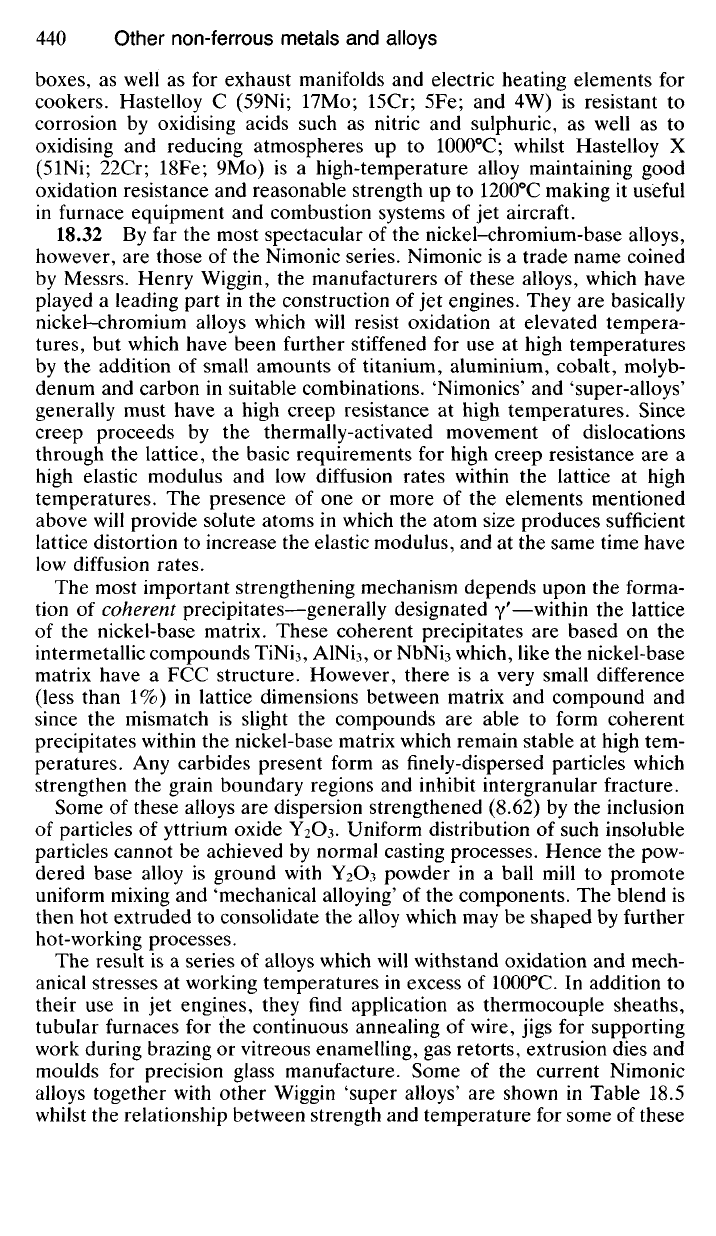
boxes,
as well as for exhaust manifolds and electric heating elements for
cookers. Hastelloy C (59Ni; 17Mo; 15Cr; 5Fe; and 4W) is resistant to
corrosion by oxidising acids such as nitric and sulphuric, as well as to
oxidising and reducing atmospheres up to 100O
0
C; whilst Hastelloy X
(51Ni; 22Cr; 18Fe; 9Mo) is a high-temperature alloy maintaining good
oxidation resistance and reasonable strength up to 1200
0
C making it useful
in furnace equipment and combustion systems of jet aircraft.
18.32 By far the most spectacular of the nickel-chromium-base alloys,
however, are those of the Nimonic series. Nimonic is a trade name coined
by Messrs. Henry Wiggin, the manufacturers of these alloys, which have
played a leading part in the construction of jet engines. They are basically
nickel-chromium alloys which will resist oxidation at elevated tempera-
tures,
but which have been further stiffened for use at high temperatures
by the addition of small amounts of titanium, aluminium, cobalt, molyb-
denum and carbon in suitable combinations. 'Nimonics' and 'super-alloys'
generally must have a high creep resistance at high temperatures. Since
creep proceeds by the thermally-activated movement of dislocations
through the lattice, the basic requirements for high creep resistance are a
high elastic modulus and low diffusion rates within the lattice at high
temperatures. The presence of one or more of the elements mentioned
above will provide solute atoms in which the atom size produces sufficient
lattice distortion to increase the elastic modulus, and at the same time have
low diffusion rates.
The most important strengthening mechanism depends upon the forma-
tion of coherent precipitates—generally designated y'—within the lattice
of the nickel-base matrix. These coherent precipitates are based on the
intermetallic compounds TiNi
3
, AlNb, or NbNi
3
which, like the nickel-base
matrix have a FCC structure. However, there is a very small difference
(less than 1%) in lattice dimensions between matrix and compound and
since the mismatch is slight the compounds are able to form coherent
precipitates within the nickel-base matrix which remain stable at high tem-
peratures. Any carbides present form as finely-dispersed particles which
strengthen the grain boundary regions and inhibit intergranular fracture.
Some of these alloys are dispersion strengthened (8.62) by the inclusion
of particles of yttrium oxide Y
2
O
3
. Uniform distribution of such insoluble
particles cannot be achieved by normal casting processes. Hence the pow-
dered base alloy is ground with Y
2
O
3
powder in a ball mill to promote
uniform mixing and 'mechanical alloying' of the components. The blend is
then hot extruded to consolidate the alloy which may be shaped by further
hot-working processes.
The result is a series of alloys which will withstand oxidation and mech-
anical stresses at working temperatures in excess of 1000
0
C. In addition to
their use in jet engines, they find application as thermocouple sheaths,
tubular furnaces for the continuous annealing of wire, jigs for supporting
work during brazing or vitreous enamelling, gas retorts, extrusion dies and
moulds for precision glass manufacture. Some of the current Nimonic
alloys together with other Wiggin 'super alloys' are shown in Table 18.5
whilst the relationship between strength and temperature for some of these