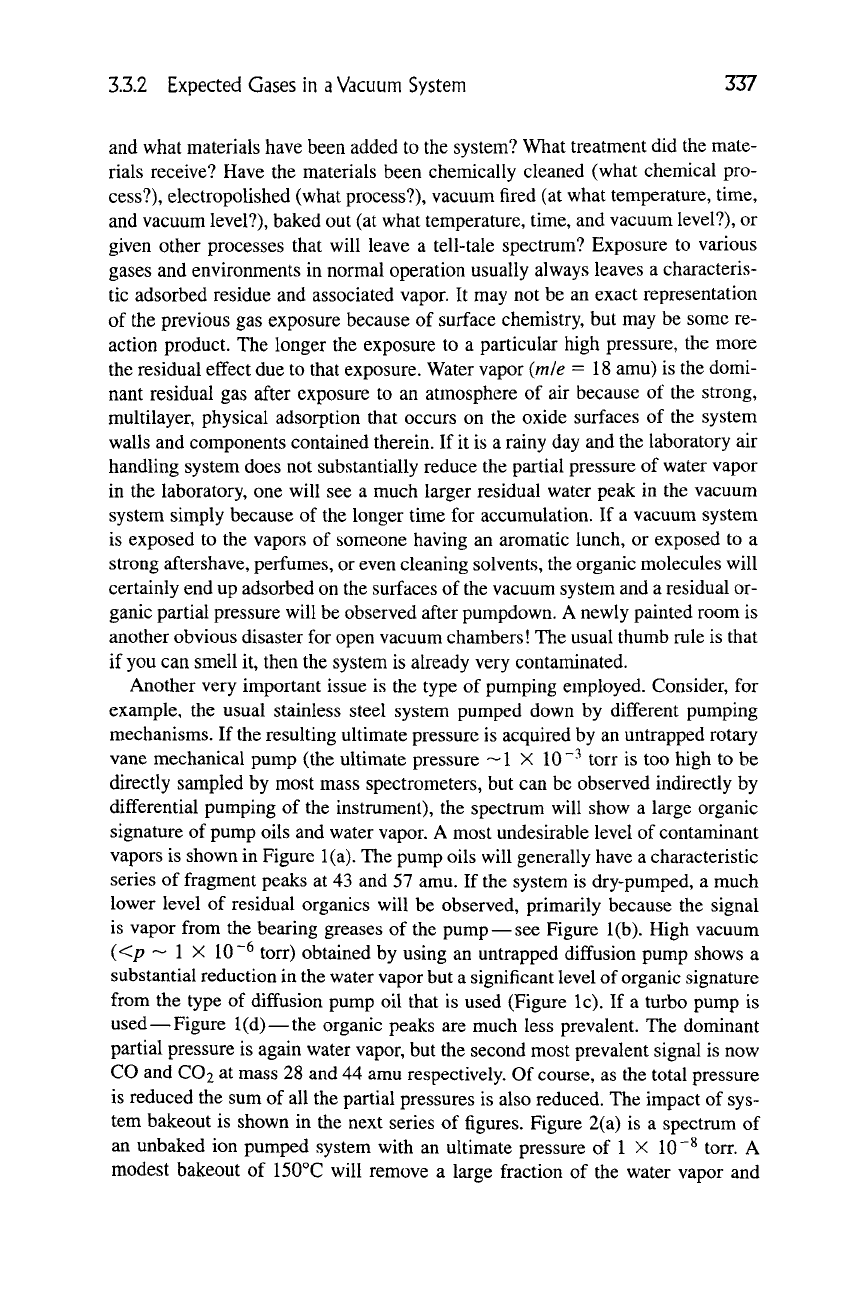
33.2 Expected Gases in
a
Vacuum System 337
and what materials have been added to the system? What treatment did the mate-
rials receive? Have the materials been chemically cleaned (what chemical pro-
cess?),
electropolished (what process?), vacuum fired (at what temperature, time,
and vacuum level?), baked out (at what temperature, time, and vacuum level?), or
given other processes that will leave a tell-tale spectrum? Exposure to various
gases and environments in normal operation usually always leaves a characteris-
tic adsorbed residue and associated vapor. It may not be an exact representation
of the previous gas exposure because of surface chemistry, but may be some re-
action product. The longer the exposure to a particular high pressure, the more
the residual effect due to that exposure. Water vapor {mie =18 amu) is the domi-
nant residual gas after exposure to an atmosphere of air because of the strong,
multilayer, physical adsorption that occurs on the oxide surfaces of the system
walls and components contained therein. If it is a rainy day and the laboratory air
handling system does not substantially reduce the partial pressure of water vapor
in the laboratory, one will see a much larger residual water peak in the vacuum
system simply because of the longer time for accumulation. If a vacuum system
is exposed to the vapors of someone having an aromatic lunch, or exposed to a
strong aftershave, perfumes, or even cleaning solvents, the organic molecules will
certainly end up adsorbed on the surfaces of the vacuum system and a residual or-
ganic partial pressure will be observed after pumpdown. A newly painted room is
another obvious disaster for open vacuum chambers! The usual thumb rule is that
if you can smell it, then the system is already very contaminated.
Another very important issue is the type of pumping employed. Consider, for
example, the usual stainless steel system pumped down by different pumping
mechanisms. If the resulting ultimate pressure is acquired by an untrapped rotary
vane mechanical pump (the ultimate pressure ~1 X 10"'^ torr is too high to be
directly sampled by most mass spectrometers, but can be observed indirectly by
differential pumping of the instrument), the spectrum will show a large organic
signature of pump oils and water vapor. A most undesirable level of contaminant
vapors is shown in Figure 1(a). The pump oils will generally have a characteristic
series of fragment peaks at 43 and 57 amu. If the system is dry-pumped, a much
lower level of residual organics will be observed, primarily because the signal
is vapor from the bearing greases of the pump —
see
Figure 1(b). High vacuum
{<p ~ 1 X 10~^ torr) obtained by using an untrapped diffusion pump shows a
substantial reduction in the water vapor but a significant level of organic signature
from the type of diffusion pump oil that is used (Figure Ic). If a turbo pump is
used—Figure
1(d)
—
the
organic peaks are much less prevalent. The dominant
partial pressure is again water vapor, but the second most prevalent signal is now
CO and CO2 at mass 28 and 44 amu respectively. Of course, as the total pressure
is reduced the sum of all the partial pressures is also reduced. The impact of sys-
tem bakeout is shown in the next series of figures. Figure 2(a) is a spectrum of
an unbaked ion pumped system with an ultimate pressure of 1 X 10"^ torr. A
modest bakeout of 150°C will remove a large fraction of the water vapor and