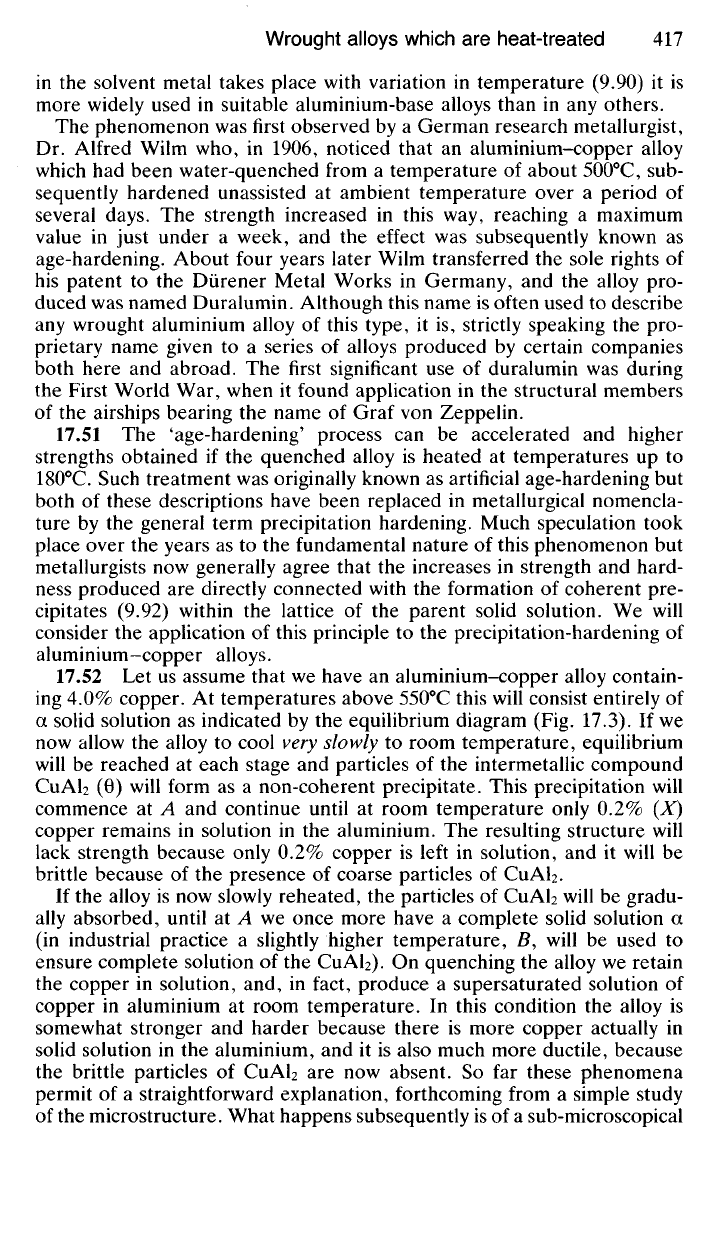
in the solvent metal takes place with variation in temperature (9.90) it is
more widely used in suitable aluminium-base alloys than in any others.
The phenomenon was first observed by a German research metallurgist,
Dr. Alfred WiIm who, in 1906, noticed that an aluminium-copper alloy
which had been water-quenched from a temperature of about 500
0
C, sub-
sequently hardened unassisted at ambient temperature over a period of
several days. The strength increased in this way, reaching a maximum
value in just under a week, and the effect was subsequently known as
age-hardening. About four years later WiIm transferred the sole rights of
his patent to the Diirener Metal Works in Germany, and the alloy pro-
duced was named Duralumin. Although this name is often used to describe
any wrought aluminium alloy of this type, it is, strictly speaking the pro-
prietary name given to a series of alloys produced by certain companies
both here and abroad. The first significant use of duralumin was during
the First World War, when it found application in the structural members
of the airships bearing the name of Graf von Zeppelin.
17.51 The 'age-hardening' process can be accelerated and higher
strengths obtained if the quenched alloy is heated at temperatures up to
180
0
C.
Such treatment was originally known as artificial age-hardening but
both of these descriptions have been replaced in metallurgical nomencla-
ture by the general term precipitation hardening. Much speculation took
place over the years as to the fundamental nature of this phenomenon but
metallurgists now generally agree that the increases in strength and hard-
ness produced are directly connected with the formation of coherent pre-
cipitates (9.92) within the lattice of the parent solid solution. We will
consider the application of this principle to the precipitation-hardening of
aluminium-copper alloys.
17.52 Let us assume that we have an aluminium-copper alloy contain-
ing 4.0% copper. At temperatures above 550
0
C this will consist entirely of
a solid solution as indicated by the equilibrium diagram (Fig. 17.3). If we
now allow the alloy to cool very slowly to room temperature, equilibrium
will be reached at each stage and particles of the intermetallic compound
CuAl
2
(0) will form as a non-coherent precipitate. This precipitation will
commence at A and continue until at room temperature only 0.2% (X)
copper remains in solution in the aluminium. The resulting structure will
lack strength because only 0.2% copper is left in solution, and it will be
brittle because of the presence of coarse particles of CuAl
2
.
If the alloy is now slowly reheated, the particles of CuAl
2
will be gradu-
ally absorbed, until at A we once more have a complete solid solution a
(in industrial practice a slightly higher temperature, B, will be used to
ensure complete solution of the CuAl
2
). On quenching the alloy we retain
the copper in solution, and, in fact, produce a supersaturated solution of
copper in aluminium at room temperature. In this condition the alloy is
somewhat stronger and harder because there is more copper actually in
solid solution in the aluminium, and it is also much more ductile, because
the brittle particles of CuAl
2
are now absent. So far these phenomena
permit of a straightforward explanation, forthcoming from a simple study
of the microstructure. What happens subsequently is of a sub-microscopical