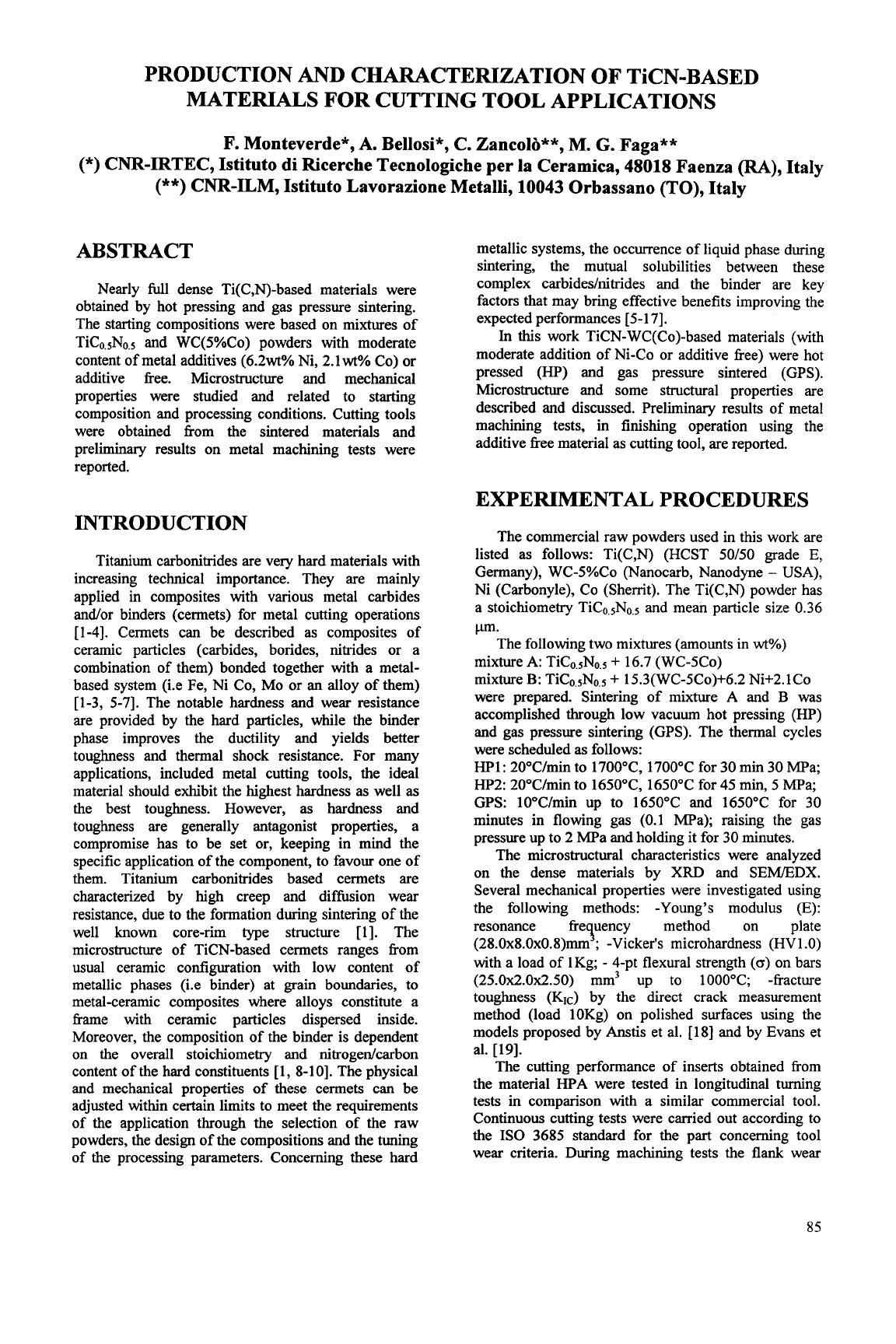
PRODUCTION AND CHARACTERIZATION OF TiCN-BASED
MATERIALS FOR CUTTING TOOL APPLICATIONS
F. Monteverde*,
A.
Bellosi*, C. Zancolij**, M.
G.
Faga**
(*)
CNR-IRTEC, Istituto di Ricerche Tecnologiche per la Cerarnica,
48018
Faenza
(RA),
Italy
(**)
CNR-ILM, Istituto Lavorazione Metalli, 10043 Orbassano
(TO),
Italy
ABSTRACT
Nearly full dense Ti(C,N)-based materials were
obtained by hot pressing and gas pressure sintering.
