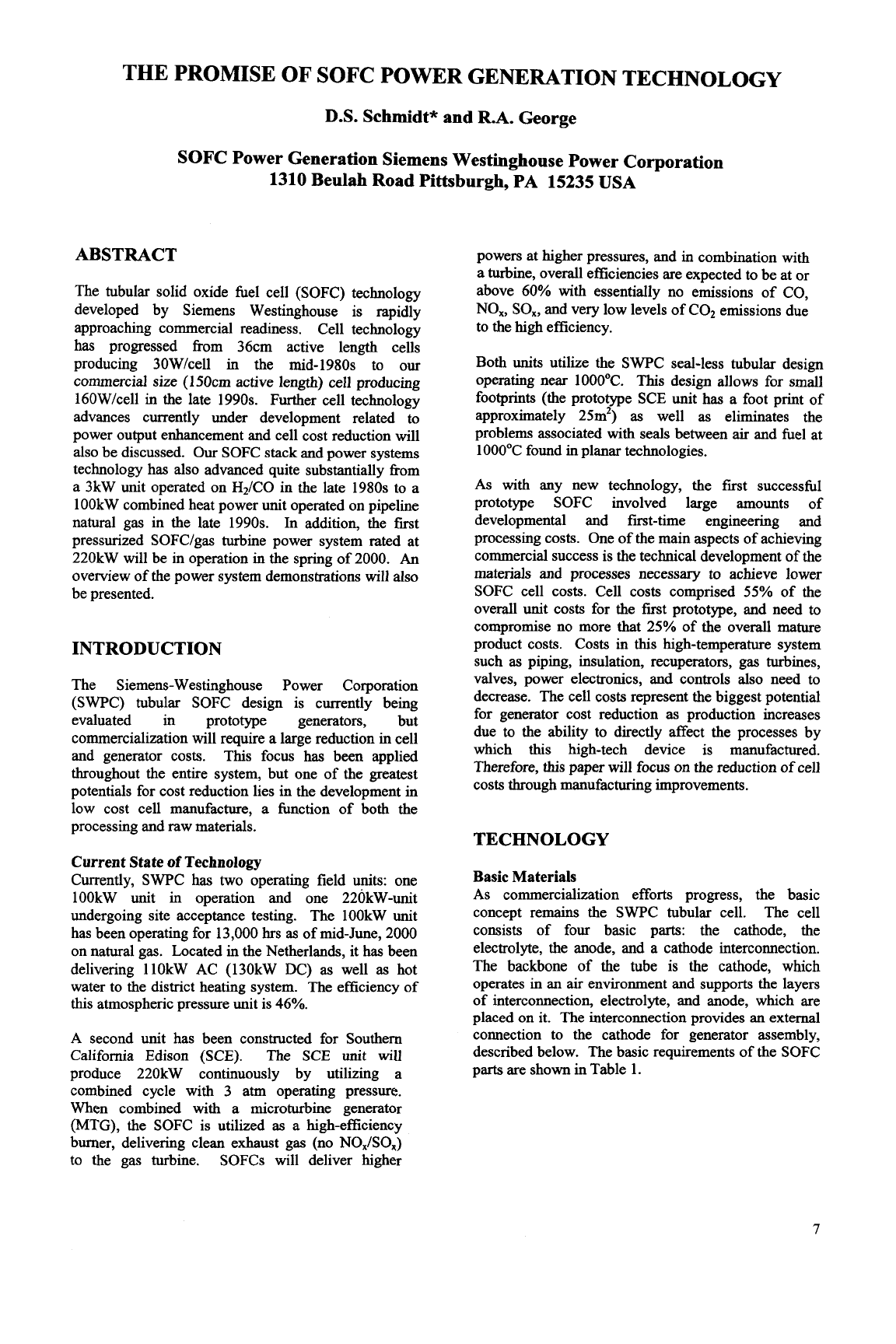
THE PROMISE
OF
SOFC POWER GENERATION TECHNOLOGY
D.S. Schmidt* and R.A. George
SOFC Power Generation Siemens Westinghouse Power Corporation
1310 Beulah Road Pittsburgh, PA 15235 USA
ABSTRACT
The tubular solid oxide fuel cell (SOFC) technology
developed by Siemens Westinghouse is rapidly
approaching commercial readiness. Cell technology
has progressed from 36cm active length cells
producing 30W/cell in the mid-1980s to our
commercial size (150cm active length) cell producing
160W/cell in the late 1990s. Further cell technology
advances currently under development related to
power output enhancement and cell cost reduction will
also be discussed. Our SOFC stack and power systems
technology has also advanced quite substantially from
a 3kW
unit
operated on H2/C0 in the late 1980s
to
a
lOOkW combined heat power unit operated
on
pipeline
natural gas in the late 1990s. In addition, the first
pressurized SOFC/gas turbine power system rated at
220kW will be in operation in the spring of 2000.
