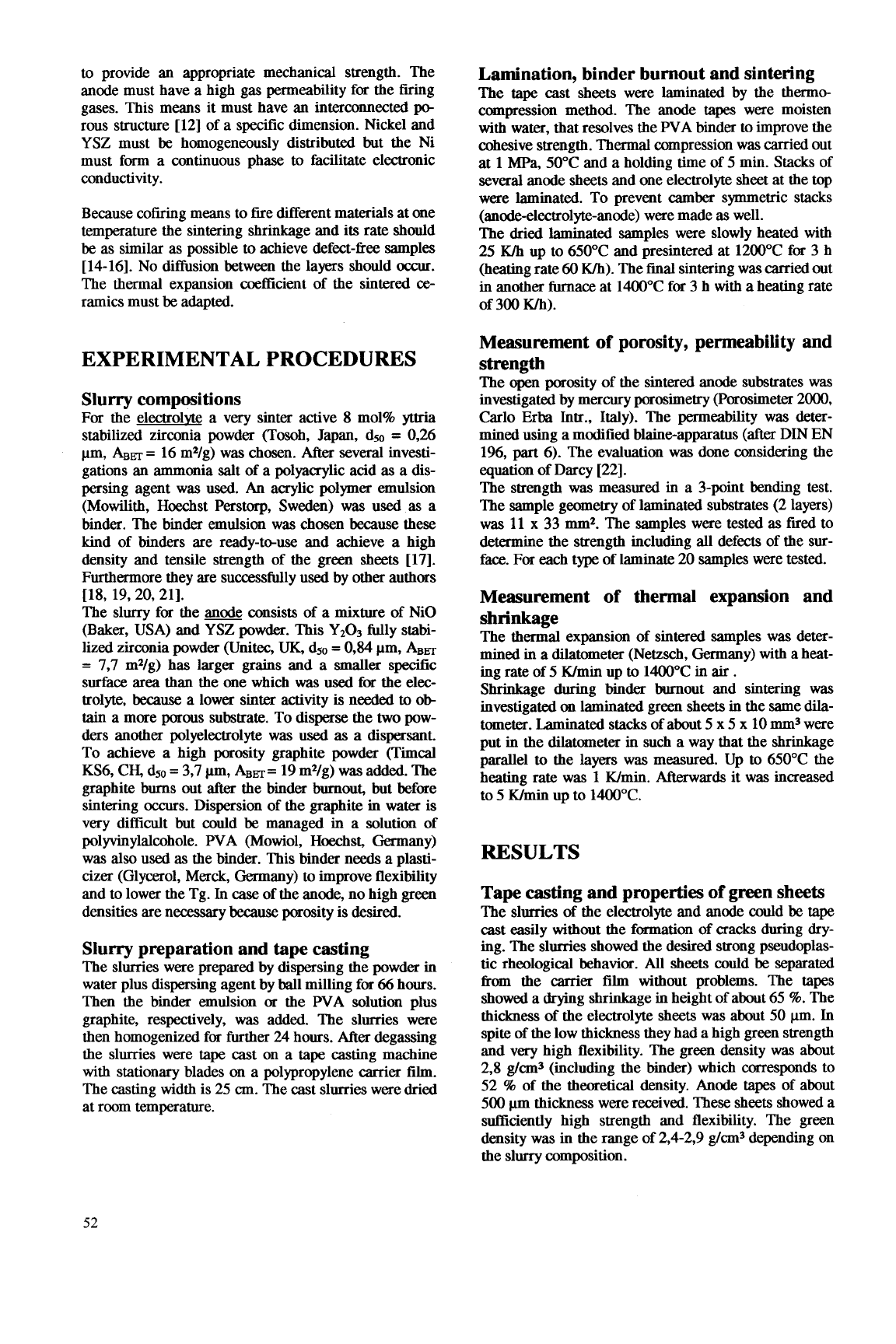
to provide an appropriate mechanical strength. The
anode must have a high gas permeability for the firing
gases. This means it must have an interconnected
PO-
rous structure
[12]
of a specific dimension. Nickel and
YSZ
must be homogeneously distributed but the Ni
must form a continuous phase to facilitate electronic
conductivity.
Because cofiring means to fire different materials at one
temperature the sintering shrinkage and its rate should
be
as similar as possible to achieve defect-free samples
[14-161.
No diffusion between the layers should
occuf.
The thermal expansion coefficient of the sintered ce-
ramics must
be
adapted.
EXPERIMENTAL PROCEDURES
Slurry compositions
For the electrolyte a very sinter active
8
molI
yttria
stabilized zirconia powder (Tosoh, Japan, dso
=
0,26
pm, ABm
=
16
m2/g) was chosen.
