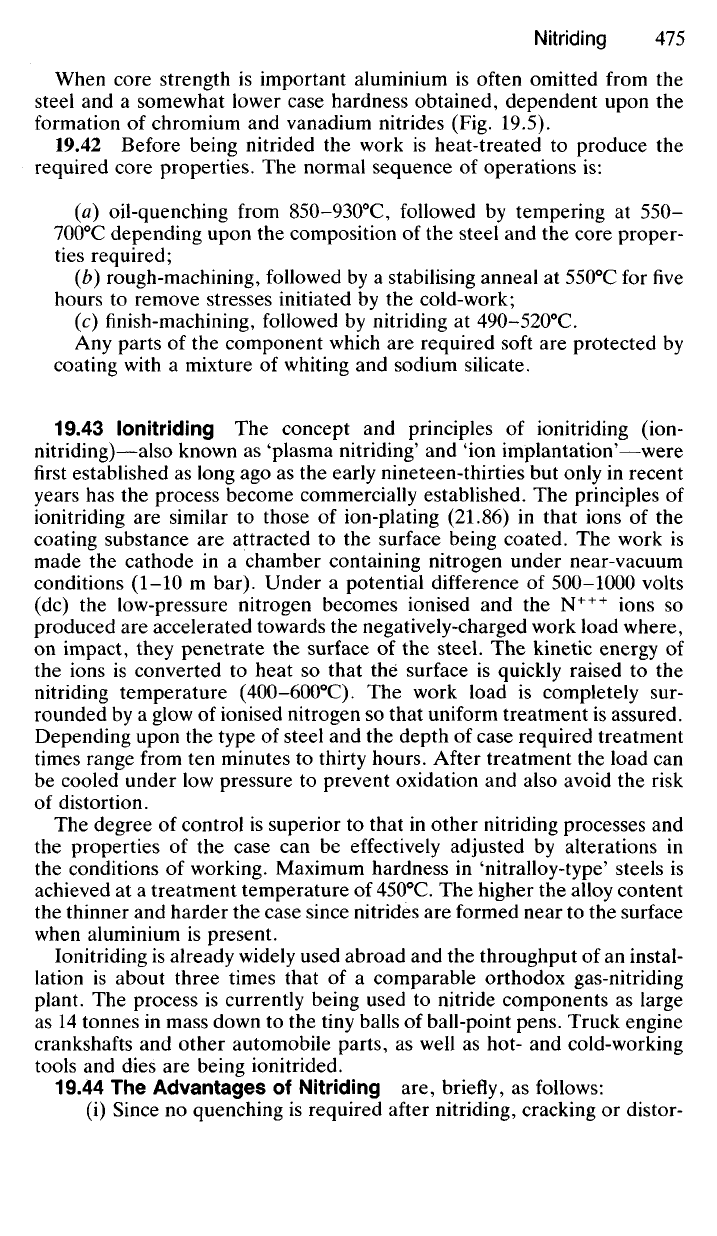
When core strength is important aluminium is often omitted from the
steel and a somewhat lower case hardness obtained, dependent upon the
formation of chromium and vanadium nitrides (Fig. 19.5).
19.42 Before being nitrided the work is heat-treated to produce the
required core properties. The normal sequence of operations is:
(a) oil-quenching from 850-930
0
C, followed by tempering at 550-
700
0
C depending upon the composition of the steel and the core proper-
ties required;
(b) rough-machining, followed by a stabilising anneal at 550
0
C for five
hours to remove stresses initiated by the cold-work;
(c) finish-machining, followed by nitriding at 490-520
0
C.
Any parts of the component which are required soft are protected by
coating with a mixture of whiting and sodium silicate.
19.43 lonitriding The concept and principles of ionitriding (ion-
nitriding)—also known as 'plasma nitriding' and 'ion implantation'—were
first established as long ago as the early nineteen-thirties but only in recent
years has the process become commercially established. The principles of
ionitriding are similar to those of ion-plating (21.86) in that ions of the
coating substance are attracted to the surface being coated. The work is
made the cathode in a chamber containing nitrogen under near-vacuum
conditions (1-10 m bar). Under a potential difference of 500-1000 volts
(dc) the low-pressure nitrogen becomes ionised and the
N
+++
ions so
produced are accelerated towards the negatively-charged work load where,
on impact, they penetrate the surface of the steel. The kinetic energy of
the ions is converted to heat so that the surface is quickly raised to the
nitriding temperature (400-600
0
C). The work load is completely sur-
rounded by a glow of ionised nitrogen so that uniform treatment is assured.
Depending upon the type of steel and the depth of case required treatment
times range from ten minutes to thirty hours. After treatment the load can
be cooled under low pressure to prevent oxidation and also avoid the risk
of distortion.
The degree of control is superior to that in other nitriding processes and
the properties of the case can be effectively adjusted by alterations in
the conditions of working. Maximum hardness in 'nitralloy-type' steels is
achieved at a treatment temperature of 450
0
C. The higher the alloy content
the thinner and harder the case since nitrides are formed near to the surface
when aluminium is present.
Ionitriding is already widely used abroad and the throughput of an instal-
lation is about three times that of a comparable orthodox gas-nitriding
plant. The process is currently being used to nitride components as large
as 14 tonnes in mass down to the tiny balls of ball-point pens. Truck engine
crankshafts and other automobile parts, as well as hot- and cold-working
tools and dies are being ionitrided.
19.44 The Advantages of Nitriding are, briefly, as follows:
(i) Since no quenching is required after nitriding, cracking or distor-