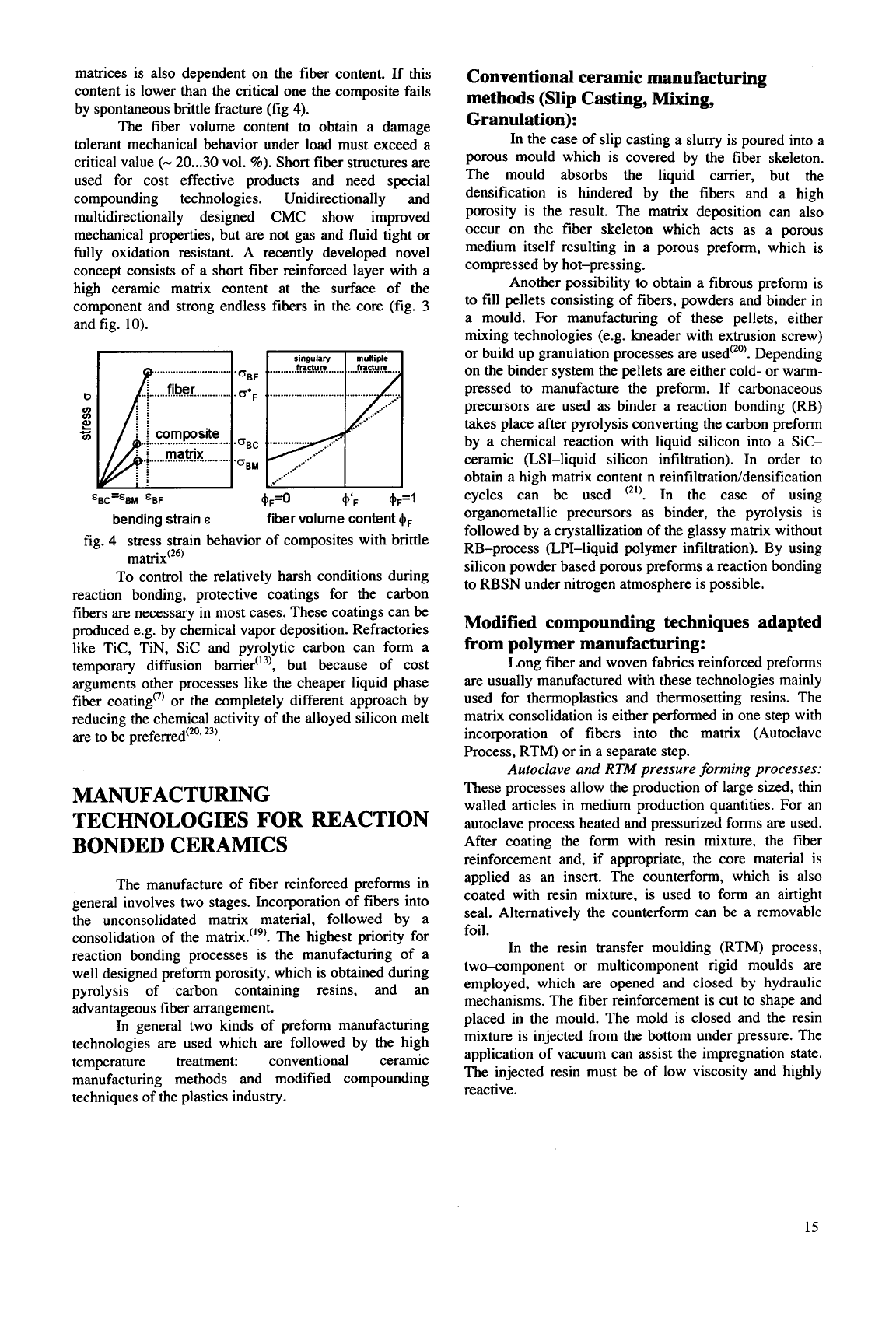
matrices is also dependent on the fiber content. If this
content is lower than the critical one the composite fails
by spontaneous brittle fracture (fig
4).
The fiber volume content to obtain a damage
tolerant mechanical behavior under load must exceed a
critical value
(-
20 ...
30
vol.
%).