After
several investi-
gations an ammonia salt of a polyacrylic acid
as
a dis-
persing agent was
used.
An acrylic polymer emulsion
(Mowilith, Hoechst Perstorp, Sweden) was used
as
a
binder. The binder emulsion was chosen because these
kind of binders are ready-to-use and achieve a high
density and tensile strength of the green sheets
[17].
Furthermore they are successfully used by other authors
[18, 19,20,21].
The slurry for the anode consists of a mixture of NiO
(Baker,
USA)
and
YSZ
powder. This
Y203
fully stabi-
lized zirconia powder (Unitec,
UK,
d50
=
0,84
pm, ABET
=
7,7
m2/g)
has
larger
grains
and a smaller specific
surface area than the one which
was
used
for the elec-
trolyte,
because
a lower sinter activity is needed to
ob
tain
a more
porous
substrate. To disperse the two
pow-
ders another polyelectrolyte
was
used
as
a dispersant.
To
achieve a high porosity graphite powder (Timcal
KS6, CH,
d50
=
3,7
pm,
ABET
=
19
m2/g)
was
added. The
graphite burns out
after
the binder
burnout,
but before
sintering
occuzs.
Dispersion of the graphite in water is
very difficult but could
be
managed in a solution of
polyvinylalcohole. PVA (Mowiol, Hoechst, Germany)
was also used
as
the binder. This binder needs a plasti-
cizer (Glycerol, Merck, Germany) to improve flexibility
and to lower the Tg.
In
case
of the anode, no high green
densities are necessary
because
porosity is desired.
Slurry preparation and tape casting
The slurries were prepared by dispersing the powder in
water plus dispersing agent by ball milling for
66
hours.
Then the binder emulsion
or
the PVA solution plus
graphite, respectively, was added. The slurries were
then homogenized for further
24
hours. After degassing
the slurries were tape cast on a
tape
casting machine
with stationary blades on a polypropylene carrier film.
The casting width is
25
cm.
The cast slurries were dried
at room temperature.
Lamination, binder burnout and sintering
The tape cast sheets were laminated by the thermo-
cumpression method. The anode tapes were moisten
with water, that resolves the PVA binder to improve the
cohesive strength. Thermal compression was carried out
at
1
MPa,
50°C
and a holding time of
5
min. Stacks
of
several anode
sheets
and one electrolyte sheet at the top
were laminated.
To
prevent
camber
symmetric stacks
(anode-electrolyte-anode)
were made
as
well.
The dried
laminated
samples were slowly heated with
25
Kh
up to
650°C
and presintered at
1200°C
for 3
h
(heating rate
60
Kh).
The final sintering was carried out
in another furnace at
1400°C
for
3
h
with a heating rate
of
300
Kh).
Measurement
of
porosity, permeability and
strength
The open porosity of the sintered anode substrates was
investigated by mercury porosimetry (Porosimeter
2000,
Car10
Erba Intr., Italy). The permeability was deter-
mined using a modified blaine-apparatus (after DIN EN
196,
part
6).
The evaluation was done considering the
equation
of Darcy
[22].
The strength was measured in a 3-point bending test.
The sample geometry of laminated substrates
(2
layers)
was
11
x
33
mm*.
The samples were tested
as
fned
to
determine the strength including all defects of the sur-
face.
For
each
type of laminate
20
samples were tested.
Measurement
of
thermal expansion and
shrinkage
The thermal expansion of sintered samples was deter-
mined in a dilatometer (Netzsch, Germany) with a heat-
ing rate of
5
Wmin up to
1400°C
in
air.
Shrinkage during binder burnout and sintering was
investigated
on
laminated green sheets in the same dila-
tometer. Laminated stacks of about
5
x
5
x
10
1111113
were
put in the dilatometer in such a way that the shrinkage
parallel to the layers was measured. Up
to
650°C
the
heating rate was
1
Wmin.
Afterwards
it was increased
to
5
Wmin up to
1400°C.
RESULTS
Tape casting and properties
of
green sheets
The slurries
of
the electrolyte and anode could be tape
cast easily without the formation of cracks during dry-
ing. The slurries showed the desired strong pseudoplas-
tic
rheological behavior.
AU
sheets could be separated
fiom
the carrier film without problems. The tapes
showed a drying shrinkage in height of about
65
%.
The
thickness of the electrolyte
sheets
was about
50
pm.
In
spite of the low thickness they had a high green strength
and very high flexibility. The green density was about
2,8
g/cm3
(including the binder) which corresponds to
52
%
of the theoretical density. Anode tapes of about
500
pm
thickness were received. These
sheets
showed a
sufficiently high strength and flexibility. The green
density was in the range
of
2,4-2,9
g/cm3 depending on
the slurry composition.
52