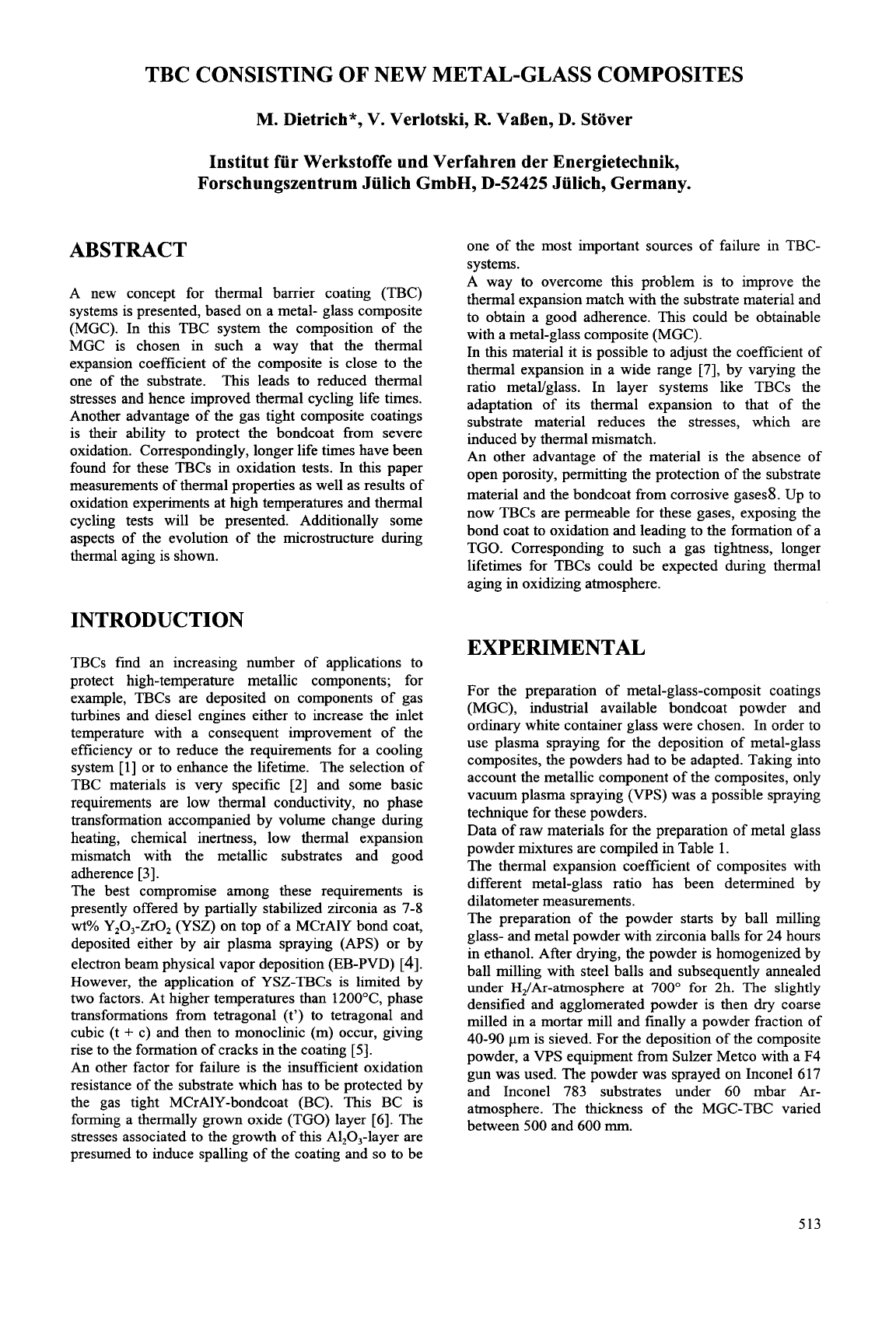
TBC CONSISTING
OF
NEW METAL-GLASS COMPOSITES
M. Dietrich*, V. Verlotski,
R.
VaDen, D. Stover
Institut fur Werkstoffe und Verfahren der Energietechnik,
Forschungszentrum Jiilich GmbH,
D-52425
Jiilich, Germany.
