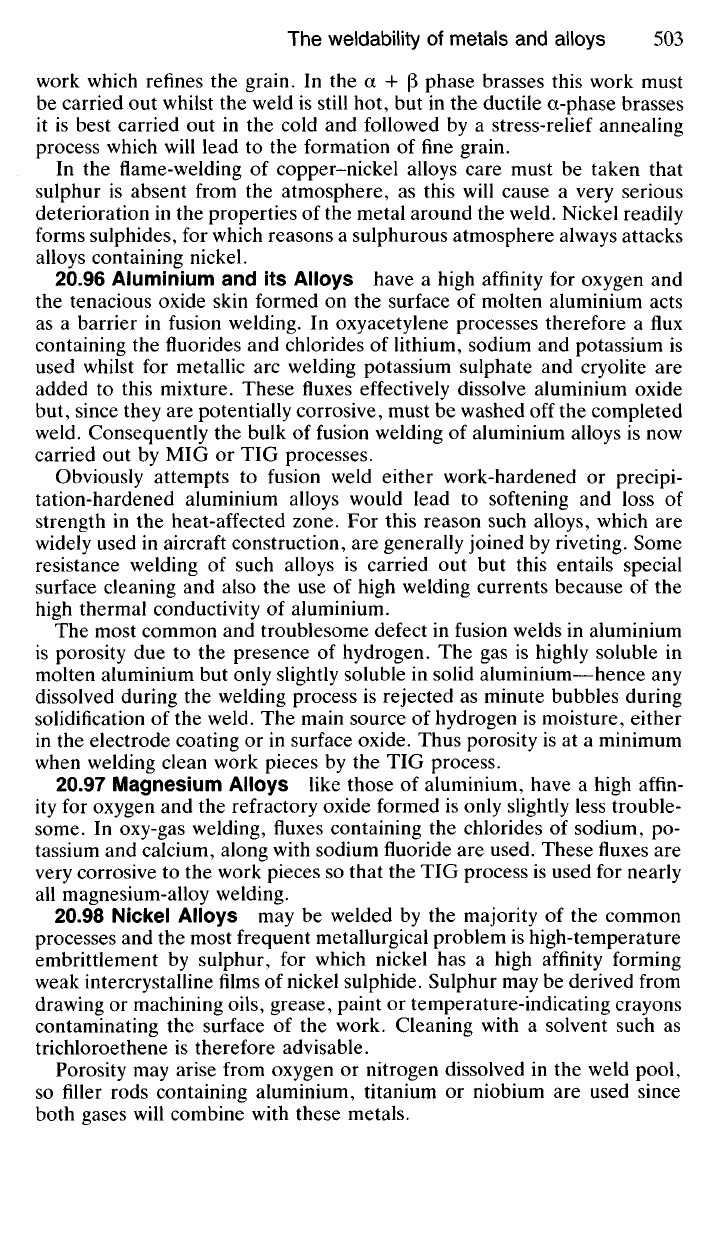
work which refines the grain. In the a + (3 phase brasses this work must
be carried out whilst the weld is still hot, but in the ductile a-phase brasses
it is best carried out in the cold and followed by a stress-relief annealing
process which will lead to the formation of fine grain.
In the flame-welding of copper-nickel alloys care must be taken that
sulphur is absent from the atmosphere, as this will cause a very serious
deterioration in the properties of the metal around the weld. Nickel readily
forms sulphides, for which reasons a sulphurous atmosphere always attacks
alloys containing nickel.
20.96 Aluminium and its Alloys have a high affinity for oxygen and
the tenacious oxide skin formed on the surface of molten aluminium acts
as a barrier in fusion welding. In oxyacetylene processes therefore a flux
containing the fluorides and chlorides of lithium, sodium and potassium is
used whilst for metallic arc welding potassium sulphate and cryolite are
added to this mixture. These fluxes effectively dissolve aluminium oxide
but, since they are potentially corrosive, must be washed off the completed
weld. Consequently the bulk of fusion welding of aluminium alloys is now
carried out by MIG or TIG processes.
Obviously attempts to fusion weld either work-hardened or precipi-
tation-hardened aluminium alloys would lead to softening and loss of
strength in the heat-affected zone. For this reason such alloys, which are
widely used in aircraft construction, are generally joined by riveting. Some
resistance welding of such alloys is carried out but this entails special
surface cleaning and also the use of high welding currents because of the
high thermal conductivity of aluminium.
The most common and troublesome defect in fusion welds in aluminium
is porosity due to the presence of hydrogen. The gas is highly soluble in
molten aluminium but only slightly soluble in solid aluminium—hence any
dissolved during the welding process is rejected as minute bubbles during
solidification of the weld. The main source of hydrogen is moisture, either
in the electrode coating or in surface oxide. Thus porosity is at a minimum
when welding clean work pieces by the TIG process.
20.97 Magnesium Alloys like those of aluminium, have a high affin-
ity for oxygen and the refractory oxide formed is only slightly less trouble-
some. In oxy-gas welding, fluxes containing the chlorides of sodium, po-
tassium and calcium, along with sodium fluoride are used. These fluxes are
very corrosive to the work pieces so that the TIG process is used for nearly
all magnesium-alloy welding.
20.98 Nickel Alloys may be welded by the majority of the common
processes and the most frequent metallurgical problem is high-temperature
embrittlement by sulphur, for which nickel has a high affinity forming
weak intercrystalline films of nickel sulphide. Sulphur may be derived from
drawing or machining oils, grease, paint or temperature-indicating crayons
contaminating the surface of the work. Cleaning with a solvent such as
trichloroethene is therefore advisable.
Porosity may arise from oxygen or nitrogen dissolved in the weld pool,
so filler rods containing aluminium, titanium or niobium are used since
both gases will combine with these metals.