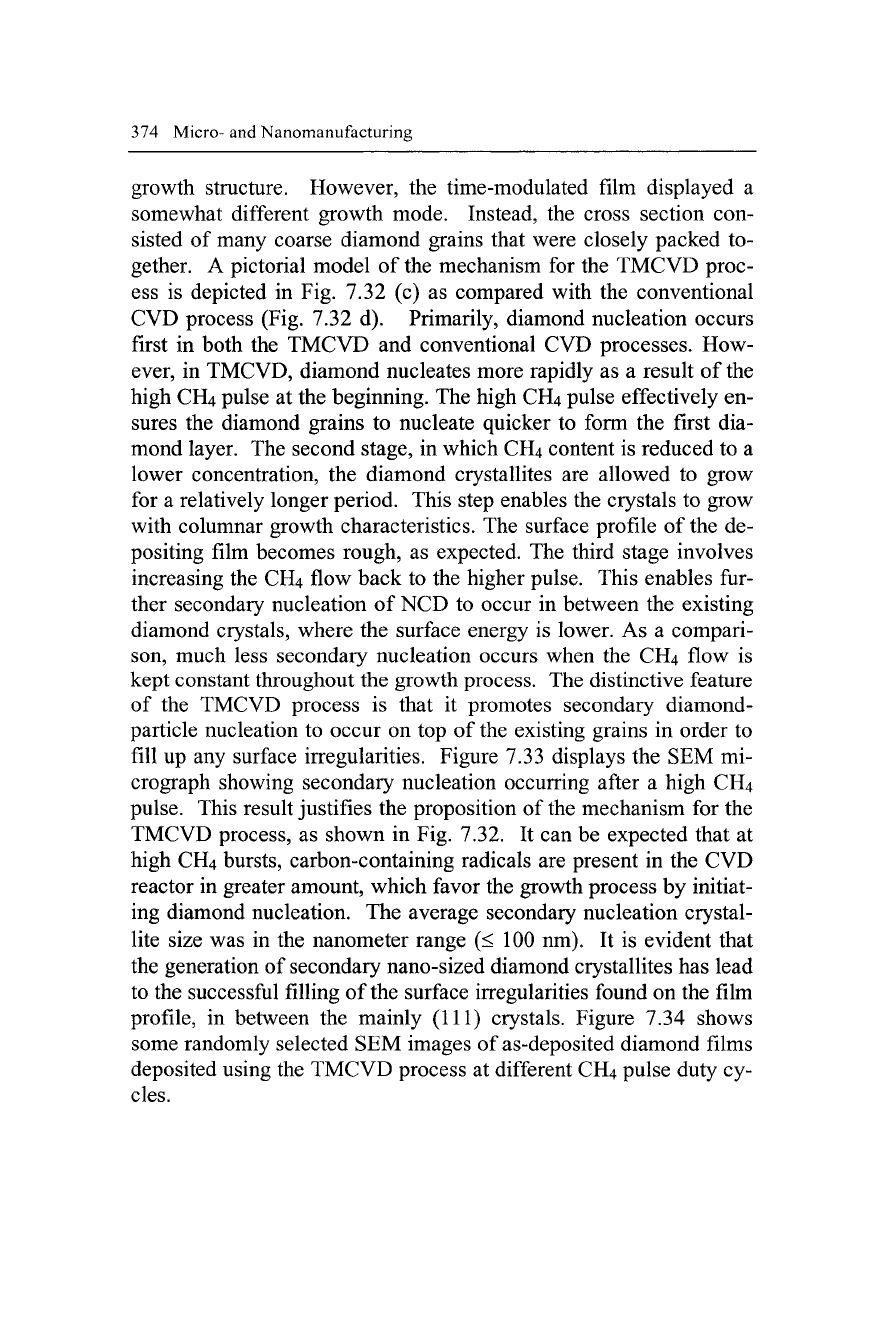
374 Micro- and Nanomanufacturing
growth structure. However, the time-modulated film displayed a
somewhat different growth mode. Instead, the cross section con-
sisted of many coarse diamond grains that were closely packed to-
gether. A pictorial model of the mechanism for the TMCVD proc-
ess is depicted in Fig. 7.32 (c) as compared with the conventional
CVD process (Fig. 7.32 d). Primarily, diamond nucleation occurs
first in both the TMCVD and conventional CVD processes. How-
ever, in TMCVD, diamond nucleates more rapidly as a result of the
high CH4 pulse at the beginning. The high CH4 pulse effectively en-
sures the diamond grains to nucleate quicker to form the first dia-
mond layer. The second stage, in which CH4 content is reduced to a
lower concentration, the diamond crystallites are allowed to grow
for a relatively longer period. This step enables the crystals to grow
with columnar growth characteristics. The surface profile of the de-
positing film becomes rough, as expected. The third stage involves
increasing the CH4 flow back to the higher pulse. This enables fur-
ther secondary nucleation of NCD to occur in between the existing
diamond crystals, where the surface energy is lower. As a compari-
son, much less secondary nucleation occurs when the CH4 flow is
kept constant throughout the growth process. The distinctive feature
of the TMCVD process is that it promotes secondary diamond-
particle nucleation to occur on top of the existing grains in order to
fill up any surface irregularities. Figure 7.33 displays the SEM mi-
crograph showing secondary nucleation occurring after a high CH4
pulse. This result justifies the proposition of the mechanism for the
TMCVD process, as shown in Fig. 7.32. It can be expected that at
high CH4 bursts, carbon-containing radicals are present in the CVD
reactor in greater amount, which favor the growth process by initiat-
ing diamond nucleation. The average secondary nucleation crystal-
lite size was in the nanometer range (< 100 nm). It is evident that
the generation of secondary nano-sized diamond crystallites has lead
to the successful filling of the surface irregularities found on the film
profile, in between the mainly (111) crystals. Figure 7.34 shows
some randomly selected SEM images of as-deposited diamond films
deposited using the TMCVD process at different CH4 pulse duty cy-
cles.