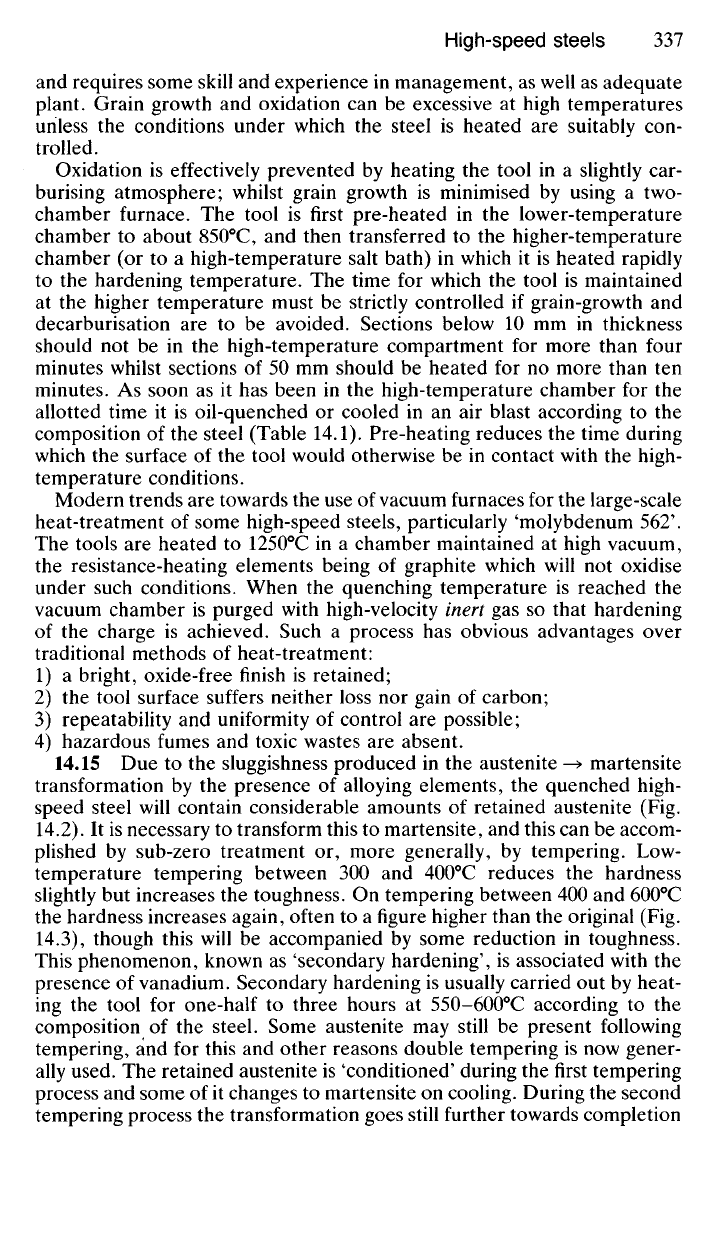
and requires some skill and experience in management, as well as adequate
plant. Grain growth and oxidation can be excessive at high temperatures
unless the conditions under which the steel is heated are suitably con-
trolled.
Oxidation is effectively prevented by heating the tool in a slightly car-
burising atmosphere; whilst grain growth is minimised by using a two-
chamber furnace. The tool is first pre-heated in the lower-temperature
chamber to about 850
0
C, and then transferred to the higher-temperature
chamber (or to a high-temperature salt bath) in which it is heated rapidly
to the hardening temperature. The time for which the tool is maintained
at the higher temperature must be strictly controlled if grain-growth and
decarburisation are to be avoided. Sections below 10 mm in thickness
should not be in the high-temperature compartment for more than four
minutes whilst sections of 50 mm should be heated for no more than ten
minutes. As soon as it has been in the high-temperature chamber for the
allotted time it is oil-quenched or cooled in an air blast according to the
composition of the steel (Table 14.1). Pre-heating reduces the time during
which the surface of the tool would otherwise be in contact with the high-
temperature conditions.
Modern trends are towards the use of vacuum furnaces for the large-scale
heat-treatment of some high-speed steels, particularly 'molybdenum 562'.
The tools are heated to 1250
0
C in a chamber maintained at high vacuum,
the resistance-heating elements being of graphite which will not oxidise
under such conditions. When the quenching temperature is reached the
vacuum chamber is purged with high-velocity inert gas so that hardening
of the charge is achieved. Such a process has obvious advantages over
traditional methods of heat-treatment:
1) a bright, oxide-free finish is retained;
2) the tool surface suffers neither loss nor gain of carbon;
3) repeatability and uniformity of control are possible;
4) hazardous fumes and toxic wastes are absent.
14.15 Due to the sluggishness produced in the austenite
—»
martensite
transformation by the presence of alloying elements, the quenched high-
speed steel will contain considerable amounts of retained austenite (Fig.
14.2).
It is necessary to transform this to martensite, and this can be accom-
plished by sub-zero treatment or, more generally, by tempering. Low-
temperature tempering between 300 and 400
0
C reduces the hardness
slightly but increases the toughness. On tempering between 400 and 600
0
C
the hardness increases again, often to a figure higher than the original (Fig.
14.3),
though this will be accompanied by some reduction in toughness.
This phenomenon, known as 'secondary hardening', is associated with the
presence of vanadium. Secondary hardening is usually carried out by heat-
ing the tool for one-half to three hours at 550-600
0
C according to the
composition of the steel. Some austenite may still be present following
tempering, and for this and other reasons double tempering is now gener-
ally used. The retained austenite is 'conditioned' during the first tempering
process and some of it changes to martensite on cooling. During the second
tempering process the transformation goes still further towards completion