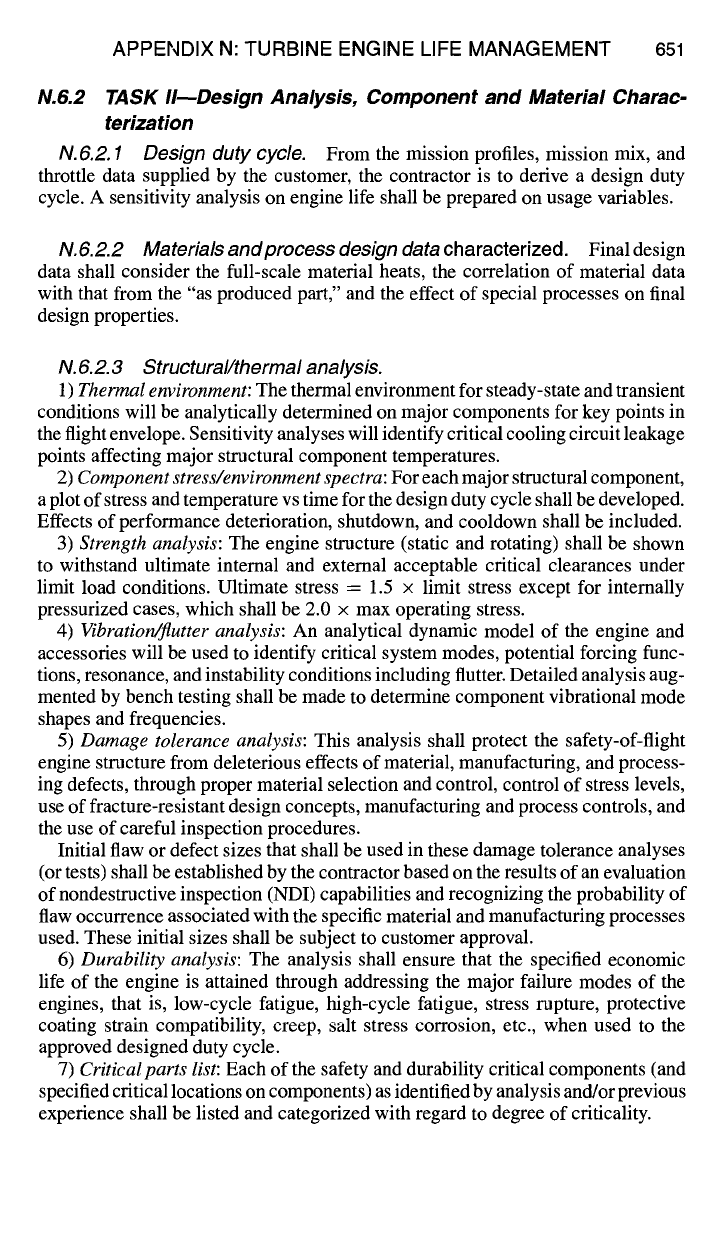
APPENDIX N: TURBINE ENGINE LIFE MANAGEMENT 651
N.6.2 TASK II--Design Analysis, Component and Material Charac-
terization
N.6.2. I Design duty cycle.
From the mission profiles, mission mix, and
throttle data supplied by the customer, the contractor is to derive a design duty
cycle. A sensitivity analysis on engine life shall be prepared on usage variables.
IV.6.2.2 Materials and process design data
characterized. Final design
data shall consider the full-scale material heats, the correlation of material data
with that from the "as produced part," and the effect of special processes on final
design properties.
N.6.2.3 Structural~thermal analysis.
1) Thermal environment:
The thermal environment for steady-state and transient
conditions will be analytically determined on major components for key points in
the flight envelope. Sensitivity analyses will identify critical cooling circuit leakage
points affecting major structural component temperatures.
2)
Component stress~environment spectra:
For each major structural component,
a plot of stress and temperature vs time for the design duty cycle shall be developed.
Effects of performance deterioration, shutdown, and cooldown shall be included.
3)
Strength analysis:
The engine structure (static and rotating) shall be shown
to withstand ultimate internal and external acceptable critical clearances under
limit load conditions. Ultimate stress = 1.5 × limit stress except for intemally
pressurized cases, which shall be 2.0 × max operating stress.
4)
Vibration~flutter analysis:
An analytical dynamic model of the engine and
accessories will be used to identify critical system modes, potential forcing func-
tions, resonance, and instability conditions including flutter. Detailed analysis aug-
mented by bench testing shall be made to determine component vibrational mode
shapes and frequencies.
5)
Damage tolerance analysis:
This analysis shall protect the safety-of-flight
engine structure from deleterious effects of material, manufacturing, and process-
ing defects, through proper material selection and control, control of stress levels,
use of fracture-resistant design concepts, manufacturing and process controls, and
the use of careful inspection procedures.
Initial flaw or defect sizes that shall be used in these damage tolerance analyses
(or tests) shall be established by the contractor based on the results of an evaluation
of nondestructive inspection (NDI) capabilities and recognizing the probability of
flaw occurrence associated with the specific material and manufacturing processes
used. These initial sizes shall be subject to customer approval.
6)
Durability analysis:
The analysis shall ensure that the specified economic
life of the engine is attained through addressing the major failure modes of the
engines, that is, low-cycle fatigue, high-cycle fatigue, stress rupture, protective
coating strain compatibility, creep, salt stress corrosion, etc., when used to the
approved designed duty cycle.
7)
Critical parts list:
Each of the safety and durability critical components (and
specified critical locations on components) as identified by analysis and/or previous
experience shall be listed and categorized with regard to degree of criticality.