ABSTRACT
A new concept for thermal barrier coating (TBC)
systems is presented, based on a metal- glass composite
(MGC). In this TBC system the composition of the
MGC is chosen in such a way that the thermal
expansion coefficient of the composite is close to the
one of the substrate. This leads to reduced thermal
stresses and hence improved thermal cycling life times.
Another advantage of the gas tight composite coatings
is their ability to protect the bondcoat from severe
oxidation. Correspondingly, longer life times have been
found for these
TBCs
in oxidation tests. In this paper
measurements of thermal properties as well as results of
oxidation experiments at high temperatures and thermal
cycling tests will be presented. Additionally some
aspects of the evolution of the microstructure during
thermal aging is shown.
INTRODUCTION
TBCs find an increasing number of applications to
protect high-temperature metallic components; for
example, TBCs are deposited on components of gas
turbines and diesel engines either to increase the inlet
temperature with a consequent improvement of the
efficiency or to reduce the requirements for a cooling
system [l] or to enhance the lifetime. The selection of
TBC materials is very specific [2] and some basic
requirements are low thermal conductivity, no phase
transformation accompanied by volume change during
heating, chemical inertness, low thermal expansion
mismatch with the metallic substrates and good
adherence [3].
The best compromise among these requirements is
presently offered by partially stabilized zirconia as
7-8
wt% Y,O,-ZrO, (YSZ) on top of a MCrAlY bond coat,
deposited either by air plasma spraying (APS) or by
electron beam physical vapor deposition (EB-PVD)
[4].
However, the application
of
YSZ-TBCs is limited by
two
factors. At higher temperatures than
1200"C,
phase
transformations from tetragonal (t') to tetragonal and
cubic (t
+
c) and then to monoclinic (m) occur, giving
rise to the formation of cracks in the coating
[5].
An other factor for failure is the insufficient oxidation
resistance of the substrate which has to be protected by
the gas tight MCrAlY-bondcoat (BC). This BC is
forming a thermally grown oxide (TGO) layer [6]. The
stresses associated to the growth of this Al,O,-layer are
presumed to induce spalling of the coating and
so
to be
one
of
the most important sources of failure in TBC-
systems.
A way to overcome this problem is to improve the
thermal expansion match with the substrate material and
to obtain a good adherence. This could be obtainable
with a metal-glass composite (MGC).
In this material it is possible to adjust the coefficient of
thermal expansion in a wide range [7], by varying the
ratio metayglass. In layer systems like TBCs the
adaptation of its thermal expansion to that of the
substrate material reduces the stresses, which are
induced by thermal mismatch.
An other advantage of the material is the absence of
open porosity, permitting the protection of the substrate
material and the bondcoat from corrosive gases8. Up to
now
TBCs
are permeable for these gases, exposing the
bond coat to oxidation and leading to the formation of a
TGO. Corresponding to such a gas tightness, longer
lifetimes for TBCs could be expected during thermal
aging in oxidizing atmosphere.
EXPERIMENTAL
For the preparation of metal-glass-composit coatings
(MGC), industrial available bondcoat powder and
ordinary white container glass were chosen. In order to
use plasma spraying for the deposition of metal-glass
composites, the powders had to be adapted. Taking into
account the metallic component of the composites, only
vacuum plasma spraying
(VPS)
was a possible spraying
technique for these powders.
Data of raw materials for the preparation of metal glass
powder mixtures are compiled in Table 1.
The thermal expansion coefficient of composites with
different metal-glass ratio has been determined by
dilatometer measurements.
The preparation of the powder starts by ball milling
glass- and metal powder with zirconia balls for 24 hours
in ethanol. After drying, the powder is homogenized by
ball milling with steel balls and subsequently annealed
under HJAr-atmosphere at
700"
for 2h.
The
slightly
densified and agglomerated powder is then dry coarse
milled in a mortar mill and finally a powder fraction of
40-90 pm is sieved. For the deposition of the composite
powder, a VPS equipment from Sulzer Metco with a F4
gun was used. The powder was sprayed on Inconel 617
and Inconel 783 substrates under 60 mbar Ar-
atmosphere. The thickness of the MGC-TBC varied
between
500
and 600
nun.
513