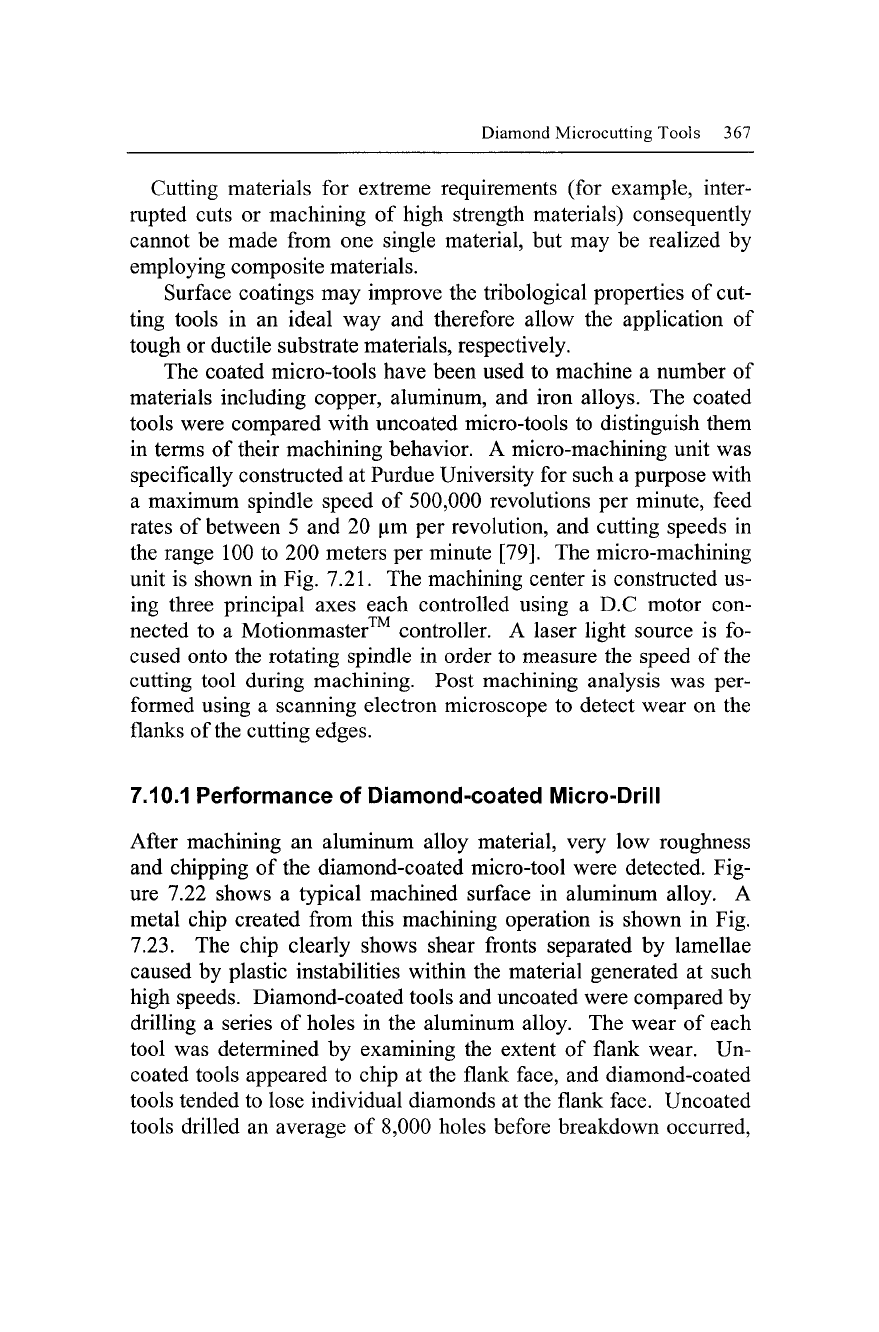
Diamond Microcutting Tools 367
Cutting materials for extreme requirements (for example, inter-
rupted cuts or machining of high strength materials) consequently
cannot be made from one single material, but may be realized by
employing composite materials.
Surface coatings may improve the tribological properties of cut-
ting tools in an ideal way and therefore allow the application of
tough or ductile substrate materials, respectively.
The coated micro-tools have been used to machine a number of
materials including copper, aluminum, and iron alloys. The coated
tools were compared with uncoated micro-tools to distinguish them
in terms of their machining behavior. A micro-machining unit was
specifically constructed at Purdue University for such a purpose with
a maximum spindle speed of 500,000 revolutions per minute, feed
rates of between 5 and 20 [im per revolution, and cutting speeds in
the range 100 to 200 meters per minute [79]. The micro-machining
unit is shown in Fig. 7.21. The machining center is constructed us-
ing three principal axes each controlled using a D.C motor con-
nected to a Motionmaster^^ controller. A laser light source is fo-
cused onto the rotating spindle in order to measure the speed of the
cutting tool during machining. Post machining analysis was per-
formed using a scanning electron microscope to detect wear on the
flanks of the cutting edges.
7.10.1 Performance of Diamond-coated Micro-Drill
After machining an aluminum alloy material, very low roughness
and chipping of the diamond-coated micro-tool were detected. Fig-
ure 7.22 shows a typical machined surface in aluminum alloy. A
metal chip created from this machining operation is shown in Fig.
7.23.
The chip clearly shows shear fronts separated by lamellae
caused by plastic instabilities within the material generated at such
high speeds. Diamond-coated tools and uncoated were compared by
drilling a series of holes in the aluminum alloy. The wear of each
tool was determined by examining the extent of flank wear. Un-
coated tools appeared to chip at the flank face, and diamond-coated
tools tended to lose individual diamonds at the flank face. Uncoated
tools drilled an average of
8,000
holes before breakdown occurred.