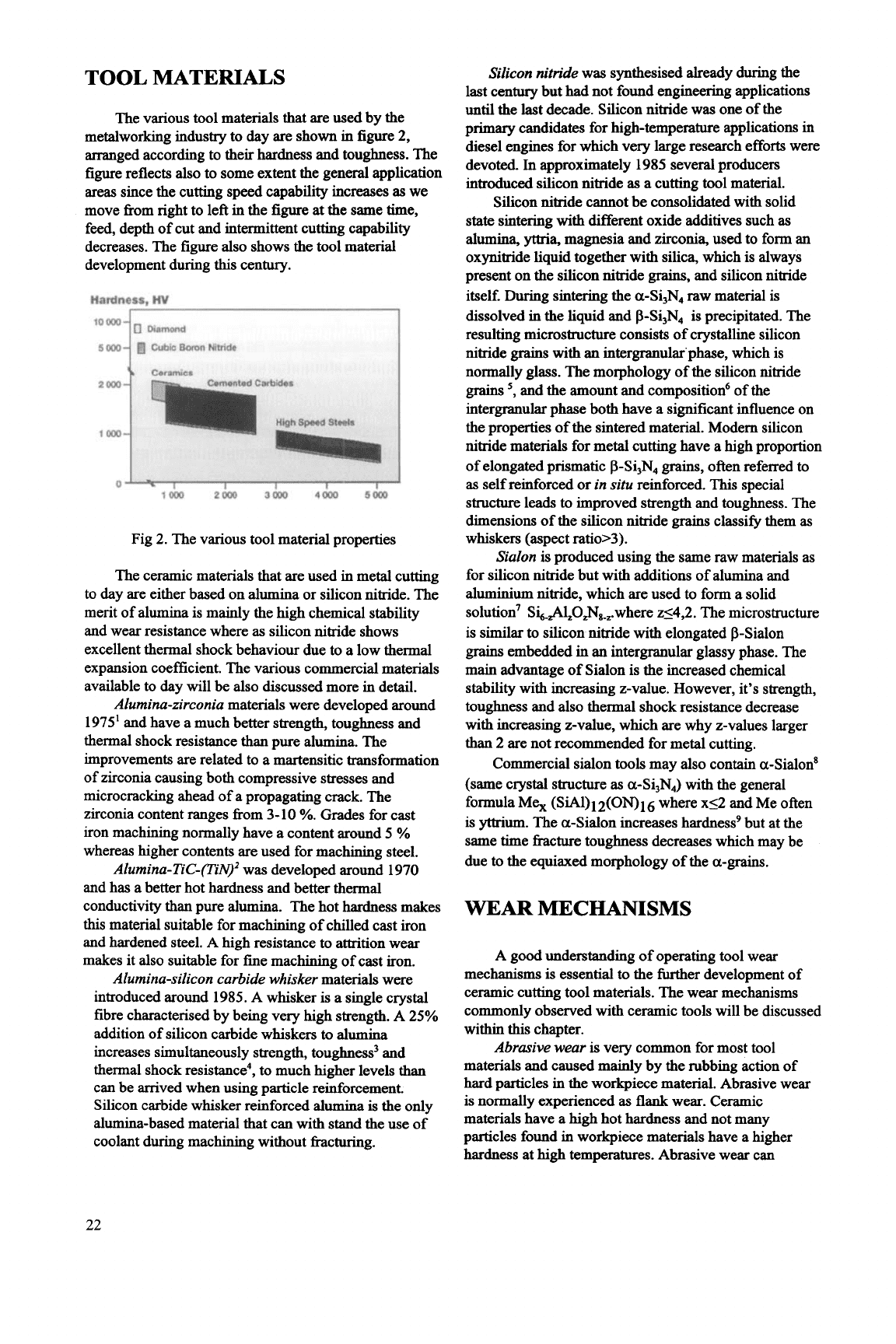
TOOL MATERIALS
The various tool materials that are used by the
metalworking industry to day are shown in figure
2,
arranged according to their hardness and toughness. The
figure reflects also to some extent the general application
areas since the cutting speed capability increases
as
we
move fiom right to left in the figure at the same time,
feed, depth of cut and intermittent cutting capability
decreases. The figure also shows the tool material
development during
this
century.
