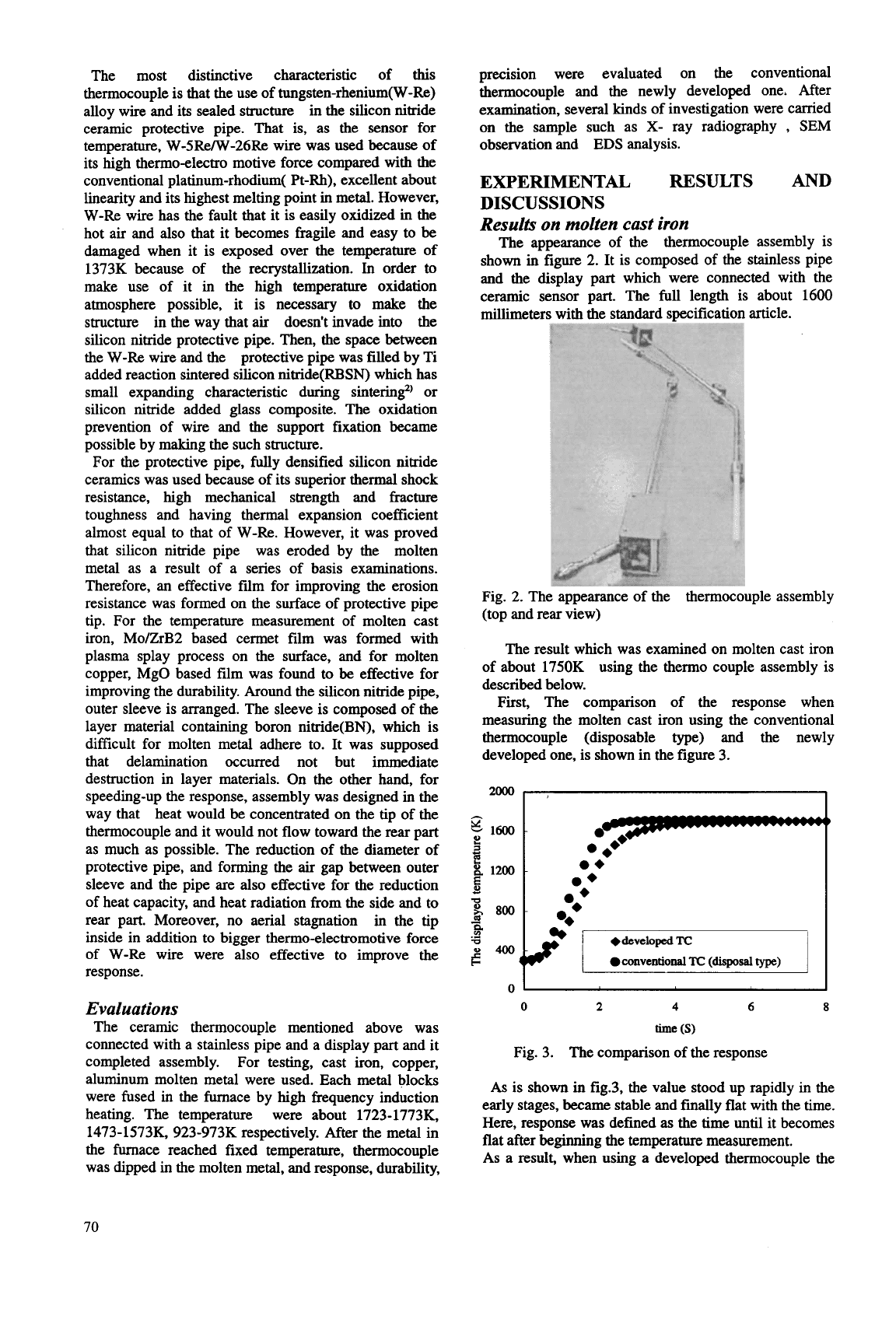
The most distinctive characteristic of
this
thermocouple is that the use of tungsten-rhenium(W-Re)
alloy wire and its sealed structure in the silicon nitride
ceramic protective pipe. That is, as the sensor for
temperature,
W-5Rem-26Re
wire was used because of
its high thermoelectro motive force compared with the
conventional platinum-rhodium( Pt-Rh), excellent about
linearity and its highest melting point in metal. However,
W-Re
wire has the fault that it is easily oxidized in the
hot air and also that it becomes fragile and easy to
be
damaged when it is exposed over the temperature of
1373K
because
of
the recrystallization.