Short fiber structures are
used for cost effective products and need special
compounding technologies. Unidirectionally and
multidirectionally designed CMC show improved
mechanical properties, but are not gas and fluid tight or
fully oxidation resistant. A recently developed novel
concept consists of a short fiber reinforced layer with a
high ceramic matrix content at the surface of the
component and strong endless fibers in the core (fig.
3
and fig.
10).
singulary
multiple
oBF
fnctun
fnctun
....................
............................................
b
.......
8
s!
.....
-
u)
...................
.......
....
,.-”’
........
‘BC=‘BM
‘BF
4F=o
4‘F
+F=l
bending strain
E
fiber volume content
c$F
fig.
4
stress strain behavior of composites with brittle
matrix(26’
To control the relatively harsh conditions during
reaction bonding, protective coatings for the carbon
fibers are necessary in most cases. These coatings can be
produced e.g. by chemical vapor deposition. Refractories
like TIC, TiN, Sic and pyrolytic carbon can form a
temporary diffusion barrier“3’, but because of cost
arguments other processes like the cheaper liquid phase
fiber coating”’ or the completely different approach by
reducing the chemical activity of the alloyed silicon melt
are to be preferred(”,
23’.
MANUFACTURING
TECHNOLOGIES FOR REACTION
BONDED CERAMICS
The manufacture of fiber reinforced preforms in
general involves two stages. Incorporation of fibers into
the unconsolidated matrix material, followed by a
consolidation of the matrix.(”’. The highest priority for
reaction bonding processes is the manufacturing of a
well designed preform porosity, which is obtained during
pyrolysis of carbon containing resins, and an
advantageous fiber arrangement.
In general two kinds of preform manufacturing
technologies are used which
are
followed by the high
temperature treatment: conventional ceramic
manufacturing methods and modified compounding
techniques of the plastics industry.
Conventional ceramic manufacturing
methods (Slip Casting, Mixing,
Granulation):
In the case of slip casting a slurry is poured into a
porous mould which is covered by the fiber skeleton.
The mould absorbs the liquid carrier, but the
densification is hindered by the fibers and a high
porosity is the result. The matrix deposition can also
occur on the fiber skeleton which acts as a porous
medium itself resulting in a porous preform, which is
compressed by hot-pressing.
Another possibility to obtain a fibrous preform
is
to fill pellets consisting of fibers, powders and binder in
a mould. For manufacturing of these pellets, either
mixing technologies (e.g. kneader with extrusion screw)
or build up granulation processes
are
used(20’. Depending
on the binder system
the
pellets are either cold- or warm-
pressed to manufacture the preform. If carbonaceous
precursors are used as binder a reaction bonding (RB)
takes place after pyrolysis converting the carbon preform
by a chemical reaction with liquid silicon into a SiC-
ceramic (LSI-liquid silicon infiltration). In order to
obtain a high matrix content n
reinfiltratioddensification
cycles can
be
used
(21).
In the case of using
organometallic precursors as binder, the pyrolysis is
followed by a crystallization of the glassy matrix without
RB-process (LPI-liquid polymer infiltration). By using
silicon powder based porous preforms a reaction bonding
to RBSN under nitrogen atmosphere is possible.
Modified compounding techniques adapted
from polymer manufacturing:
Long fiber and woven fabrics reinforced preforms
are usually manufactured with these technologies mainly
used for thermoplastics and thermosetting resins. The
matrix consolidation is either performed in one step with
incorporation of fibers into the matrix (Autoclave
Process, RTM) or in a separate step.
Autoclave and
RTM
pressure
forming
processes:
These processes allow the production of large sized, thin
walled articles in medium production quantities. For an
autoclave process heated and pressurized forms are used.
After coating the form with resin mixture, the fiber
reinforcement and, if appropriate, the core material is
applied as an insert. The counterform, which is also
coated with resin mixture, is used to form an airtight
seal. Alternatively the counterform can be a removable
foil.
In the resin transfer moulding (RTM) process,
two-component or multicomponent rigid moulds are
employed, which are opened and closed by hydraulic
mechanisms. The fiber reinforcement is cut
to
shape and
placed in the mould. The mold is closed and the resin
mixture is injected from the bottom under pressure. The
application of vacuum can assist the impregnation state.
The injected resin must
be
of low viscosity and highly
reactive.
15