.,-
ftennrerse
Rupture
Stre-
Wmm*
Fig
2.
The various tool material properties
The ceramic materials that are used in metal cutting
to day are either based
on
alumina or silicon nitride. The
merit of alumina is mainly the high chemical stability
and wear resistance where
as
silicon nitride shows
excellent thermal shock behaviour due
to
a low thermal
expansion coefficient. The various commercial materials
available to day will be also discussed more in detail.
Alumina-zirconia
materials were developed around
1975' and have a much better strength, toughness and
thermal shock resistance than pure alumina. The
improvements are related to a martensitic transformation
of zirconia causing both compressive stresses and
microcracking ahead of a propagating crack. The
zirconia content ranges from 3-10
YO.
Grades for cast
iron machining normally have a content around
5
%
whereas higher contents are used for machining steel.
Alumina-TiC-(TiN)'
was developed around 1970
and has a better hot hardness and better thermal
conductivity than pure alumina. The hot hardness makes
this material suitable for machining of chilled cast iron
and hardened steel. A high resistance to
attrition
wear
makes it also suitable for fine machining of cast iron.
Alumina-silicon carbide whisker
materials were
introduced around 1985. A whisker is a single crystal
fibre characterised by being very high strength. A 25%
addition of silicon carbide whiskers
to
alumina
increases simultaneously strength, toughness3 and
thermal shock resistance4, to much higher levels
than
can be arrived when using particle reinforcement.
Silicon carbide whisker reinforced alumina is the only
alumina-based material that can with stand the use of
coolant during machining without fi-acturing.
Silicon nitride
was synthesised already during the
last century but
had
not found engineering applications
until the last decade. Silicon nitride was one of the
primary candidates for high-temperature applications in
diesel engines for which very large research efforts were
devoted.
In
approximately 1985 several producers
introduced silicon nitride
as
a cutting tool material.
Silicon nitride cannot be consolidated with solid
state sintering with different oxide additives such
as
alumina,
yttria,
magnesia and zirconia, used to form an
oxynitride liquid together with silica, which
is
always
present
on
the silicon nitride
grains,
and silicon nitride
itself. During sintering the a-Si3N4 raw material is
dissolved in the liquid and p-Si3N4 is precipitated. The
resulting microstructure consists of crystalline silicon
nitride
grains
with an intergranular'phase, which is
normally glass. The morphology of the silicon nitride
grains
5,
and the amount and composition6 of the
intergranular phase both have a significant influence
on
the properties of the sintered material. Modem silicon
nitride materials for metal cutting have a high proportion
of elongated prismatic p-Si3N4
grains,
often
referred to
as
self reinforced or
in situ
reinforced.
This
special
structure leads to improved strength and toughness. The
dimensions of the silicon nitride
grains
classify them
as
whiskers (aspect ratio>3).
Sialon
is produced using the same raw materials
as
for silicon nitride but with additions of alumina and
aluminium nitride, which are used to form a solid
solution' S&Al,ON,-,.where z54,2. The microstructure
is similar to silicon nitride with elongated p-Sialon
grains
embedded
in
an intergranular glassy phase. The
main advantage of Sialon is the increased chemical
stability with increasing z-value. However, it's strength,
toughness and also thermal shock resistance decrease
with increasing z-value, which are why z-values larger
than
2 are not recommended for metal cutting.
Commercial sialon tools may also contain a-sialon'
(same crystal structure
as
a-Si3N4) with the general
formula Me, (SiAl)12(ON)16 where x52 and Me often
is yttrium. The a-Sialon increases hardness' but at the
same time fracture toughness decreases which may be
due
to
the equiaxed morphology of the a-grains.
WEAR
MECHANISMS
A
good understanding of operating tool wear
mechanisms
is
essential to the further development of
ceramic cutting tool materials. The wear mechanisms
commonly observed with ceramic tools will be discussed
within
this
chapter.
Abrasive wear
is
very common for most tool
materials and caused mainly by the rubbing action of
hard particles in the workpiece material. Abrasive wear
is normally experienced
as
flank
wear. Ceramic
materials have a high hot hardness and not many
particles found in workpiece materials have a higher
hardness at high temperatures. Abrasive wear can
22