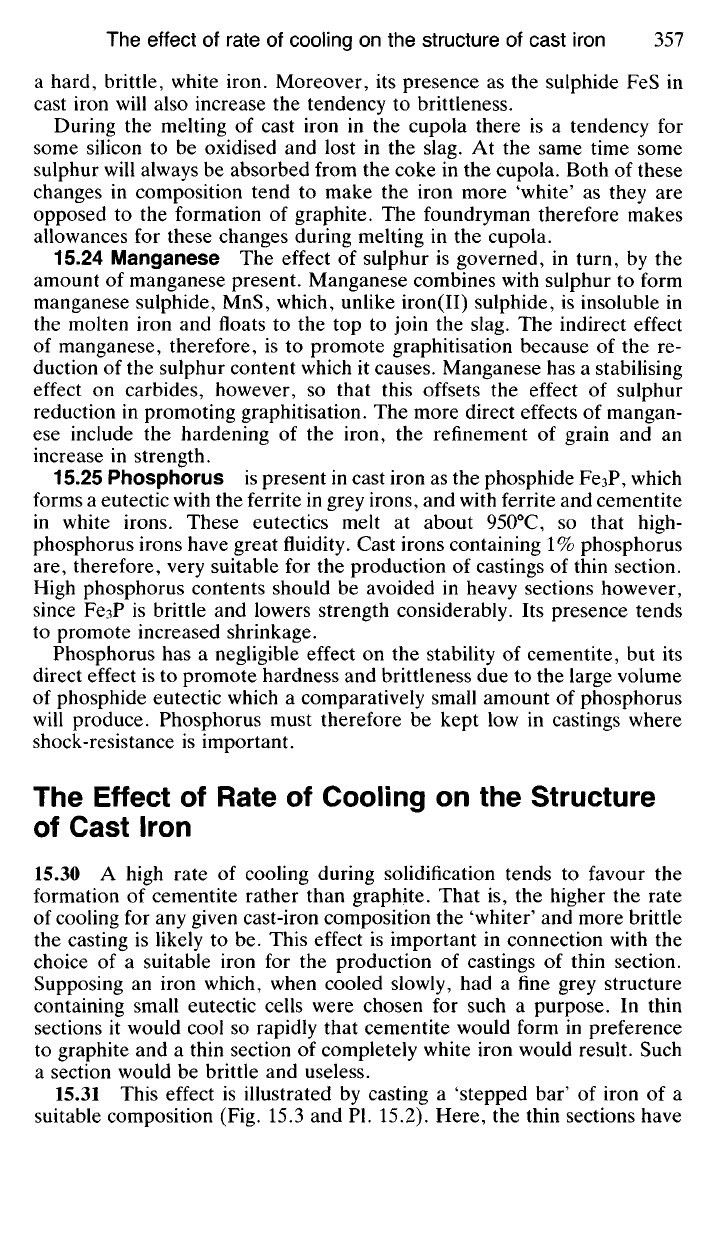
a hard, brittle, white iron. Moreover, its presence as the sulphide FeS in
cast iron will also increase the tendency to brittleness.
During the melting of cast iron in the cupola there is a tendency for
some silicon to be oxidised and lost in the slag. At the same time some
sulphur will always be absorbed from the coke in the cupola. Both of these
changes in composition tend to make the iron more 'white' as they are
opposed to the formation of graphite. The foundryman therefore makes
allowances for these changes during melting in the cupola.
15.24 Manganese The effect of sulphur is governed, in turn, by the
amount of manganese present. Manganese combines with sulphur to form
manganese sulphide, MnS, which, unlike iron(II) sulphide, is insoluble in
the molten iron and floats to the top to join the slag. The indirect effect
of manganese, therefore, is to promote graphitisation because of the re-
duction of the sulphur content which it causes. Manganese has a stabilising
effect on carbides, however, so that this offsets the effect of sulphur
reduction in promoting graphitisation. The more direct effects of mangan-
ese include the hardening of the iron, the refinement of grain and an
increase in strength.
15.25 Phosphorus is present in cast iron as the phosphide Fe
3
P, which
forms a eutectic with the ferrite in grey irons, and with ferrite and cementite
in white irons. These eutectics melt at about 950
0
C, so that high-
phosphorus irons have great fluidity. Cast irons containing 1% phosphorus
are,
therefore, very suitable for the production of castings of thin section.
High phosphorus contents should be avoided in heavy sections however,
since Fe
3
P is brittle and lowers strength considerably. Its presence tends
to promote increased shrinkage.
Phosphorus has a negligible effect on the stability of cementite, but its
direct effect is to promote hardness and brittleness due to the large volume
of phosphide eutectic which a comparatively small amount of phosphorus
will produce. Phosphorus must therefore be kept low in castings where
shock-resistance is important.
The Effect of Rate of Cooling on the Structure
of Cast Iron
15.30 A high rate of cooling during solidification tends to favour the
formation of cementite rather than graphite. That is, the higher the rate
of cooling for any given cast-iron composition the 'whiter' and more brittle
the casting is likely to be. This effect is important in connection with the
choice of a suitable iron for the production of castings of thin section.
Supposing an iron which, when cooled slowly, had a fine grey structure
containing small eutectic cells were chosen for such a purpose. In thin
sections it would cool so rapidly that cementite would form in preference
to graphite and a thin section of completely white iron would result. Such
a section would be brittle and useless.
15.31 This effect is illustrated by casting a 'stepped bar' of iron of a
suitable composition (Fig. 15.3 and Pl. 15.2). Here, the thin sections have