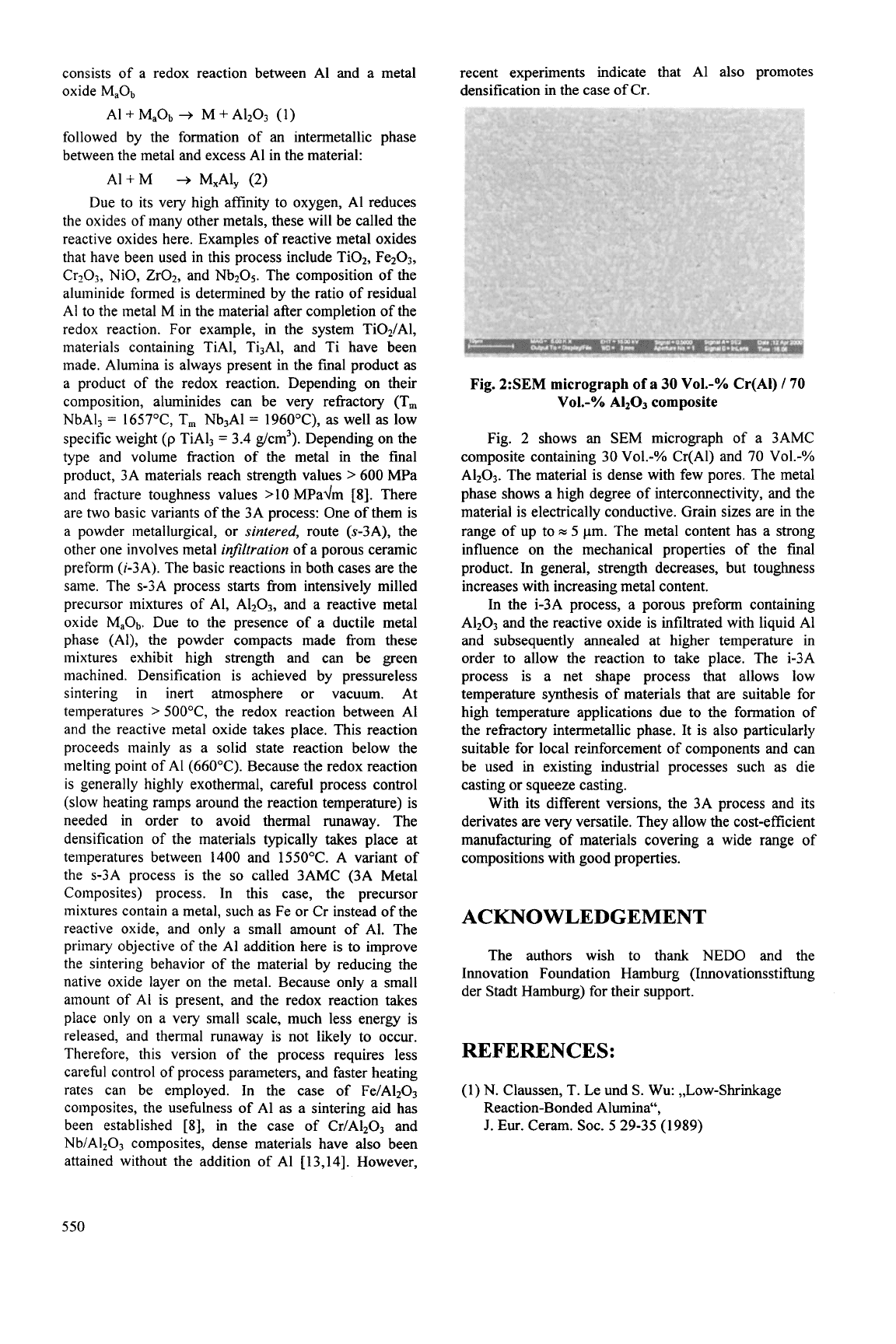
consists of a redox reaction between Al and a metal
oxide
M,Ob
followed by the formation of an intermetallic phase
between the metal and excess A1 in the material:
A]+
MaOb
+
M
i-
AI2o3 (1)
AI+M
+
M,Al,
(2)
Due to its very high affinity to oxygen, A1 reduces
the oxides of many other metals, these will be called the
reactive oxides here. Examples
of
reactive metal oxides
that have been used in this process include Ti02, Fe203,
Cr103, NiO, Zr02, and Nb205. The composition of the
aluminide formed is determined by the ratio of residual
A1 to the metal
M
in the material after completion of the
redox reaction. For example, in the system Ti02/Al,
materials containing TiAl, Ti3A1, and Ti have been
made. Alumina is always present in the final product as
a product of the redox reaction. Depending on their
composition, aluminides can be very refractory (T,
NbA13
=
1657"C, T, Nb3AI
=
1960"C), as well
as
low
specific weight
(p
TiAI3
=
3.4 g/cm3). Depending on the
type and volume fraction of the metal in the final
product, 3A materials reach strength values
>
600 MPa
and fracture toughness values >10 MPadm [8]. There
are two basic variants of the 3A process: One of them is
a powder metallurgical, or
sintered,
route (s-~A), the
other one involves metal
infiltration
of a porous ceramic
preform (i-3A). The basic reactions in both cases are the
same. The s-3A process starts from intensively milled
precursor mixtures of Al, A1203, and a reactive metal
oxide
MaOb.
