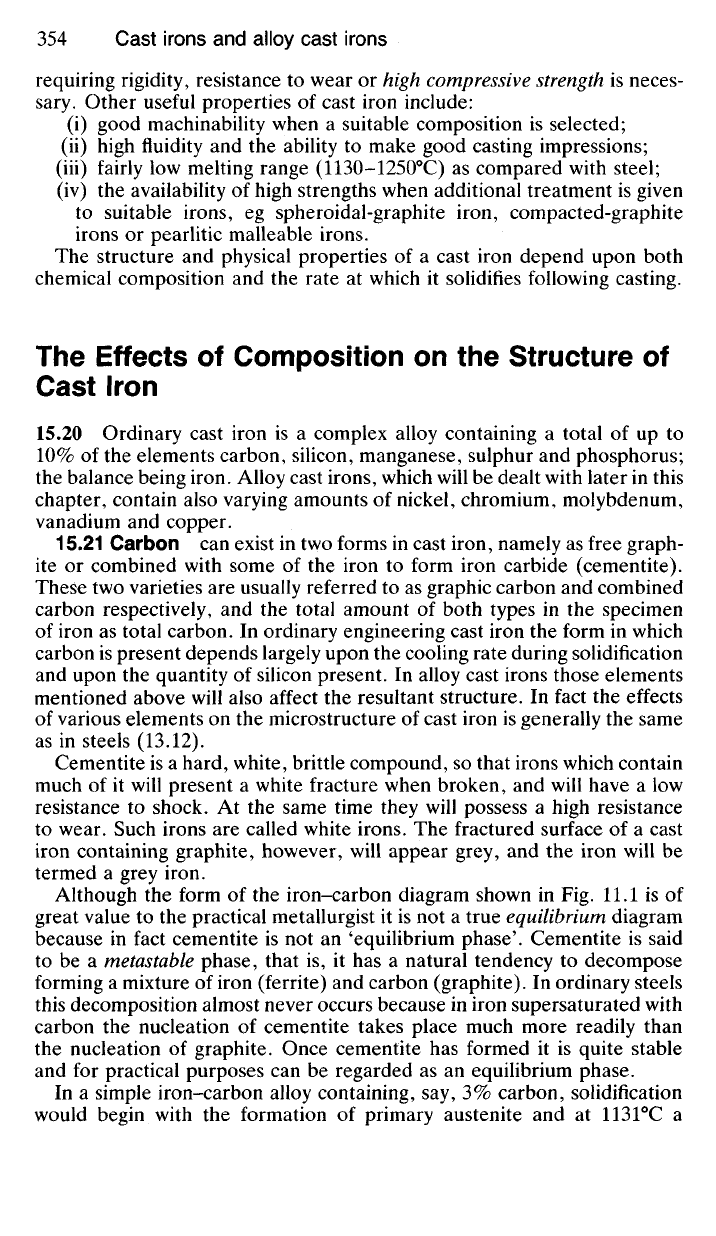
requiring rigidity, resistance to wear or high compressive strength is neces-
sary. Other useful properties of cast iron include:
(i) good machinability when a suitable composition is selected;
(ii) high fluidity and the ability to make good casting impressions;
(iii) fairly low melting range (1130-1250
0
C) as compared with steel;
(iv) the availability of high strengths when additional treatment is given
to suitable irons, eg spheroidal-graphite iron, compacted-graphite
irons or pearlitic malleable irons.
The structure and physical properties of a cast iron depend upon both
chemical composition and the rate at which it solidifies following casting.
The Effects of Composition on the Structure of
Cast Iron
15.20 Ordinary cast iron is a complex alloy containing a total of up to
10%
of the elements carbon, silicon, manganese, sulphur and phosphorus;
the balance being iron. Alloy cast irons, which will be dealt with later in this
chapter, contain also varying amounts of nickel, chromium, molybdenum,
vanadium and copper.
15.21 Carbon can exist in two forms in cast iron, namely as free graph-
ite or combined with some of the iron to form iron carbide (cementite).
These two varieties are usually referred to as graphic carbon and combined
carbon respectively, and the total amount of both types in the specimen
of iron as total carbon. In ordinary engineering cast iron the form in which
carbon is present depends largely upon the cooling rate during solidification
and upon the quantity of silicon present. In alloy cast irons those elements
mentioned above will also affect the resultant structure. In fact the effects
of various elements on the microstructure of cast iron is generally the same
as in steels (13.12).
Cementite is a hard, white, brittle compound, so that irons which contain
much of it will present a white fracture when broken, and will have a low
resistance to shock. At the same time they will possess a high resistance
to wear. Such irons are called white irons. The fractured surface of a cast
iron containing graphite, however, will appear grey, and the iron will be
termed a grey iron.
Although the form of the iron-carbon diagram shown in Fig. 11.1 is of
great value to the practical metallurgist it is not a true equilibrium diagram
because in fact cementite is not an 'equilibrium phase'. Cementite is said
to be a metastable phase, that is, it has a natural tendency to decompose
forming a mixture of iron (ferrite) and carbon (graphite). In ordinary steels
this decomposition almost never occurs because in iron supersaturated with
carbon the nucleation of cementite takes place much more readily than
the nucleation of graphite. Once cementite has formed it is quite stable
and for practical purposes can be regarded as an equilibrium phase.
In a simple iron-carbon alloy containing, say, 3% carbon, solidification
would begin with the formation of primary austenite and at 1131°C a