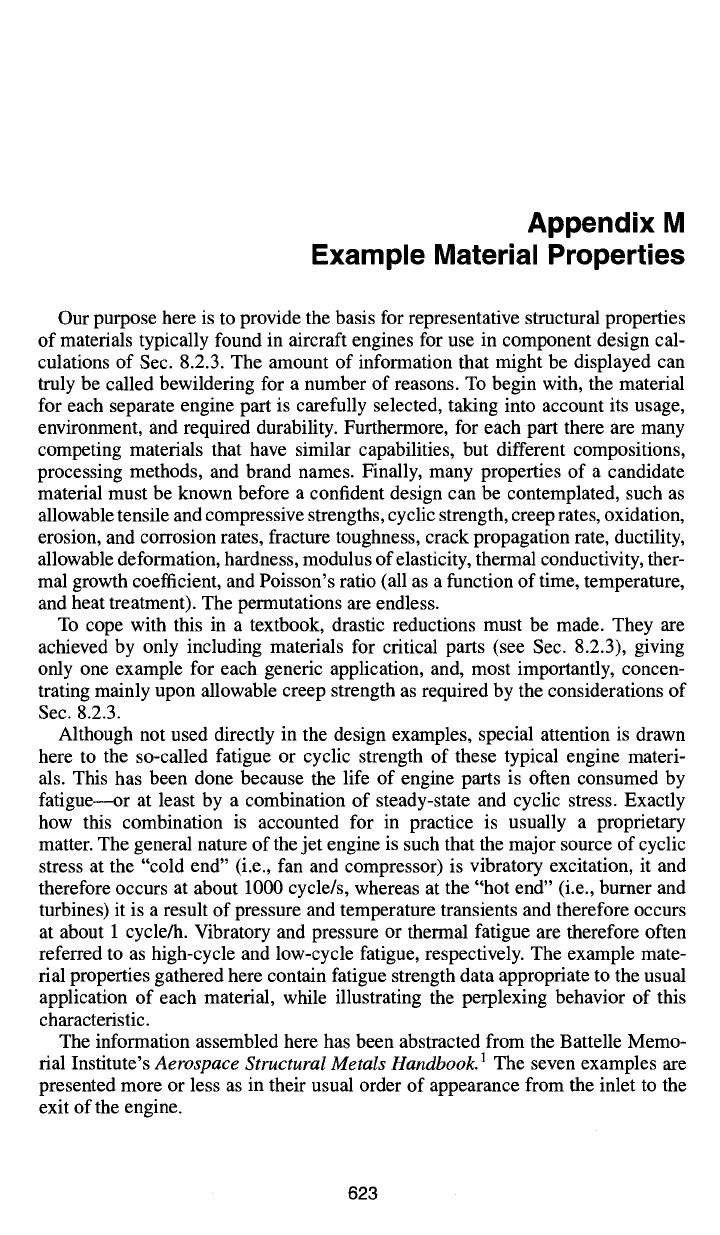
Appendix M
Example Material Properties
Our purpose here is to provide the basis for representative structural properties
of materials typically found in aircraft engines for use in component design cal-
culations of Sec. 8.2.3. The amount of information that might be displayed can
truly be called bewildering for a number of reasons. To begin with, the material
for each separate engine part is carefully selected, taking into account its usage,
environment, and required durability. Furthermore, for each part there are many
competing materials that have similar capabilities, but different compositions,
processing methods, and brand names. Finally, many properties of a candidate
material must be known before a confident design can be contemplated, such as
allowable tensile and compressive strengths, cyclic strength, creep rates, oxidation,
erosion, and corrosion rates, fracture toughness, crack propagation rate, ductility,
allowable deformation, hardness, modulus of elasticity, thermal conductivity, ther-
mal growth coefficient, and Poisson's ratio (all as a function of time, temperature,
and heat treatment). The permutations are endless.
To cope with this in a textbook, drastic reductions must be made. They are
achieved by only including materials for critical parts (see Sec. 8.2.3), giving
only one example for each generic application, and, most importantly, concen-
trating mainly upon allowable creep strength as required by the considerations of
Sec. 8.2.3.
Although not used directly in the design examples, special attention is drawn
here to the so-called fatigue or cyclic strength of these typical engine materi-
als. This has been done because the life of engine parts is often consumed by
fatigue--or at least by a combination of steady-state and cyclic stress. Exactly
how this combination is accounted for in practice is usually a proprietary
matter. The general nature of the jet engine is such that the major source of cyclic
stress at the "cold end" (i.e., fan and compressor) is vibratory excitation, it and
therefore occurs at about 1000 cycle/s, whereas at the "hot end" (i.e., burner and
turbines) it is a result of pressure and temperature transients and therefore occurs
at about 1 cycle/h. Vibratory and pressure or thermal fatigue are therefore often
referred to as high-cycle and low-cycle fatigue, respectively. The example mate-
rial properties gathered here contain fatigue strength data appropriate to the usual
application of each material, while illustrating the perplexing behavior of this
characteristic.
The information assembled here has been abstracted from the Battelle Memo-
rial Institute's
Aerospace Structural Metals Handbook. 1 The
seven examples are
presented more or less as in their usual order of appearance from the inlet to the
exit of the engine.
623