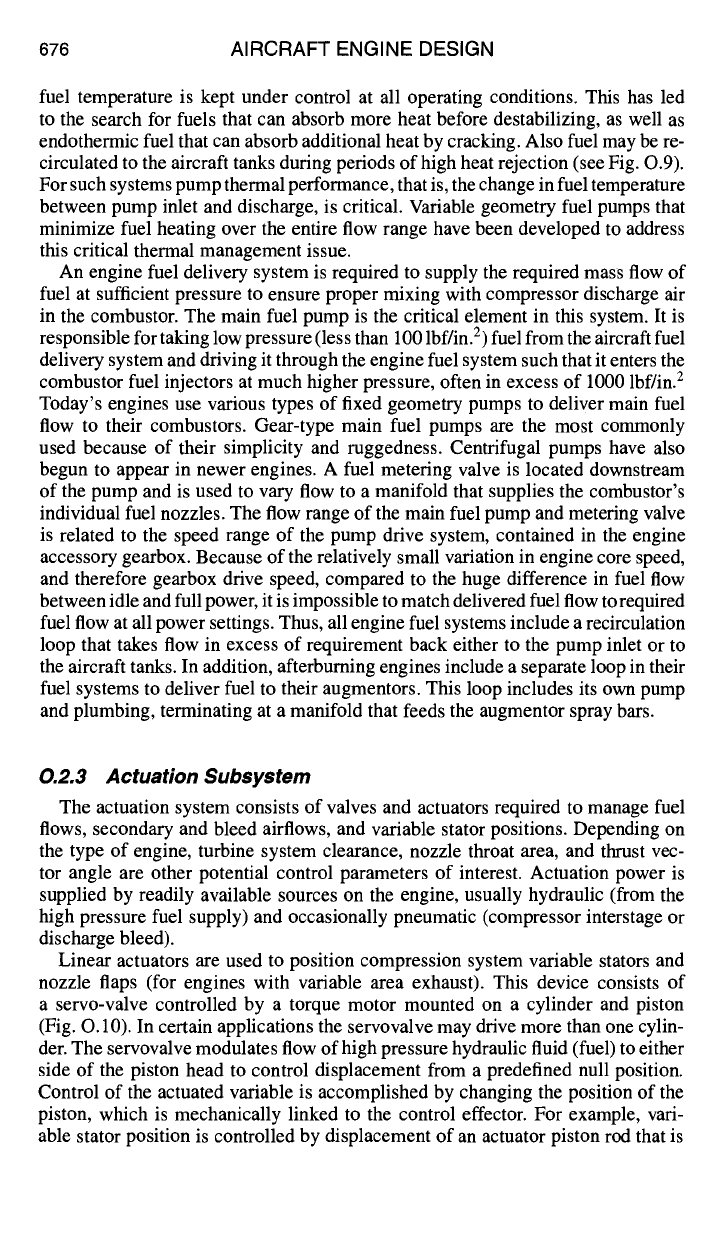
676 AIRCRAFT ENGINE DESIGN
fuel temperature is kept under control at all operating conditions. This has led
to the search for fuels that can absorb more heat before destabilizing, as well as
endothermic fuel that can absorb additional heat by cracking. Also fuel may be re-
circulated to the aircraft tanks during periods of high heat rejection (see Fig. 0.9).
For such systems pump thermal performance, that is, the change in fuel temperature
between pump inlet and discharge, is critical. Variable geometry fuel pumps that
minimize fuel heating over the entire flow range have been developed to address
this critical thermal management issue.
An engine fuel delivery system is required to supply the required mass flow of
fuel at sufficient pressure to ensure proper mixing with compressor discharge air
in the combustor. The main fuel pump is the critical element in this system. It is
responsible for taking low pressure (less than 100 lbf/in. 2) fuel from the aircraft fuel
delivery system and driving it through the engine fuel system such that it enters the
combustor fuel injectors at much higher pressure, often in excess of 1000 lbf/in. 2
Today's engines use various types of fixed geometry pumps to deliver main fuel
flow to their combustors. Gear-type main fuel pumps are the most commonly
used because of their simplicity and ruggedness. Centrifugal pumps have also
begun to appear in newer engines. A fuel metering valve is located downstream
of the pump and is used to vary flow to a manifold that supplies the combustor's
individual fuel nozzles. The flow range of the main fuel pump and metering valve
is related to the speed range of the pump drive system, contained in the engine
accessory gearbox. Because of the relatively small variation in engine core speed,
and therefore gearbox drive speed, compared to the huge difference in fuel flow
between idle and full power, it is impossible to match delivered fuel flow to required
fuel flow at all power settings. Thus, all engine fuel systems include a recirculation
loop that takes flow in excess of requirement back either to the pump inlet or to
the aircraft tanks. In addition, afterburning engines include a separate loop in their
fuel systems to deliver fuel to their augmentors. This loop includes its own pump
and plumbing, terminating at a manifold that feeds the augmentor spray bars.
0.2.3 Actuation Subsystem
The actuation system consists of valves and actuators required to manage fuel
flows, secondary and bleed airflows, and variable stator positions. Depending on
the type of engine, turbine system clearance, nozzle throat area, and thrust vec-
tor angle are other potential control parameters of interest. Actuation power is
supplied by readily available sources on the engine, usually hydraulic (from the
high pressure fuel supply) and occasionally pneumatic (compressor interstage or
discharge bleed).
Linear actuators are used to position compression system variable stators and
nozzle flaps (for engines with variable area exhaust). This device consists of
a servo-valve controlled by a torque motor mounted on a cylinder and piston
(Fig. O. 10). In certain applications the servovalve may drive more than one cylin-
der. The servovalve modulates flow of high pressure hydraulic fluid (fuel) to either
side of the piston head to control displacement from a predefined null position.
Control of the actuated variable is accomplished by changing the position of the
piston, which is mechanically linked to the control effector. For example, vari-
able stator position is controlled by displacement of an actuator piston rod that is