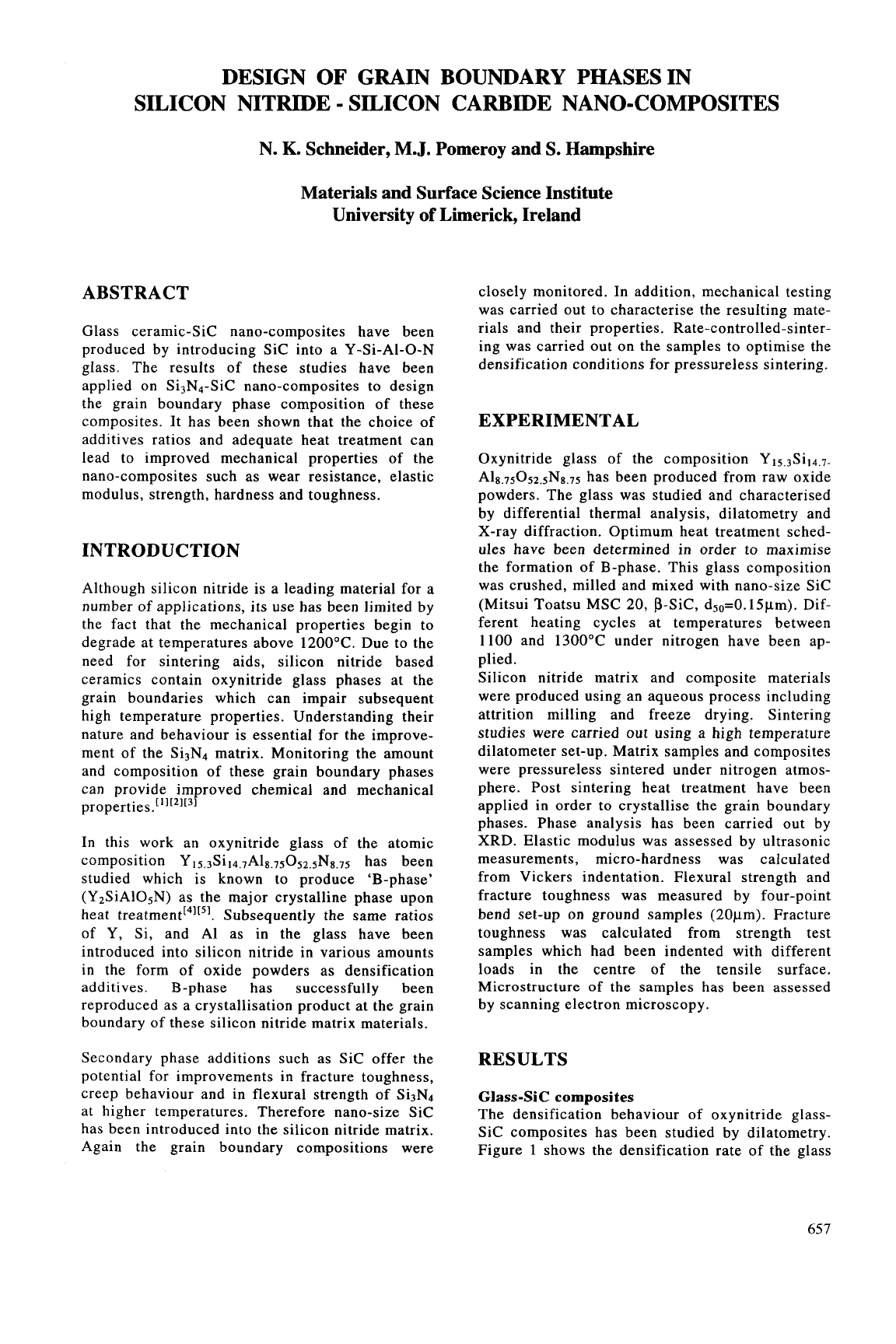
DESIGN
OF
GRAIN BOUNDARY PHASES IN
SILICON NITRIDE
-
SILICON CARBIDE NANO-COMPOSITES
N.
K.
Schneider, M.J. Pomeroy and
S.
Hampshire
Materials and Surface Science Institute
University
of
Limerick, Ireland
ABSTRACT
Glass ceramic-Sic nano-composites have been
produced by introducing Sic into a Y-Si-AI-0-N
glass. The results of these studies have been
applied on Si3N4-SiC nano-composites to design
the grain boundary phase composition of these
composites. It has been shown that the choice of
additives ratios and adequate heat treatment can
lead to improved mechanical properties of the
nano-composites such as wear resistance, elastic
modulus, strength, hardness and toughness.
INTRODUCTION
Although silicon nitride is a leading material for a
number of applications, its use has been limited by
the fact that the mechanical properties begin to
degrade at temperatures above 1200°C. Due to the
need for sintering aids, silicon nitride based
ceramics contain oxynitride glass phases at the
grain boundaries which can impair subsequent
high temperature properties. Understanding their
nature and behaviour is essential for the improve-
ment of the Si3N4 matrix. Monitoring the amount
and composition of these grain boundary phases
can provide improved chemical and mechanical
propertie~.['l[~1[~1
In this work an oxynitride glass of the atomic
composition
Y15.3Si,4.7Als.75052.~Ns.75
has been
studied which is known to produce 'B-phase'
(Y2SiAI05N) as the major crystalline phase upon
heat Subsequently the same ratios
of Y, Si, and A1 as in the glass have been
introduced into silicon nitride in various amounts
in
the form of oxide powders as densification
additives. B-phase has successfully been
reproduced as a crystallisation product at the grain
boundary of these silicon nitride matrix materials.
Secondary phase additions such as Sic offer the
potential for improvements in fracture toughness,
creep behaviour and in flexural strength of Si3N4
at higher temperatures. Therefore nano-size Sic
has been introduced into the silicon nitride matrix.
Again the grain boundary compositions were
closely monitored. In addition, mechanical testing
was carried out to characterise the resulting mate-
rials and their properties. Rate-controlled-sinter-
ing was carried out on the samples to optimise the
densification conditions for pressureless sintering.
EXPERIMENTAL
Oxynitride glass of the composition Y1~.~Si14.7-
A18.75052.5Ns.75 has been produced from raw oxide
powders. The glass was studied and characterised
by differential thermal analysis, dilatometry and
X-ray diffraction. Optimum heat treatment sched-
ules have been determined in order to maximise
the formation of B-phase. This glass composition
was crushed, milled and mixed with nano-size Sic
(Mitsui Toatsu MSC 20, p-Sic, d50=0.15pm). Dif-
ferent heating cycles at temperatures between
1100 and 1300°C under nitrogen have been ap-
plied.
Silicon nitride matrix and composite materials
were produced using an aqueous process including
attrition milling and freeze drying. Sintering
studies were carried out using a high temperature
dilatometer set-up. Matrix samples and composites
were pressureless sintered under nitrogen atmos-
phere. Post sintering heat treatment have been
applied in order to crystallise the grain boundary
phases. Phase analysis has been carried out by
XRD. Elastic modulus was assessed by ultrasonic
measurements, micro-hardness was calculated
from Vickers indentation. Flexural strength and
fracture toughness was measured by four-point
bend set-up on ground samples (20~m). Fracture
toughness was calculated from strength test
samples which had been indented with different
loads in the centre of the tensile surface.
Microstructure
of
the samples has been assessed
by scanning electron microscopy.
RESULTS
Glass-Sic
composites
The densification behaviour of oxynitride glass-
Sic composites has been studied by dilatometry.
Figure
1
shows the densification rate of the glass
657