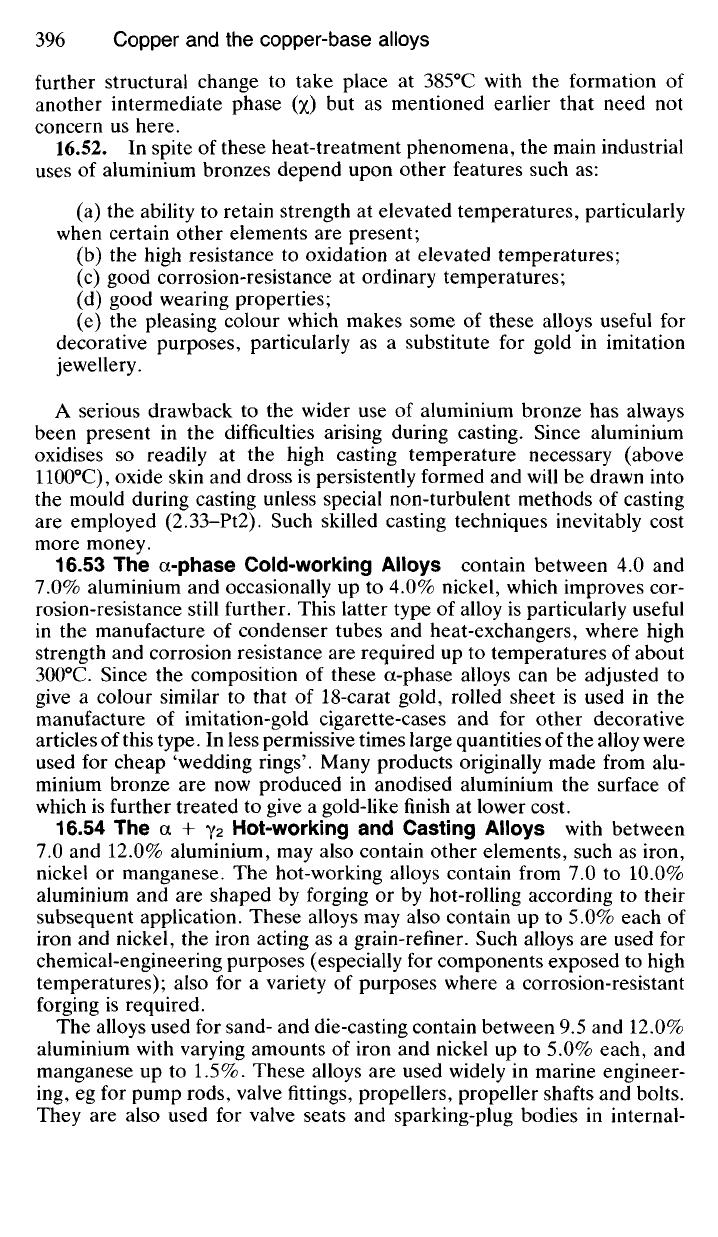
further structural change to take place at 385°C with the formation of
another intermediate phase (x) but as mentioned earlier that need not
concern us here.
16.52.
In spite of these heat-treatment phenomena, the main industrial
uses of aluminium bronzes depend upon other features such as:
(a) the ability to retain strength at elevated temperatures, particularly
when certain other elements are present;
(b) the high resistance to oxidation at elevated temperatures;
(c) good corrosion-resistance at ordinary temperatures;
(d) good wearing properties;
(e) the pleasing colour which makes some of these alloys useful for
decorative purposes, particularly as a substitute for gold in imitation
jewellery.
A serious drawback to the wider use of aluminium bronze has always
been present in the difficulties arising during casting. Since aluminium
oxidises so readily at the high casting temperature necessary (above
1100
0
C), oxide skin and dross is persistently formed and will be drawn into
the mould during casting unless special non-turbulent methods of casting
are employed (2.33-Pt2). Such skilled casting techniques inevitably cost
more money.
16.53 The ('-phase Cold-working Alloys contain between 4.0 and
7.0% aluminium and occasionally up to 4.0% nickel, which improves cor-
rosion-resistance still further. This latter type of alloy is particularly useful
in the manufacture of condenser tubes and heat-exchangers, where high
strength and corrosion resistance are required up to temperatures of about
300
0
C.
Since the composition of these a-phase alloys can be adjusted to
give a colour similar to that of 18-carat gold, rolled sheet is used in the
manufacture of imitation-gold cigarette-cases and for other decorative
articles of this type. In less permissive times large quantities of the alloy were
used for cheap 'wedding rings'. Many products originally made from alu-
minium bronze are now produced in anodised aluminium the surface of
which is further treated to give a gold-like finish at lower cost.
16.54 The a + y
2
Hot-working and Casting Alloys with between
7.0 and 12.0% aluminium, may also contain other elements, such as iron,
nickel or manganese. The hot-working alloys contain from 7.0 to 10.0%
aluminium and are shaped by forging or by hot-rolling according to their
subsequent application. These alloys may also contain up to 5.0% each of
iron and nickel, the iron acting as a grain-refiner. Such alloys are used for
chemical-engineering purposes (especially for components exposed to high
temperatures); also for a variety of purposes where a corrosion-resistant
forging is required.
The alloys used for sand- and die-casting contain between 9.5 and 12.0%
aluminium with varying amounts of iron and nickel up to 5.0% each, and
manganese up to 1.5%. These alloys are used widely in marine engineer-
ing, eg for pump rods, valve fittings, propellers, propeller shafts and bolts.
They are also used for valve seats and sparking-plug bodies in internal-