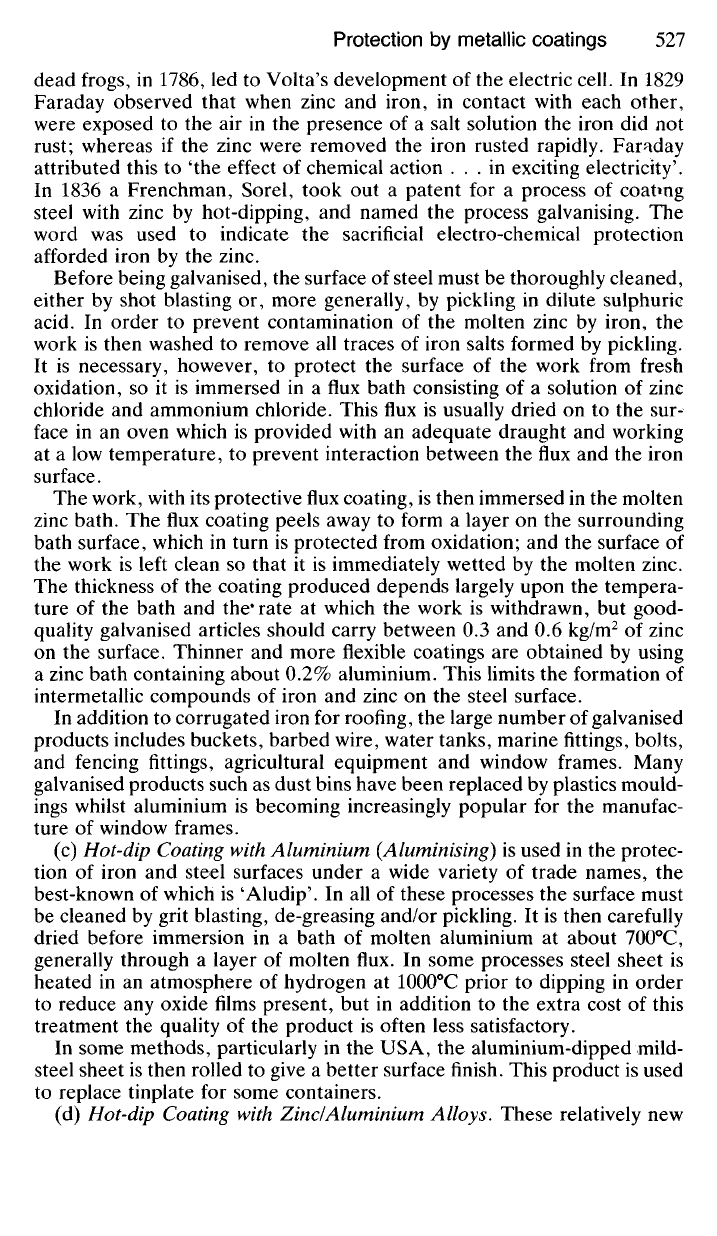
dead frogs, in 1786, led to Volta's development of the electric cell. In 1829
Faraday observed that when zinc and iron, in contact with each other,
were exposed to the air in the presence of a salt solution the iron did not
rust; whereas if the zinc were removed the iron rusted rapidly. Faraday
attributed this to 'the effect of chemical action ... in exciting electricity'.
In 1836 a Frenchman, Sorel, took out a patent for a process of coatmg
steel with zinc by hot-dipping, and named the process galvanising. The
word was used to indicate the sacrificial electro-chemical protection
afforded iron by the zinc.
Before being galvanised, the surface of steel must be thoroughly cleaned,
either by shot blasting or, more generally, by pickling in dilute sulphuric
acid. In order to prevent contamination of the molten zinc by iron, the
work is then washed to remove all traces of iron salts formed by pickling.
It is necessary, however, to protect the surface of the work from fresh
oxidation, so it is immersed in a flux bath consisting of a solution of zine
chloride and ammonium chloride. This flux is usually dried on to the sur-
face in an oven which is provided with an adequate draught and working
at a low temperature, to prevent interaction between the flux and the iron
surface.
The work, with its protective flux coating, is then immersed in the molten
zinc bath. The flux coating peels away to form a layer on the surrounding
bath surface, which in turn is protected from oxidation; and the surface of
the work is left clean so that it is immediately wetted by the molten zinc.
The thickness of the coating produced depends largely upon the tempera-
ture of the bath and the'rate at which the work is withdrawn, but good-
quality galvanised articles should carry between 0.3 and 0.6 kg/m
2
of zinc
on the surface. Thinner and more flexible coatings are obtained by using
a zinc bath containing about 0.2% aluminium. This limits the formation of
intermetallic compounds of iron and zinc on the steel surface.
In addition to corrugated iron for roofing, the large number of galvanised
products includes buckets, barbed wire, water tanks, marine fittings, bolts,
and fencing fittings, agricultural equipment and window frames. Many
galvanised products such as dust bins have been replaced by plastics mould-
ings whilst aluminium is becoming increasingly popular for the manufac-
ture of window frames.
(c) Hot-dip Coating with Aluminium (Aluminising) is used in the protec-
tion of iron and steel surfaces under a wide variety of trade names, the
best-known of which is 'Aludip'. In all of these processes the surface must
be cleaned by grit blasting, de-greasing and/or pickling. It is then carefully
dried before immersion in a bath of molten aluminium at about 700
0
C,
generally through a layer of molten flux. In some processes steel sheet is
heated in an atmosphere of hydrogen at 1000
0
C prior to dipping in order
to reduce any oxide films present, but in addition to the extra cost of this
treatment the quality of the product is often less satisfactory.
In some methods, particularly in the USA, the aluminium-dipped mild-
steel sheet is then rolled to give a better surface finish. This product is used
to replace tinplate for some containers.
(d) Hot-dip Coating with ZinclAluminium Alloys. These relatively new