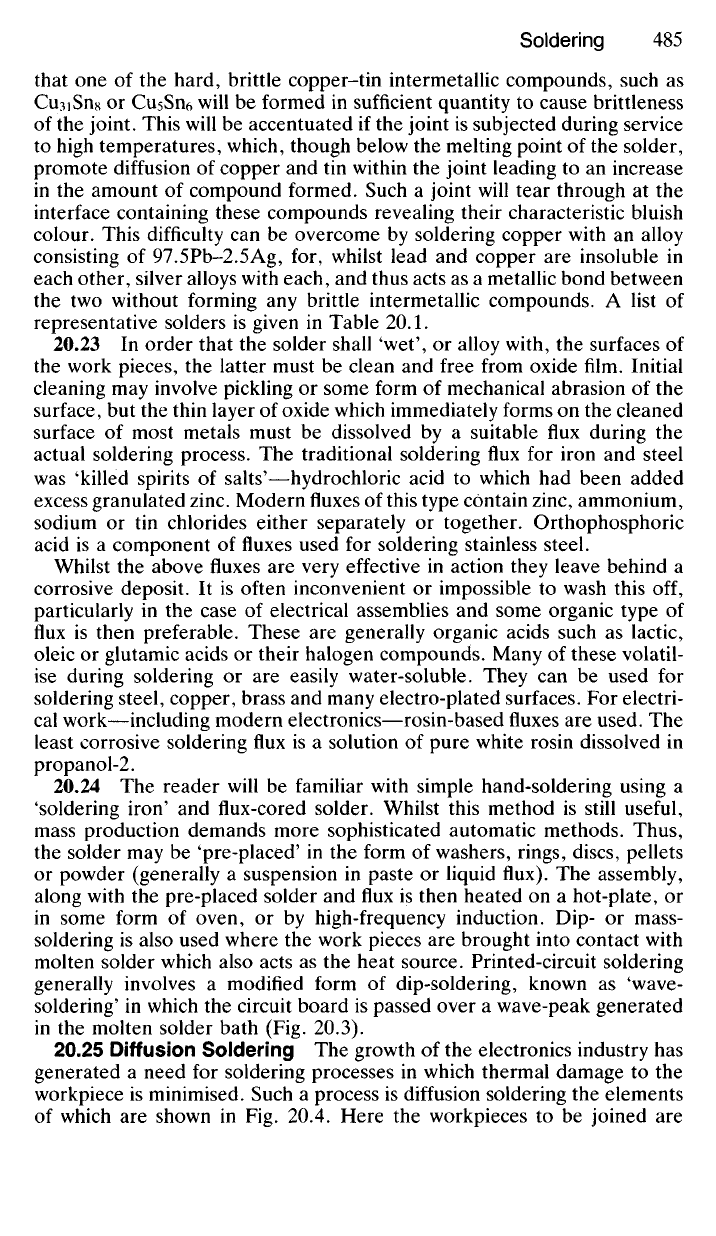
that one of the hard, brittle copper-tin intermetallic compounds, such as
CU31S118 or CusSn6 will be formed in sufficient quantity to cause brittleness
of the joint. This will be accentuated if the joint is subjected during service
to high temperatures, which, though below the melting point of the solder,
promote diffusion of copper and tin within the joint leading to an increase
in the amount of compound formed. Such a joint will tear through at the
interface containing these compounds revealing their characteristic bluish
colour. This difficulty can be overcome by soldering copper with an alloy
consisting of 97.5Pb-2.5Ag, for, whilst lead and copper are insoluble in
each other, silver alloys with each, and thus acts as a metallic bond between
the two without forming any brittle intermetallic compounds. A list of
representative solders is given in Table 20.1.
20.23 In order that the solder shall 'wet', or alloy with, the surfaces of
the work pieces, the latter must be clean and free from oxide film. Initial
cleaning may involve pickling or some form of mechanical abrasion of the
surface, but the thin layer of oxide which immediately forms on the cleaned
surface of most metals must be dissolved by a suitable flux during the
actual soldering process. The traditional soldering flux for iron and steel
was 'killed spirits of salts'—hydrochloric acid to which had been added
excess granulated zinc. Modern fluxes of this type contain zinc, ammonium,
sodium or tin chlorides either separately or together. Orthophosphoric
acid is a component of fluxes used for soldering stainless steel.
Whilst the above fluxes are very effective in action they leave behind a
corrosive deposit. It is often inconvenient or impossible to wash this off,
particularly in the case of electrical assemblies and some organic type of
flux is then preferable. These are generally organic acids such as lactic,
oleic or glutamic acids or their halogen compounds. Many of these volatil-
ise during soldering or are easily water-soluble. They can be used for
soldering steel, copper, brass and many electro-plated surfaces. For electri-
cal work—including modern electronics—rosin-based fluxes are used. The
least corrosive soldering flux is a solution of pure white rosin dissolved in
propanol-2.
20.24 The reader will be familiar with simple hand-soldering using a
'soldering iron' and flux-cored solder. Whilst this method is still useful,
mass production demands more sophisticated automatic methods. Thus,
the solder may be 'pre-placed' in the form of washers, rings, discs, pellets
or powder (generally a suspension in paste or liquid flux). The assembly,
along with the pre-placed solder and flux is then heated on a hot-plate, or
in some form of oven, or by high-frequency induction. Dip- or mass-
soldering is also used where the work pieces are brought into contact with
molten solder which also acts as the heat source. Printed-circuit soldering
generally involves a modified form of dip-soldering, known as 'wave-
soldering' in which the circuit board is passed over a wave-peak generated
in the molten solder bath (Fig. 20.3).
20.25 Diffusion Soldering The growth of the electronics industry has
generated a need for soldering processes in which thermal damage to the
workpiece is minimised. Such a process is diffusion soldering the elements
of which are shown in Fig. 20.4. Here the workpieces to be joined are