An
overview of the power system demonstrations will also
be presented.
INTRODUCTION
The Siemens-Westinghouse Power Corporation
(SWPC) tubular SOFC design is currently being
evaluated in prototype generators, but
commercialization will require a large reduction in cell
and generator costs. This focus
has
been applied
throughout the entire system, but one of the greatest
potentials for cost reduction lies in the development in
low cost cell manufacture, a function of both the
processing and raw materials.
Current State
of
Technology
Currently, SWPC has two operating field units: one
lOOkW unit in operation and one 22OkW-unit
undergoing site acceptance testing. The lOOkW unit
has been operating for 13,000
hrs
as
of
mid-June, 2000
on natural gas. Located in the Netherlands, it has been
delivering 1lOkW AC (130kW DC)
as
well
as
hot
water to the district heating system. The efficiency
of
this atmospheric pressure unit is 46%.
A
second unit has been constructed for southern
California Edison (SCE). The SCE
unit
will
produce 220kW continuously by utilizing a
combined cycle with 3 atm operating pressure.
When combined with a microturbine generator
(MTG),
the SOFC is utilized
as
a high-efficiency
burner, delivering clean exhaust gas (no
NO,/SO,)
to the gas turbine. SOFCs will deliver higher
powers at higher pressures, and in combination with
a turbine, overall efficiencies are expected to be at or
above 60% with essentially
no
emissions of CO,
NO,,
SO,,
and very low levels of CO1 emissions due
to the high efficiency.
Both units utilize the SWPC seal-less tubular design
operating near 1000°C.
This
design allows for small
footprints (the prototype SCE unit has a foot print
of
approximately 25m2)
as
well
as
eliminates the
problems associated with seals between
air
and fuel at
1000°C found
in
planar technologies.
As
with any new technology, the fxst successful
prototype SOFC involved large amounts of
developmental and first-time engineering and
processing costs. One of the main aspects of achieving
commercial success is the technical development of the
materials and processes necessary to achieve lower
SOFC cell costs. Cell costs comprised
55%
of
the
overall unit costs for the first prototype, and need to
compromise no more that 25% of the overall mature
product costs. Costs
in
this
high-temperature system
such
as
piping, insulation, recuperators, gas turbines,
valves, power electronics, and controls also need to
decrease. The cell costs represent the biggest potential
for generator cost reduction
as
production increases
due to the ability to directly affect the processes by
which
this
high-tech device is manufactured.
Therefore,
this
paper will focus
on
the reduction of cell
costs through manufacturing improvements.
TECHNOLOGY
Basic Materials
As
commercialization efforts progress, the basic
concept remains the SWPC tubular cell. The cell
consists of four basic parts: the cathode, the
electrolyte, the anode, and a cathode interconnection.
The backbone
of
the tube
is
the cathode, which
operates
in
an air environment and supports the layers
of interconnection, electrolyte, and anode, which are
placed on it. The interconnection provides an external
connection to the cathode for generator assembly,
described below. The basic requirements
of
the SOFC
parts are shown
in
Table 1.
7