In
order to
make use of it in the high temperature oxidation
atmosphere possible, it is necessary to make the
structure in the way that air doesn't invade into the
silicon nitride protective pipe. Then, the space between
the
W-Re
wire and the protective pipe was filled by Ti
added reaction sintered silicon nitride(RBSN) which has
small expanding characteristic during sintering2) or
silicon nitride added glass composite. The oxidation
prevention of wire and the support fixation became
possible by making the such structure.
For the protective pipe, fully densified silicon nitride
ceramics was used because of its superior thermal shock
resistance, high mechanical strength and fracture
toughness and having thermal expansion coefficient
almost equal to that of
W-Re.
However, it was proved
that silicon nitride pipe was eroded by the molten
metal as a result of a series of basis examinations.
Therefore, an effective film for improving the erosion
resistance was formed on the surface of protective pipe
tip. For the temperature measurement of molten cast
iron, Mo/ZrB2 based cermet film was formed with
plasma splay process on the surface, and for molten
copper, MgO based film was found to
be
effective for
improving the durability. Around the silicon nitride pipe,
outer sleeve is arranged. The sleeve is composed of the
layer material containing boron nitride(BN), which is
difficult for molten metal adhere to. It was supposed
that delamination occurred not but immediate
destruction in layer materials. On the other hand, for
speeding-up the response, assembly was designed
in the
way that heat would be concentrated on the tip of the
thermocouple and it would not flow toward the rear part
as much as possible. The reduction of the diameter of
protective pipe, and forming the
air
gap between outer
sleeve and the pipe are also effective for the reduction
of heat capacity, and heat radiation from the side and to
rear part. Moreover,
no
aerial stagnation
in
the tip
inside in addition to bigger thermo-electromotive force
of W-Re wire were also effective to improve
the
response.
Evaluations
The ceramic thermocouple mentioned above was
connected with a stainless pipe and a display part and it
completed assembly. For testing, cast iron, copper,
aluminum molten metal were used. Each metal blocks
were fused in the furnace by high frequency induction
heating. The temperature were about
1723-1773K,
1473-1573K, 923-973K
respectively. After the metal in
the furnace reached fixed temperature, thermocouple
was dipped
in
the molten metal, and response, durability,
precision were evaluated on the conventional
thermocouple and the newly developed one, After
examination, several kinds of investigation were carried
on the sample such as
X-
ray radiography
,
SEM
observation and
EDS
analysis.
EXPERIMENTAL RESULTS AND
DISCUSSIONS
Results on molten cast iron
The appearance of the thermocouple assembly is
shown in
figure
2. It is composed of the stainless pipe
and the display part which were connected with the
ceramic sensor part. The
full
length is about
1600
millimeters with the standard specification article.
Fig.
2.
The appearance of the thermocouple assembly
(top and rear view)
The result which was examined on molten cast iron
of about
1750K
using the thermo couple assembly is
described below.
First, The comparison of the response when
measuring the molten cast iron using the conventional
thermocouple (disposable type) and the newly
developed one, is shown in the figure
3.
I
0+
t
.+
I
+developed
TC
conventiod
TC
(disposal
type)
1
I
1
1
0
2
4
6
8
time
(S)
Fig.
3.
The comparison of the response
As
is shown in fig.3, the value stood up rapidly
in
the
early stages, became stable and finally flat with the time.
Here, response was defined as the time until it becomes
flat after beginning the temperature measurement.
As
a result, when using a developed thermocouple the
70