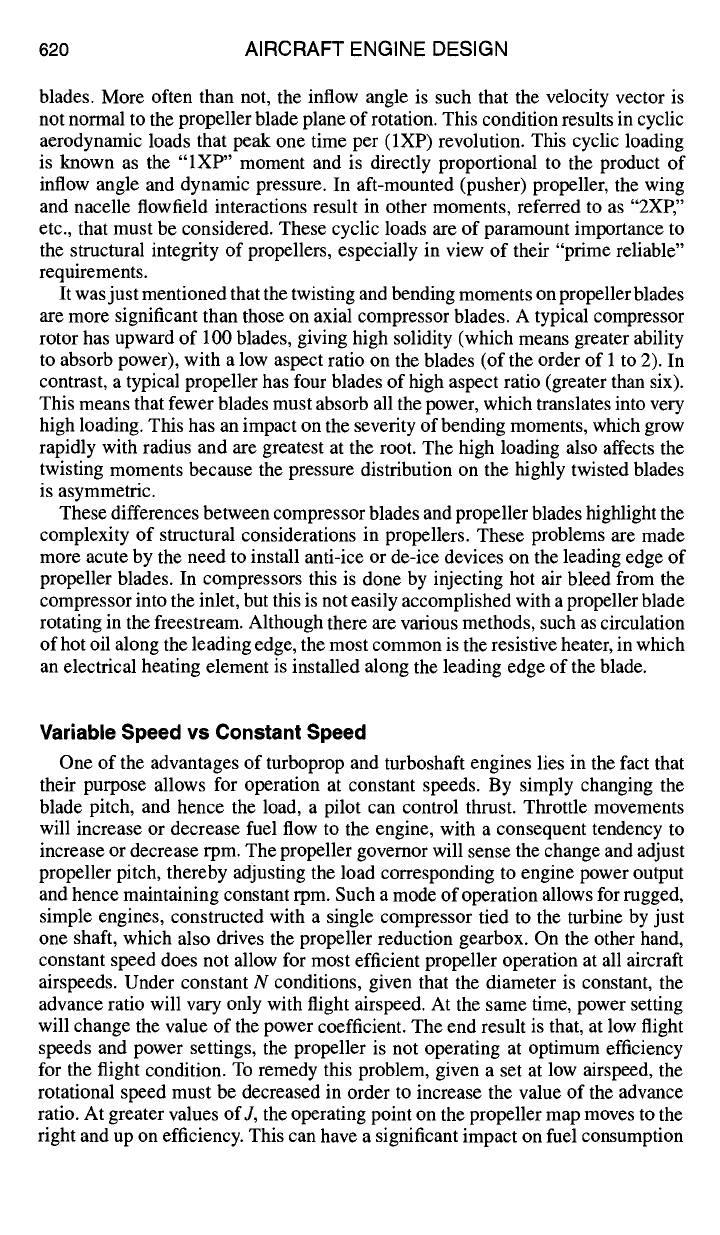
620 AIRCRAFT ENGINE DESIGN
blades. More often than not, the inflow angle is such that the velocity vector is
not normal to the propeller blade plane of rotation. This condition results in cyclic
aerodynamic loads that peak one time per (1XP) revolution. This cyclic loading
is known as the "IXP" moment and is directly proportional to the product of
inflow angle and dynamic pressure. In aft-mounted (pusher) propeller, the wing
and nacelle flowfield interactions result in other moments, referred to as "2XP,"
etc., that must be considered. These cyclic loads are of paramount importance to
the structural integrity of propellers, especially in view of their "prime reliable"
requirements.
It was just mentioned that the twisting and bending moments on propeller blades
are more significant than those on axial compressor blades. A typical compressor
rotor has upward of 100 blades, giving high solidity (which means greater ability
to absorb power), with a low aspect ratio on the blades (of the order of 1 to 2). In
contrast, a typical propeller has four blades of high aspect ratio (greater than six).
This means that fewer blades must absorb all the power, which translates into very
high loading. This has an impact on the severity of bending moments, which grow
rapidly with radius and are greatest at the root. The high loading also affects the
twisting moments because the pressure distribution on the highly twisted blades
is asymmetric.
These differences between compressor blades and propeller blades highlight the
complexity of structural considerations in propellers. These problems are made
more acute by the need to install anti-ice or de-ice devices on the leading edge of
propeller blades. In compressors this is done by injecting hot air bleed from the
compressor into the inlet, but this is not easily accomplished with a propeller blade
rotating in the freestream. Although there are various methods, such as circulation
of hot oil along the leading edge, the most common is the resistive heater, in which
an electrical heating element is installed along the leading edge of the blade.
Variable Speed vs Constant Speed
One of the advantages of turboprop and turboshaft engines lies in the fact that
their purpose allows for operation at constant speeds. By simply changing the
blade pitch, and hence the load, a pilot can control thrust. Throttle movements
will increase or decrease fuel flow to the engine, with a consequent tendency to
increase or decrease rpm. The propeller governor will sense the change and adjust
propeller pitch, thereby adjusting the load corresponding to engine power output
and hence maintaining constant rpm. Such a mode of operation allows for rugged,
simple engines, constructed with a single compressor tied to the turbine by just
one shaft, which also drives the propeller reduction gearbox. On the other hand,
constant speed does not allow for most efficient propeller operation at all aircraft
airspeeds. Under constant N conditions, given that the diameter is constant, the
advance ratio will vary only with flight airspeed. At the same time, power setting
will change the value of the power coefficient. The end result is that, at low flight
speeds and power settings, the propeller is not operating at optimum efficiency
for the flight condition. To remedy this problem, given a set at low airspeed, the
rotational speed must be decreased in order to increase the value of the advance
ratio. At greater values of J, the operating point on the propeller map moves to the
right and up on efficiency. This can have a significant impact on fuel consumption