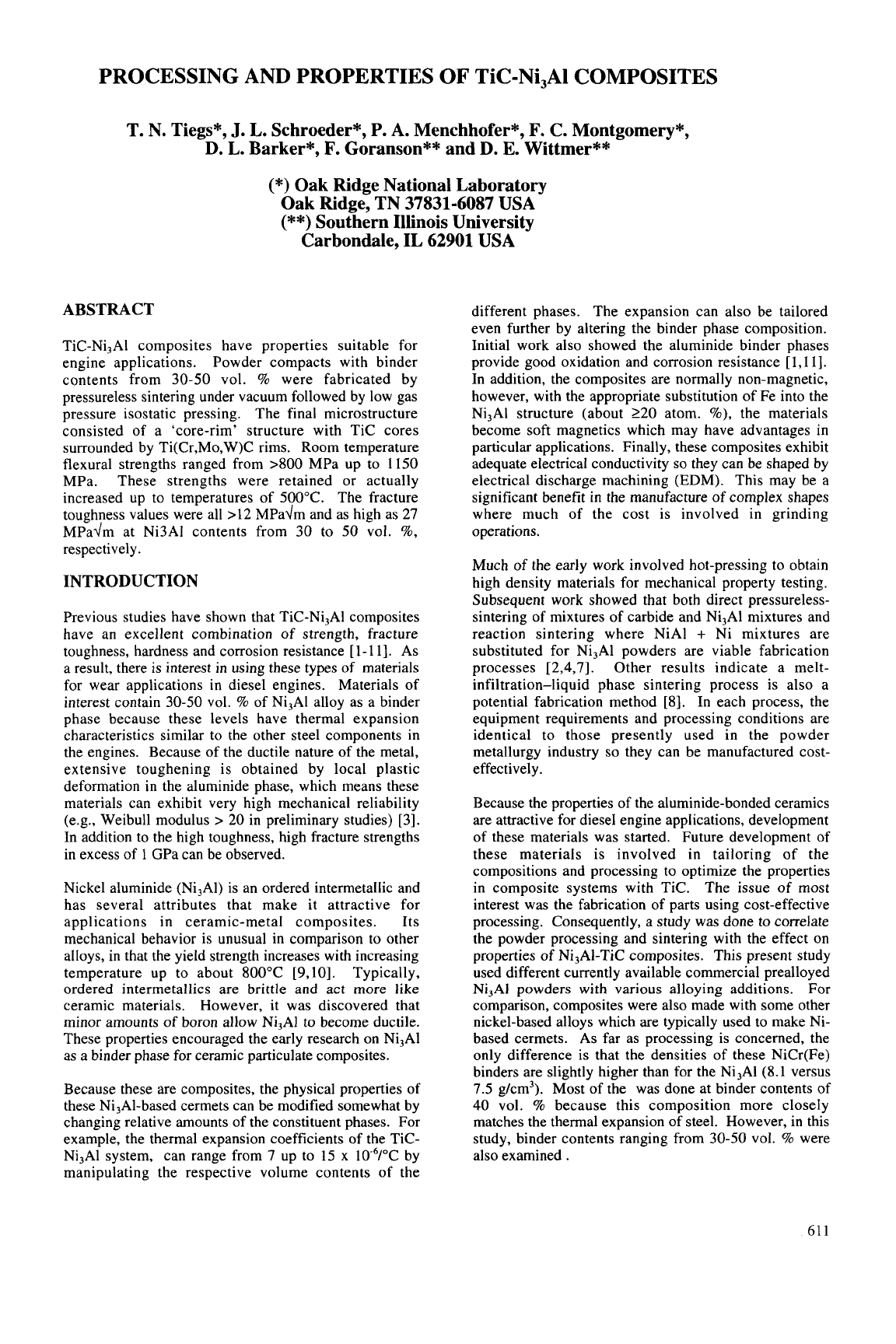
PROCESSING AND PROPERTIES
OF
Tic-Ni,Al COMPOSITES
T.
N.
Tiegs*,
J.
L.
Schroeder",
P.
A.
Menchhofer",
F.
C.
Montgomery*,
D.
L. Barker*,
F.
Goranson** and
D.
E.
Wittmer**
(*)
Oak Ridge National Laboratory
Oak Ridge, TN 37831-6087
USA
(**)
Southern Illinois University
Carbondale, IL 62901
USA
ABSTRACT
Tic-Ni,AI composites have properties suitable for
engine applications. Powder compacts with binder
contents from 30-50 vol.