Due to the presence of a ductile metal
phase (Al), the powder compacts made from these
mixtures exhibit high strength and can be green
machined. Densification is achieved by pressureless
sintering
in
inert atmosphere or vacuum. At
temperatures
>
5OO0C, the redox reaction between A1
and the reactive metal oxide takes place. This reaction
proceeds mainly as a solid state reaction below the
melting point of A1 (660°C). Because the redox reaction
is generally highly exothermal, carefkl process control
(slow heating ramps around the reaction temperature) is
needed in order to avoid thermal runaway. The
densification of the materials typically takes place at
temperatures between 1400 and 1550°C. A variant
of
the s-3A process is the
so
called 3AMC (3A Metal
Composites) process. In this case, the precursor
mixtures contain a metal, such as Fe or Cr instead of the
reactive oxide, and only a small amount
of Al. The
primary objective of the A1 addition here is to improve
the sintering behavior of the material by reducing the
native oxide layer on the metal. Because only a small
amount of
Al
is present, and the redox reaction takes
place only on a very small scale, much less energy is
released, and thermal runaway is not likely to occur.
Therefore, this version of the process requires less
careful control of process parameters, and faster heating
rates can be employed. In the case of Fe/AI2O3
composites, the usehlness of
A1
as a sintering aid has
been established [S], in the case of Cr/A1203 and
Nb/AI2O3 composites, dense materials have also been
attained without the addition of A1 [13,14]. However,
recent experiments indicate that A1 also promotes
densification in the case of Cr.
Fig.
2:SEM
micrograph
of
a
30
Vo1.-YO
Cr(A1)
/
70
Vo1.-YO
A1203
composite
Fig.
2
shows an SEM micrograph of a 3AMC
composite containing 30 Vo1.-% Cr(AI) and
70
VoL-%
A1203. The material is dense with few pores. The metal
phase shows a high degree of interconnectivity, and the
material is electrically conductive. Grain sizes are in the
range of up to
5
pm. The metal content has a strong
influence on the mechanical properties of the final
product. In general, strength decreases, but toughness
increases with increasing metal content.
In the i-3A process, a porous preform containing
A1203 and the reactive oxide is infiltrated with liquid A1
and subsequently annealed at higher temperature in
order to allow the reaction to take place. The i-3A
process is a net shape process that allows low
temperature synthesis of materials that are suitable for
high temperature applications due to the formation of
the refractory intermetallic phase. It is also particularly
suitable for local reinforcement of components and can
be used in existing industrial processes such as die
casting or squeeze casting.
With its different versions, the 3A process and its
derivates are very versatile. They allow the cost-efficient
manufacturing
of materials covering a wide range of
compositions with good properties.
ACKNOWLEDGEMENT
The authors wish to thank NED0 and the
Innovation Foundation Hamburg (Innovationsstihng
der Stadt Hamburg) for their support.
REFERENCES:
(1) N. Claussen, T. Le und
S.
Wu: ,,Low-Shrinkage
Reaction-Bonded Alumina",
J.
Eur. Ceram. SOC.
5
29-35 (1989)
550