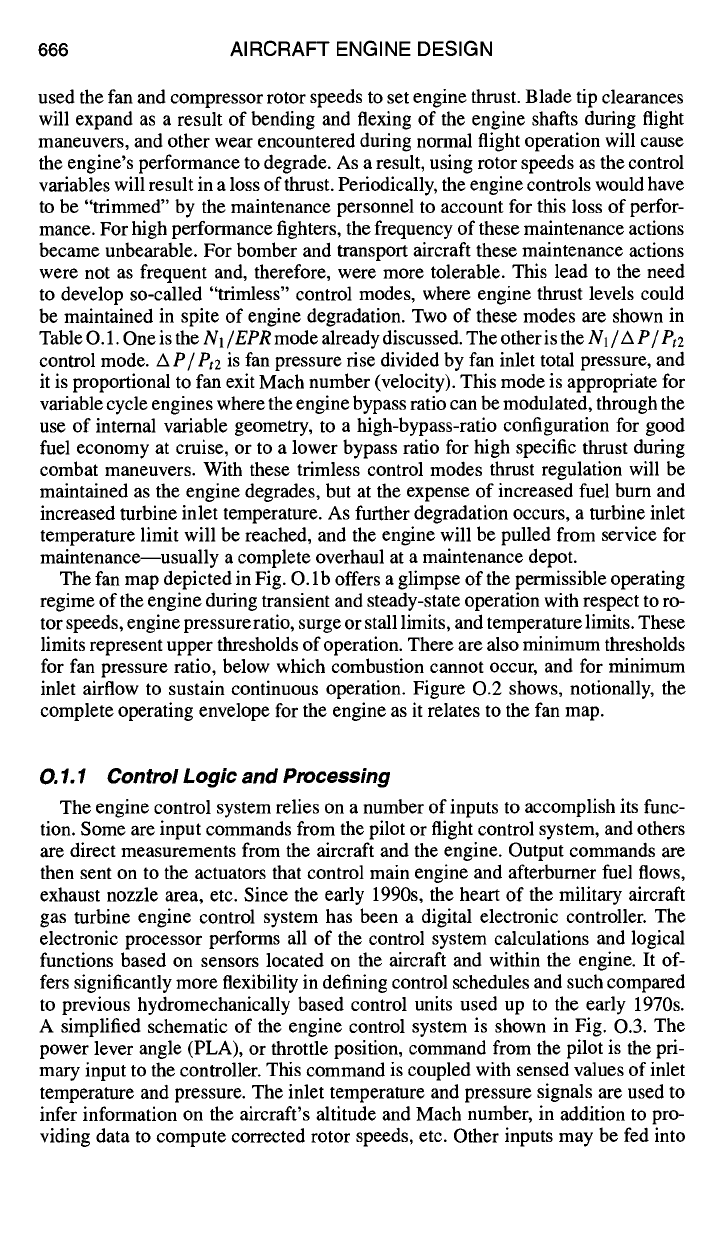
666 AIRCRAFT ENGINE DESIGN
used the fan and compressor rotor speeds to set engine thrust. Blade tip clearances
will expand as a result of bending and flexing of the engine shafts during flight
maneuvers, and other wear encountered during normal flight operation will cause
the engine's performance to degrade. As a result, using rotor speeds as the control
variables will result in a loss of thrust. Periodically, the engine controls would have
to be "trimmed" by the maintenance personnel to account for this loss of perfor-
mance. For high performance fighters, the frequency of these maintenance actions
became unbearable. For bomber and transport aircraft these maintenance actions
were not as frequent and, therefore, were more tolerable. This lead to the need
to develop so-called "trimless" control modes, where engine thrust levels could
be maintained in spite of engine degradation. Two of these modes are shown in
Table O. 1. One is the
N1/EPR
mode already discussed. The other is the N1 / A P/Pt2
control mode.
AP/Pt2
is fan pressure rise divided by fan inlet total pressure, and
it is proportional to fan exit Mach number (velocity). This mode is appropriate for
variable cycle engines where the engine bypass ratio can be modulated, through the
use of internal variable geometry, to a high-bypass-ratio configuration for good
fuel economy at cruise, or to a lower bypass ratio for high specific thrust during
combat maneuvers. With these trimless control modes thrust regulation will be
maintained as the engine degrades, but at the expense of increased fuel burn and
increased turbine inlet temperature. As further degradation occurs, a turbine inlet
temperature limit will be reached, and the engine will be pulled from service for
maintenance--usually a complete overhaul at a maintenance depot.
The fan map depicted in Fig. O. lb offers a glimpse of the permissible operating
regime of the engine during transient and steady-state operation with respect to ro-
tor speeds, engine pressure ratio, surge or stall limits, and temperature limits. These
limits represent upper thresholds of operation. There are also minimum thresholds
for fan pressure ratio, below which combustion cannot occur, and for minimum
inlet airflow to sustain continuous operation. Figure 0.2 shows, notionally, the
complete operating envelope for the engine as it relates to the fan map.
Oo
1.1 Control Logic and Processing
The engine control system relies on a number of inputs to accomplish its func-
tion. Some are input commands from the pilot or flight control system, and others
are direct measurements from the aircraft and the engine. Output commands are
then sent on to the actuators that control main engine and afterburner fuel flows,
exhaust nozzle area, etc. Since the early 1990s, the heart of the military aircraft
gas turbine engine control system has been a digital electronic controller. The
electronic processor performs all of the control system calculations and logical
functions based on sensors located on the aircraft and within the engine. It of-
fers significantly more flexibility in defining control schedules and such compared
to previous hydromechanically based control units used up to the early 1970s.
A simplified schematic of the engine control system is shown in Fig. 0.3. The
power lever angle (PLA), or throttle position, command from the pilot is the pri-
mary input to the controller. This command is coupled with sensed values of inlet
temperature and pressure. The inlet temperature and pressure signals are used to
infer information on the aircraft's altitude and Mach number, in addition to pro-
viding data to compute corrected rotor speeds, etc. Other inputs may be fed into