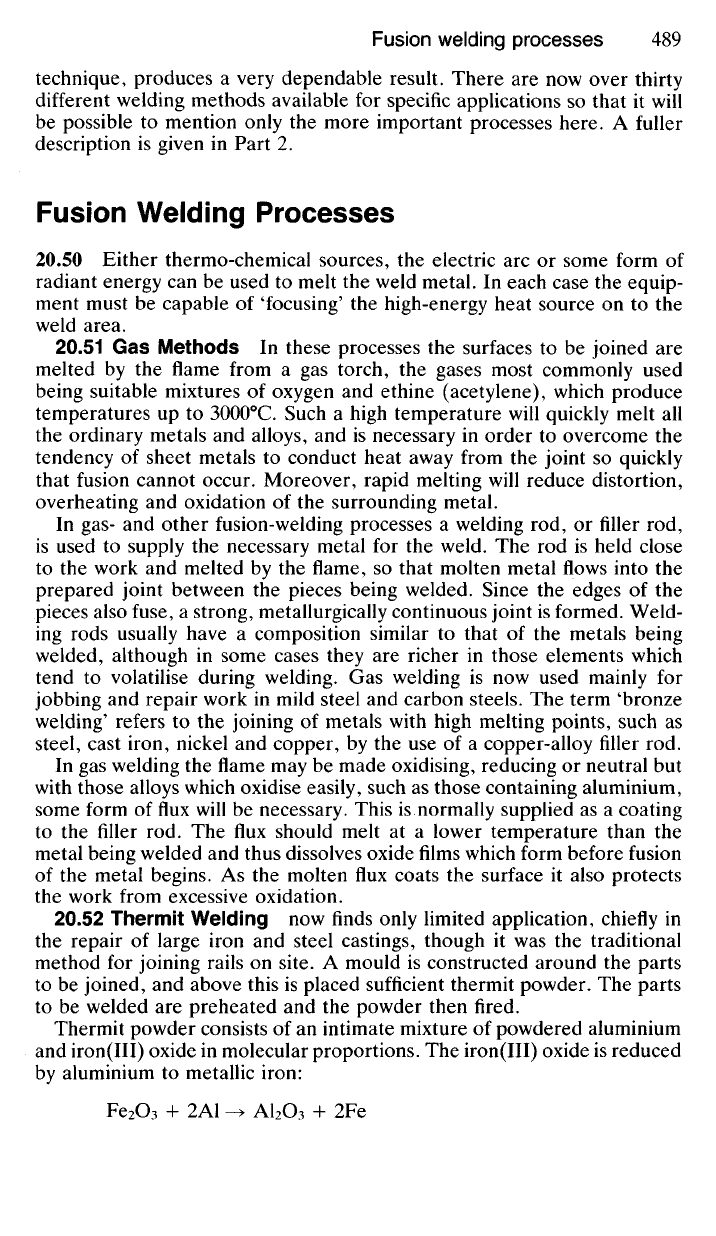
technique, produces a very dependable result. There are now over thirty
different welding methods available for specific applications so that it will
be possible to mention only the more important processes here. A fuller
description is given in Part 2.
Fusion Welding Processes
20.50 Either thermo-chemical sources, the electric arc or some form of
radiant energy can be used to melt the weld metal. In each case the equip-
ment must be capable of 'focusing' the high-energy heat source on to the
weld area.
20.51 Gas Methods In these processes the surfaces to be joined are
melted by the flame from a gas torch, the gases most commonly used
being suitable mixtures of oxygen and ethine (acetylene), which produce
temperatures up to 3000
0
C. Such a high temperature will quickly melt all
the ordinary metals and alloys, and is necessary in order to overcome the
tendency of sheet metals to conduct heat away from the joint so quickly
that fusion cannot occur. Moreover, rapid melting will reduce distortion,
overheating and oxidation of the surrounding metal.
In gas- and other fusion-welding processes a welding rod, or filler rod,
is used to supply the necessary metal for the weld. The rod is held close
to the work and melted by the flame, so that molten metal flows into the
prepared joint between the pieces being welded. Since the edges of the
pieces also fuse, a strong, metallurgically continuous joint is formed. Weld-
ing rods usually have a composition similar to that of the metals being
welded, although in some cases they are richer in those elements which
tend to volatilise during welding. Gas welding is now used mainly for
jobbing and repair work in mild steel and carbon steels. The term 'bronze
welding' refers to the joining of metals with high melting points, such as
steel, cast iron, nickel and copper, by the use of a copper-alloy filler rod.
In gas welding the flame may be made oxidising, reducing or neutral but
with those alloys which oxidise easily, such as those containing aluminium,
some form of flux will be necessary. This is normally supplied as a coating
to the filler rod. The flux should melt at a lower temperature than the
metal being welded and thus dissolves oxide films which form before fusion
of the metal begins. As the molten flux coats the surface it also protects
the work from excessive oxidation.
20.52 Thermit Welding now finds only limited application, chiefly in
the repair of large iron and steel castings, though it was the traditional
method for joining rails on site. A mould is constructed around the parts
to be joined, and above this is placed sufficient thermit powder. The parts
to be welded are preheated and the powder then fired.
Thermit powder consists of an intimate mixture of powdered aluminium
and iron(III) oxide in molecular proportions. The iron(III) oxide is reduced
by aluminium to metallic iron: