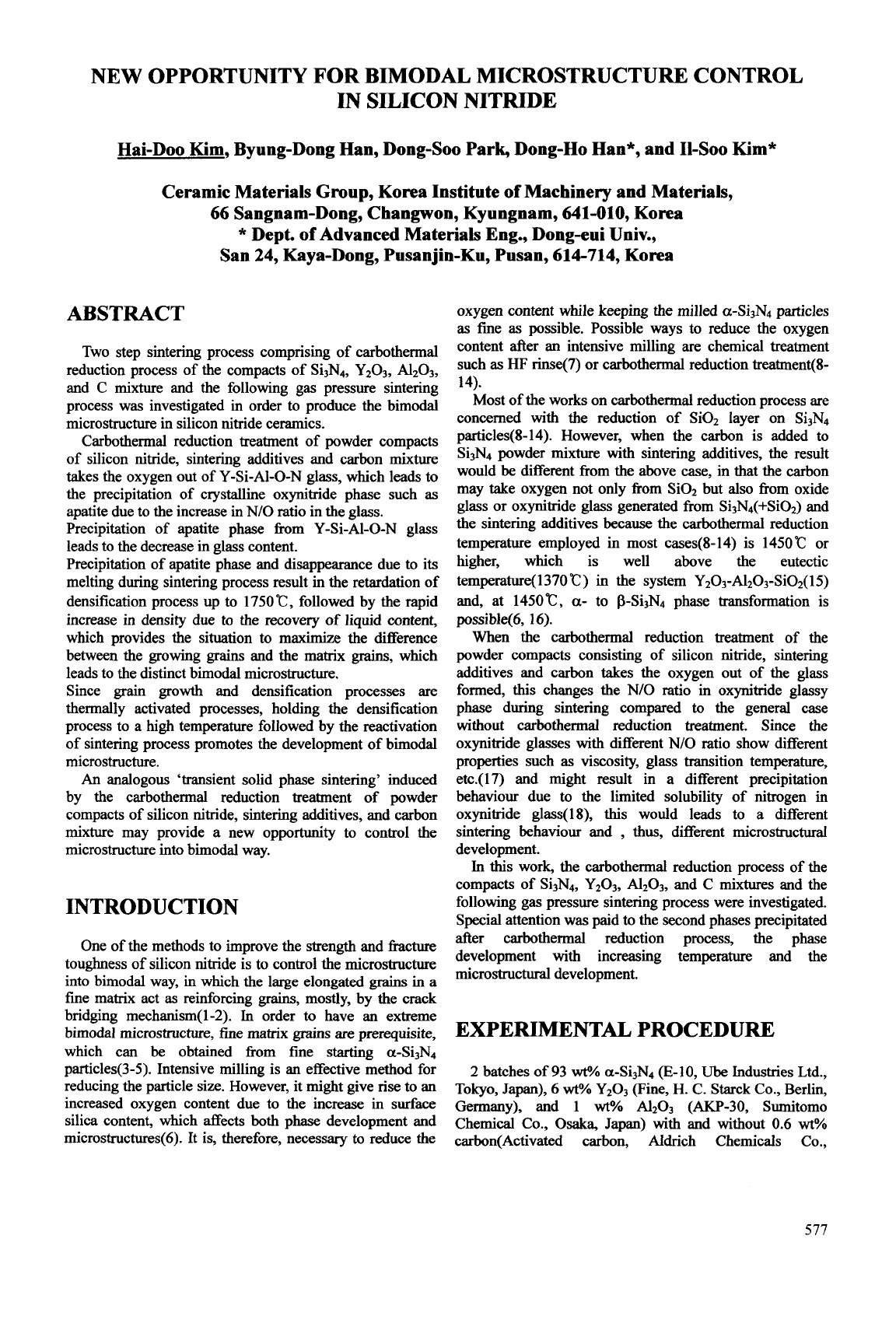
NEW OPPORTUNITY FOR BIMODAL MICROSTRUCTURE CONTROL
IN SILICON NITRIDE
Hai-Doo Kim, Byung-Dong Han, Dong-Soo Park, Dong-Ho Han*, and 11-So0 Kim*
Ceramic Materials Group, Korea Institute
of
Machinery and Materials,
66 Sangnam-Dong, Changwon, Kyungnam, 641-010, Korea
*
Dept.
of
Advanced Materials
Eng.,
Dong-eui Univ.,
San 24, Kaya-Dong, Pusanjin-Ku, Pusan, 614-714, Korea
ABSTRACT
Two step sintering process comprising of carbothermal
reduction process of the compacts of Si3N4, Y2O3, A1203,
and C mixture and the following gas pressure sintering
process was investigated in order to produce the bimodal
microstructure in silicon nitride ceramics.
Carbothermal reduction treatment of powder compacts
of silicon nitride, sintering additives and carbon
mixture
takes the oxygen out of Y-Si-Al-0-N glass, which leads to
the precipitation of crystalline oxynitride phase such
as
apatite due to the increase in
N/O
ratio in the glass.
Precipitation of apatite phase from Y-Si-A1-0-N glass
leads to the decrease in glass content.
Precipitation of apatite phase and disappearance due to its
melting during sintering process result in the retardation of
densification process up to 1750
“c
,
followed by the rapid
increase in density due to the recovery
of
liquid content,
which provides the situation to maximize the difference
between the growing grains and the matrix
grains,
which
leads to the distinct bimodal microstructure.
Since grain growth and densification processes are
thermally activated processes, holding the densification
process to a high temperature followed by the reactivation
of sintering process promotes the development of bimodal
microstructure.
An
analogous ‘transient solid phase sintering’ induced
by the carbothermal reduction treatment of powder
compacts of silicon nitride, sintering additives, and carbon
mixture may provide a new opportunity to control the
microstructure into bimodal way.
INTRODUCTION
One of the methods to improve the strength and
hture
toughness of silicon nitride is to control the microstructure
into bimodal way, in which the large elongated
grains
in a
fine matrix act
as
reinforcing grains, mostly, by the crack
bridging mechanism(1-2). In order to have an extreme
bimodal microstructure,
fine
matrix
grains
are prerequisite,
which can be obtained from fine starting a-Si3N4
particles(3-5). Intensive milling is an effective method for
reducing the particle size. However, it might give
rise
to an
increased oxygen content due to the increase in surface
silica content, which affects both phase development and
microstructures(6). It is, therefore, necessary to reduce the
oxygen content while keeping the milled a-Si3N4 particles
as
fine
as
possible. Possible ways to reduce the oxygen
content after an intensive milling are chemical treatment
such
as
HF rinse(7) or carbothermal reduction treatment(&
14).
Most of the works on carbothermal reduction process are
concerned with the reduction of SiOz layer on Si3N4
particles(8-14). However, when the carbon is added to
Si3N4 powder mixture with sintering additives, the result
would be different from the above case, in that the carbon
may take oxygen not only from Si02 but also fiom oxide
glass or oxynitride glass generated from Si3N4(+Si02) and
the sintering additives because the carbothermal reduction
temperature employed in most cases(8-14) is 1450°C or
higher, which is well above the eutectic
temperature( 1370
C
)
in the system Y203-A1203-Si02( 15)
and, at 1450C,
a-
to p-Si3N4 phase transformation is
possible(6, 16).
When
the carbothermal reduction treatment of the
powder compacts consisting of silicon nitride, sintering
additives and carbon takes the oxygen out of the glass
formed,
this
changes the N/O ratio in oxynitride glassy
phase during sintering compared to the general case
without carbothermal reduction treatment. Since the
oxynitride
glasses
with different
N/O
ratio show different
properties such
as
viscosity, glass transition temperature,
etc.(l7) and might result in a different precipitation
behaviour due to the limited solubility of nitrogen in
oxynitride glass(l8),
this
would leads to a different
sintering behaviour and
,
thus, different microstructural
development.
In
this
work, the carbothermal reduction process of the
compacts of Si3N4, Y2O3, Al2O3, and C mixtures and the
following gas pressure sintering process were investigated.
Special attention was paid to the second phases precipitated
after carbothermal reduction process, the phase
development with increasing temperature and the
microstructural development.
EXPERIMENTAL PROCEDURE
2
batches of
93
wt?!
a-Si3N4
(E-10,
Ube
Industries Ltd.,
Tokyo,
Japan),
6
wt%
Y203 (Fine, H. C. Starck Co., Berlin,
Germany), and 1
wt%
A1203
(AKP-30,
Sumitomo
Chemical Co.,
Osaka,
Japan) with and without 0.6
wt%
carbon(Activated carbon, Aldrich Chemicals Co.,
577