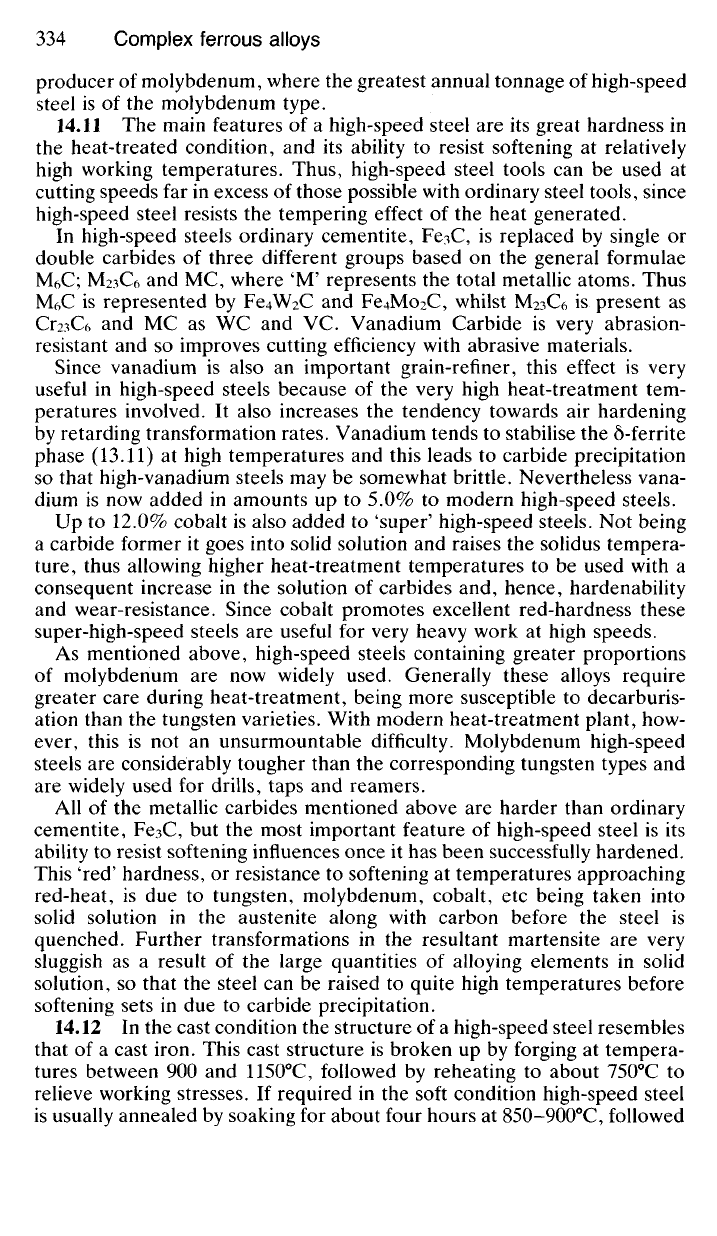
producer of molybdenum, where the greatest annual tonnage of high-speed
steel is of the molybdenum type.
14.11 The main features of a high-speed steel are its great hardness in
the heat-treated condition, and its ability to resist softening at relatively
high working temperatures. Thus, high-speed steel tools can be used at
cutting speeds far in excess of those possible with ordinary steel tools, since
high-speed steel resists the tempering effect of the heat generated.
In high-speed steels ordinary cementite, Fe
3
C, is replaced by single or
double carbides of three different groups based on the general formulae
M
6
C; M
23
C
6
and MC, where 'M' represents the total metallic atoms. Thus
M
6
C is represented by Fe
4
WiC and Fe
4
Mo
2
C, whilst M
23
C
6
is present as
O"23C
6
and MC as WC and VC. Vanadium Carbide is very abrasion-
resistant and so improves cutting efficiency with abrasive materials.
Since vanadium is also an important grain-refiner, this effect is very
useful in high-speed steels because of the very high heat-treatment tem-
peratures involved. It also increases the tendency towards air hardening
by retarding transformation rates. Vanadium tends to stabilise the 6-ferrite
phase (13.11) at high temperatures and this leads to carbide precipitation
so that high-vanadium steels may be somewhat brittle. Nevertheless vana-
dium is now added in amounts up to 5.0% to modern high-speed steels.
Up to 12.0% cobalt is also added to 'super' high-speed steels. Not being
a carbide former it goes into solid solution and raises the solidus tempera-
ture,
thus allowing higher heat-treatment temperatures to be used with a
consequent increase in the solution of carbides and, hence, hardenability
and wear-resistance. Since cobalt promotes excellent red-hardness these
super-high-speed steels are useful for very heavy work at high speeds.
As mentioned above, high-speed steels containing greater proportions
of molybdenum are now widely used. Generally these alloys require
greater care during heat-treatment, being more susceptible to decarburis-
ation than the tungsten varieties. With modern heat-treatment plant, how-
ever, this is not an unsurmountable difficulty. Molybdenum high-speed
steels are considerably tougher than the corresponding tungsten types and
are widely used for drills, taps and reamers.
All of the metallic carbides mentioned above are harder than ordinary
cementite, Fe
3
C, but the most important feature of high-speed steel is its
ability to resist softening influences once it has been successfully hardened.
This 'red' hardness, or resistance to softening at temperatures approaching
red-heat, is due to tungsten, molybdenum, cobalt, etc being taken into
solid solution in the austenite along with carbon before the steel is
quenched. Further transformations in the resultant martensite are very
sluggish as a result of the large quantities of alloying elements in solid
solution, so that the steel can be raised to quite high temperatures before
softening sets in due to carbide precipitation.
14.12 In the cast condition the structure of a high-speed steel resembles
that of a cast iron. This cast structure is broken up by forging at tempera-
tures between 900 and 1150
0
C, followed by reheating to about 750
0
C to
relieve working stresses. If required in the soft condition high-speed steel
is usually annealed by soaking for about four hours at 850-900
0
C, followed