%
were fabricated by
pressureless sintering under vacuum followed by low gas
pressure isostatic pressing. The final microstructure
consisted of a 'core-rim' structure with Tic cores
surrounded by Ti(Cr,Mo,W)C rims. Room temperature
flexural strengths ranged from
SO0
MPa up to 1150
MPa. These strengths were retained or actually
increased up to temperatures of 500°C. The fracture
toughness values were all >12 MPadm and as high as 27
MPadm at Ni3Al contents from 30 to
50
vol.
%,
respectively.
INTRODUCTION
Previous studies have shown that Tic-Ni,AI composites
have an excellent combination of strength, fracture
toughness, hardness and corrosion resistance
[
1-1
11.
As
a result, there is interest
in
using these types of materials
for wear applications
in
diesel engines. Materials of
interest contain 30-50 vol.
%
of Ni,Al alloy as a binder
phase because these levels have thermal expansion
characteristics similar to the other steel components
in
the engines. Because of the ductile nature of the metal,
extensive toughening is obtained by local plastic
deformation
in
the aluminide phase, which means these
materials can exhibit very high mechanical reliability
(e.g., Weibull modulus
>
20 in preliminary studies) [3].
In addition to the high toughness, high fracture strengths
in
excess of
1
GPa can be observed.
Nickel aluminide (Ni,Al) is an ordered intermetallic and
has several attributes that make it attractive for
applications in ceramic-metal composites. Its
mechanical behavior is unusual in comparison to other
alloys, in that the yield strength increases with increasing
temperature up to about 800°C
[9,10].
Typically,
ordered intermetallics are brittle and act more like
ceramic materials. However, it was discovered that
minor amounts of boron allow Ni,Al to become ductile.
These properties encouraged the early research on Ni,Al
as
a binder phase for ceramic particulate composites.
Because these are composites, the physical properties of
these Ni,Al-based cermets can be modified somewhat by
changing relative amounts of the constituent phases. For
example, the thermal expansion coefficients of the TiC-
Ni,Al system, can range from
7
up to
15
x 10-6/oC by
manipulating the respective volume contents of the
different phases. The expansion can also be tailored
even further by altering the binder phase composition.
Initial work also showed the aluminide binder phases
provide good oxidation and corrosion resistance
[1,11].
In addition, the composites are normally non-magnetic,
however, with the appropriate substitution of
Fe
into the
Ni,AI structure (about 220 atom.
%),
the materials
become soft magnetics which may have advantages in
particular applications. Finally, these composites exhibit
adequate electrical conductivity
so
they can be shaped by
electrical discharge machining (EDM). This may be a
significant benefit
in
the manufacture of complex shapes
where much of the cost is involved in grinding
operations.
Much of the early work involved hot-pressing to obtain
high density materials for mechanical property testing.
Subsequent work showed that both direct pressureless-
sintering of mixtures of carbide and Ni,Al mixtures and
reaction sintering where NiAl
+
Ni mixtures are
substituted for Ni,Al powders are viable fabrication
processes [2,4,7]. Other results indicate a melt-
infiltration-liquid phase sintering process is also a
potential fabrication method
[8].
In each process, the
equipment requirements and processing conditions are
identical to those presently used in the powder
metallurgy industry
so
they can be manufactured cost-
effectively.
Because the properties of the aluminide-bonded ceramics
are attractive for diesel engine applications, development
of these materials was started. Future development of
these materials is involved in tailoring of the
compositions and processing to optimize the properties
in composite systems with Tic. The issue of most
interest was the fabrication of parts using cost-effective
processing. Consequently, a study was done to correlate
the powder processing and sintering with the effect on
properties of Ni,Al-Tic composites. This present study
used different currently available commercial prealloyed
Ni,AI powders with various alloying additions. For
comparison, composites were also made with some other
nickel-based alloys which are typically used to make Ni-
based cermets. As far as processing is concerned, the
only difference is that the densities of these NiCr(Fe)
binders are slightly higher than for the Ni,AI (8.1 versus
7.5 g/cm3). Most of the was done at binder contents of
40 vol.
%
because this composition more closely
matches the thermal expansion of steel. However,
in
this
study, binder contents ranging from 30-50 vol.
%
were
also examined
.
611