The starting compositions were based on mixtures of
TiCo.5No.5 and WC(S%Co) powders with moderate
content of metal additives (6.2wt% Ni, 2.lwt% Co) or
additive fiee. Microstructure and mechanical
properties were studied and related to starting
composition and processing conditions. Cutting tools
were obtained fiom the sintered materials and
preliminary results on metal machining tests were
reported.
INTRODUCTION
Titanium carbonitrides are very hard materials with
increasing technical importance. They are mainly
applied in composites with various metal carbides
and/or binders (cermets) for metal cutting operations
[I-41. Cermets can be described as composites
of
ceramic particles (carbides, borides, nitrides or a
combination of them) bonded together with a metal-
based system (i.e Fey Ni Co, Mo or an alloy
of them)
[l-3, 5-71. The notable hardness and wear resistance
are provided by the hard particles, while the binder
phase improves the ductility and yields better
toughness and thermal shock resistance. For many
applications, included metal cutting tools, the ideal
material should exhibit the highest hardness as well
as
the best toughness. However, as hardness and
toughness are generally antagonist properties, a
compromise has to be set or, keeping in mind the
specific application of the component, to favour one of
them. Titanium carbonitrides based cermets are
characterized by high creep and difhsion wear
resistance, due to the formation during sintering of the
well
known core-rim type structure
[l].
The
microstructure of TiCN-based cermets ranges fiom
usual ceramic configuration with low content of
metallic phases (i.e binder) at grain boundaries, to
metal-ceramic composites where alloys constitute a
frame with ceramic particles dispersed inside.
Moreover, the composition of the binder is dependent
on the overall stoichiometry and nitrogedcarbon
content of the hard constituents [l, 8-10]. The physical
and mechanical properties of these cermets can be
adjusted within certain limits to meet the requirements
of the application through the selection
of the raw
powders, the design of the compositions and the tuning
of the processing parameters. Concerning these hard
metallic systems, the occurrence of liquid phase during
sintering, the mutual solubilities between these
complex carbideslnitrides and the binder are key
factors that may bring effective benefits improving the
expected performances [5-171.
In
this
work TiCN-WC(Co)-based materials (with
moderate addition of Ni-Co or additive fiee) were hot
pressed
(HP) and gas pressure sintered (GPS).
Microstructure and some structural properties are
described and discussed. Preliminary results of metal
machining tests, in finishing operation using the
additive fiee material as cutting tool, are reported.
EXPERIMENTAL PROCEDURES
The commercial raw powders used in this work are
listed as follows: Ti(C,N) (HCST
50/50
grade E,
Germany), WC-S%Co (Nanocarb, Nanodyne
-
USA),
Ni (Carbonyle), Co (Sherrit). The Ti(C,N) powder has
a stoichiometry TiCo.sNo.5 and mean particle size 0.36
w*
The following two mixtures (amounts in
wt%)
mixture
A:
TiCo.5No.5
+
16.7 (WC-5Co)
mixture
B:
TiCo.5No.5
+
15.3(WC-5Co)+6.2 Ni+2.lCo
were prepared. Sintering of mixture A and
B was
accomplished through low vacuum hot pressing
(HP)
and gas pressure sintering (GPS). The thermal cycles
were scheduled as follows:
HP1: 20"C/min to 1700"C, 1700°C for 30 min 30 MPa;
HP2: 20"C/min to 1650"C, 1650°C for 45 min,
5
MPa;
GPS: 10"C/min up to 1650°C and 1650°C for 30
minutes in flowing gas (0.1
ma); raising the gas
pressure up to 2 MPa and holding it for 30 minutes.
The microstructural characteristics were analyzed
on the dense materials by XRD and SEM/EDX.
Several mechanical properties were investigated using
the following methods: -Young's modulus
(E):
resonance fie uency method on plate
(28.0x8.0x0.8)mm
;
-Vicker's microhardness (HV1
.O)
with a load of 1Kg;
-
4-pt flexural strength
(0)
on bars
(25.0~2.0~2.50)
mm3
up to 1000°C; -fracture
toughness
(Klc)
by the direct crack measurement
method (load 10Kg) on polished surfaces using the
models proposed by Anstis et al.
[
181 and by Evans et
al. [19].
The cutting performance
of
inserts obtained fiom
the material
HPA
were tested
in
longitudinal turning
tests in comparison with a similar commercial tool.
Continuous cutting tests were carried out according to
the
IS0
3685 standard for the part concerning tool
wear criteria. During machining tests the flank wear
9
85