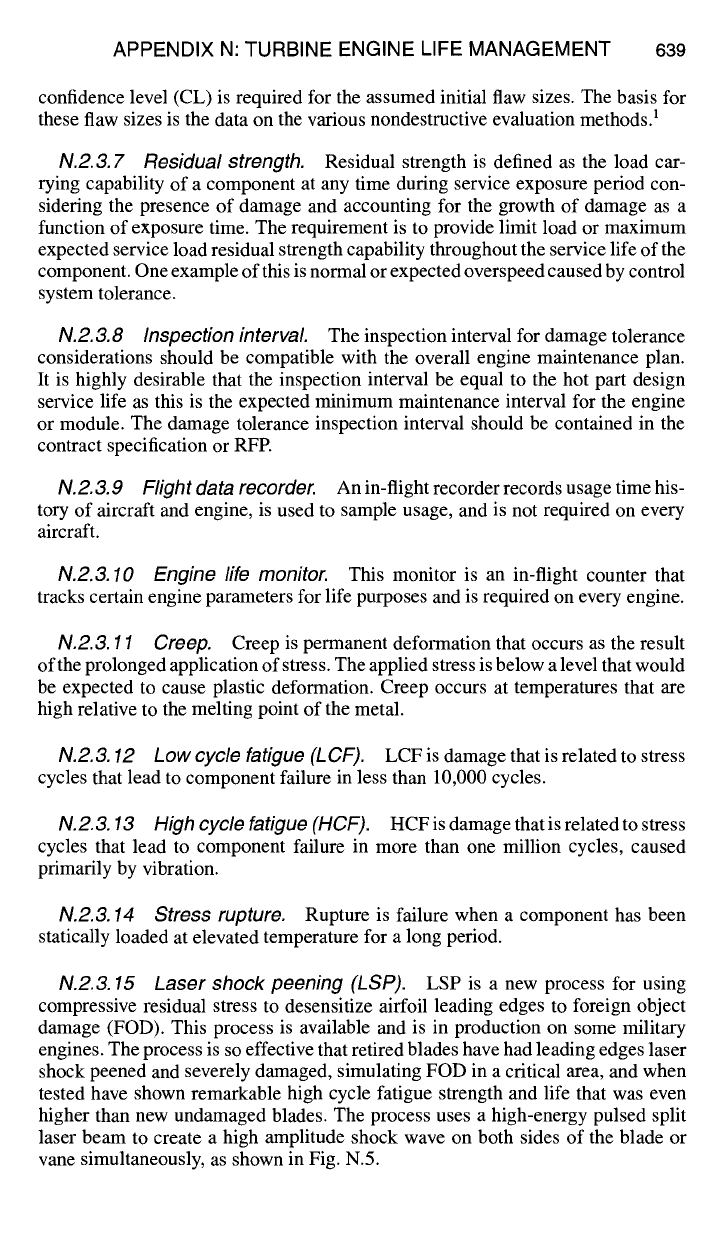
APPENDIX N: TURBINE ENGINE LIFE MANAGEMENT 639
confidence level (CL) is required for the assumed initial flaw sizes. The basis for
these flaw sizes is the data on the various nondestructive evaluation methods. 1
N.2.3.7 Residual strength.
Residual strength is defined as the load car-
rying capability of a component at any time during service exposure period con-
sidering the presence of damage and accounting for the growth of damage as a
function of exposure time. The requirement is to provide limit load or maximum
expected service load residual strength capability throughout the service life of the
component. One example of this is normal or expected overspeed caused by control
system tolerance.
N.2.3.8 Inspection interval
The inspection interval for damage tolerance
considerations should be compatible with the overall engine maintenance plan.
It is highly desirable that the inspection interval be equal to the hot part design
service life as this is the expected minimum maintenance interval for the engine
or module. The damage tolerance inspection interval should be contained in the
contract specification or RFP.
N.2.3.9 Flight data recorder.
An in-flight recorder records usage time his-
tory of aircraft and engine, is used to sample usage, and is not required on every
aircraft.
N.2.3.10 Engine life monitor.
This monitor is an in-flight counter that
tracks certain engine parameters for life purposes and is required on every engine.
N.2.3. 11 Creep.
Creep is permanent deformation that occurs as the result
of the prolonged application of stress. The applied stress is below a level that would
be expected to cause plastic deformation. Creep occurs at temperatures that are
high relative to the melting point of the metal.
N.2.3.12 Low cycle fatigue (LCF).
LCF is damage that is related to stress
cycles that lead to component failure in less than 10,000 cycles.
N.2.3.13 High cycle fatigue (HCF).
HCFisdamagethatisrelatedtostress
cycles that lead to component failure in more than one million cycles, caused
primarily by vibration.
N.2.3.14 Stress rupture.
Rupture is failure when a component has been
statically loaded at elevated temperature for a long period.
N.2.3.15 Laser shock peening (LSP).
LSP is a new process for using
compressive residual stress to desensitize airfoil leading edges to foreign object
damage (FOD). This process is available and is in production on some military
engines. The process is so effective that retired blades have had leading edges laser
shock peened and severely damaged, simulating FOD in a critical area, and when
tested have shown remarkable high cycle fatigue strength and life that was even
higher than new undamaged blades. The process uses a high-energy pulsed split
laser beam to create a high amplitude shock wave on both sides of the blade or
vane simultaneously, as shown in Fig. N.5.